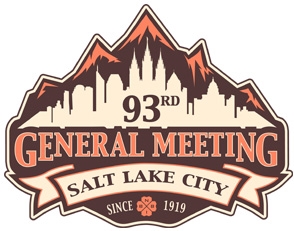
93rd General Meeting Presentation
Use of ASME Boiler & Pressure Vessel Code Globally
Luca Costa
The following remarks were delivered at the General Session of the 93rd General Meeting on May 12, 2025. It has been edited for content and phrasing.
INTRODUCTION: Dr. Luca Costa is the CEO of the International Institute of Welding (IIW). He served in the Italian Navy from 1999 to 2000 and was employed in the Engineering Department for IIS Service in 2000. In 2000, IIS and the International Institute of Welding (IIW) awarded him the International Welding Engineer (IWE) diploma. Dr. Costa has written several papers on the environment, health and safety, welding technology, and fabrication, which have been published in national reviews. He also co-authored several books and manuals dealing with welding and non-destructive testing.
His slide presentation can be found here.
DR. COSTA: Good afternoon, everyone. Here is what I would like to present to you today. And I will start with some apologies, and I have to apologize for my own biases because I have at least three.
First, I'm Italian, so please apologize for my poor English. I'll do my best to speak as well as I can, but it also involves technical and cultural background, which might be different from yours.
The second reason I am biased is that I am an engineer. And that's the kind of disease, as most of you know, you get at the university and you can’t get rid of. The third reason, and probably the most important bias I have, is that I am a welding engineer. That's something in my genes, as my father was also in the welding industry. Everything I'm representing to you today is biased by my welding background.
I want to say a few words about the International Institute of Welding, to help you understand the source of the information I'm presenting to you. The International Institute of Welding is a not-for-profit, and it’s the associations of the welding associations and institutes around the world. AWS is one of our founding members.
We have 13 founding members, and currently, 53 countries are represented, as shown in the picture. You can realize that there is one country with a different color. IIW is based in Italy. According to European legislation, we cannot work with Russia, so the Russian member is currently suspended.
The IIW is engaged in numerous activities. First, it's a standardization body recognized by the ISO, which is the International Standardization Organization. It's engaged in the publication of deliverables and in the production of deliverables. Many of the concepts used in the welding sector originate from the IIW, and probably the most known is the carbon equivalent formula. It's a so-called IIW carbon equivalent formula because the IIW has developed it.
Next, we have a system for the qualification and certification of personnel. I will touch on that a little bit later. And then, we also have a set of legacy programs. Like everyone, we are deeply concerned about the future of our industry, and we are working on programs to address this situation. Our strongest focus is the exchange of knowledge. We work through a collaborative working platform, and everyone is invited to join us and to participate in our activities.
Here is a short overview of our technical production standards. We have a technical journal and publish numerous books. The way we work is through scientific commissions, covering every aspect of welding from materials, technologies, safety, design, education, training, and so forth.
Our system for qualifying and certifying personnel utilizes worldwide-recognized diplomas, with centralized management of examinations. However, the examinations are conducted in the national language, which is a strong feature of our system. As you can see, 193,000 individuals worldwide hold an IIW diploma.
Let’s get to the scope of my presentation, which is understanding how the ASME codes and standards are globally used and understanding how, how much, and why.
First of all, there is no international standard dealing with pressure equipment and boilers. I would call it a framework standard. It's very weak. It does nothing to deal with any other standard you will find in the world. So, what is available globally? What is a driver globally?
The strongest driver is the regulatory requirements. Manufacturers should adopt a specific code because there is a national standard, and countries such as the U.S., Canada, or China have their own local codes. There is an entirely different approach in Europe, which refers to essential safety requirements. That means that no matter how you do it, it should be safe. The approach is that these are the essential safety requirements that you have to respect. Feel free to use the code that you want.
The third approach refers to standards from other countries. I was quite impressed when I learned that in India the national boiler and pressure vessels code is the ASME Code. It’s as simple as that. The fourth case is the biggest surprise I have faced in my professional life. It's a case of countries like the Republic of Korea, which we consider a developed country, not having requirements for manufacturing. They don't even have a national requirement for welders. You don’t need to be a qualified welder to weld in Korea.
Of course, then, it's up to the manufacturer or the main contractor, but there is no requirement for a welder to be qualified against any kind of standard. That was really surprising to me.
During my preparation for today, I did a survey on the use of standards and codes. I tried to contact big manufacturers, and I got replies from four. Two of them didn't want to be mentioned by name, so I will refer to them as Manufacturer A and Manufacturer B. One is a major manufacturer in Italy, and the other is a major manufacturer in Japan.
The question concerned the production of pressure vessels, with a focus on pressure vessels for known nuclear applications. Considering that case, how many pressure vessels are you currently producing and delivering in accordance with the ASME Boiler and Pressure Vessel Code? Manufacturer A in Italy, 90%. Westinghouse, a huge international manufacturer, 80%. Larsen & Toubro, an immense manufacturing company in India and one of the largest in the world, 100%. Manufacturer B in Japan, 30%.
What are the others? Well, that depends on where the manufacturers are. Not surprisingly, the manufacturer in Italy, the other 10% is various, so several standards are used because they are producing and delivering all over the world. Westinghouse is focused on the European market, so it is using the EN standard for pressure vessels and unfired pressure vessels. The manufacturer in Japan for the domestic market refers to the national domestic standard or code for pressure vessels.
The other section of my survey focused on Europe. And that comes from my first bias. In Europe, three countries were investigated, and there they are among the biggest welding manufacturers in Europe. Germany is the biggest one, and Italy is the second.
Germany is more focused on the national products, and Italy is more focused on the global markets. So as you can see from the screen, 10%, 19%, 50% – the European standard. Then look at the ASME Boiler and Pressure Vessel Code, 80% in Italy and 50% in Spain.
For those familiar with the German market, it is particularly focused on its national standards. They have a system for national standards. So, 80%, you see, is their national standard for pressure vessels.
What is the conclusion of that? It's very simple. ASME Boiler and Pressure Vessel Code is the most widely used code for the production of pressure vessels. Everything that is discussed during ASME committee meetings has an impact that is much wider than what they probably expect.
This other slide focuses on the ASME certificate holders. I also need to clarify that not all the products you saw on the side of the slide were produced by certificate holders, which is a form of distortion in the system. This is a survey of ASME certificate holders in Italy. Please remember Italy is the largest producer of welded parts for known domestic products, known domestic customers. And not surprisingly, 44% of that production goes to North America, and 33% goes to the Middle East. Something is going to North Africa, and something is going to the Far East. That's not a big surprise, and most of them are in oil and gas industry.
So what is the difference? That's probably one of the things stemming from my first bias, being Italian and European in that respect. There is a completely different approach to managing welding applications. There are two approaches that you can find in any standard. At the basis of everything, we have welders and welding procedures. You cannot produce any welding if you don't have welders and welding procedures.
As we all know, you need qualification records and manufacturing and inspection plans, but the point is, what should be written in those manufacturing and inspection plans? Here, the two philosophies come out. One approach is you can do whatever you want, provided it is written on the code.
So you look at the code and see if it is allowed or not. If it is not allowed, you can't do it. That's simple. I know the code is thick, but every answer is there or is expected to be there. Then you need an inspector, who is the person checking that what is written in the code is reflected in the manufacturing and inspection planning. I would say that’s the easy one.
The other one is when you have a standard, which is different than a code. A standard is something that puts constraints on things but does not exactly tell you what you should do. It's telling you what you cannot do. It's the opposite. If everything within the standard is OK, then you need another very important professional in the field, who is called the coordinator.
The word “coordinator” may not be one of the best, because when I think of a coordinator, I'm always thinking of someone sitting behind a desk and watching others work. That's not the case. The coordinator is the person responsible for designing the manufacturing and inspection plan, taking into account the constraints, even by the standards. Therefore, he has a much broader role and the responsibility to demonstrate that what he's considering is safe. So that's much more difficult, and that's my original technical background. I was trained as a welding engineer to become a welding coordinator, not a welding inspector. This is reflected in what you see when we examine one of the most iconic and important brands of the International Institute of Welding, namely the International Welding Engineer. I am an International Welding Engineer because of my background.
If you look at the numbers, you'll see a few spikes in the number of International Welding Engineers, which represents the highest level of welding coordination personnel. You can see that several countries are listed. It's not difficult to find. They are sorted in alphabetical order. It's missing the United States, and this is not because there are no good welding engineers. I know many outstanding welding engineers in this country, but that's largely due to the different manufacturing philosophies, which are based on codes.
So, how does that fit with the widespread use of the ASME code globally, the fact that it is a code and is not the standard? Why are there so many International Welding Engineers around the world if most of the world in the field of pressure vessels use the ASME Code?
To illustrate this, I will use an example from Europe, as it provides a clear explanation to the question. How is it possible in a country where the cultural background and the technical background are focused on standards and code coordinators? How is it possible that the ASME Code is so widely used in Europe?
I don't want to be boring, so I'll be very short, but here are a few words about the Pressure Equipment Directive, which is the rule that governs the manufacturing, installation, and service of boilers and pressure vessels in Europe. It is based on essential safety requirements. It's still heavily influenced by the European cultural background in manufacturing. You can do whatever you do, provided it is safe.
So the directives just state what the essential safety requirements are for a pressure vessel? There are very few technical requirements. All the rest is free for the manufacturer to choose how to demonstrate that.
That approach, quite frankly, is quite poor, because if you have the opportunity to review the Pressure Equipment Directive, you will realize that there is not much written. The main point in the Pressure Equipment Directive is that there are two ways to comply with the directive. One way is to use the harmonized standards, which are standards like the ASME Boiler and Pressure Vessel Code, which guarantee what is called the presumption of conformity. That means if you use a standard, which is simply a set of constraints, you are automatically compliant with the PED requirements and directive. But other standards may be used, provided the manufacturer demonstrates compliance with the European, with the Essential Safety Requirements. Therefore, manufacturers are free to use the ASME Boiler and Pressure Vessel Code.
This is the picture of all the European harmonized standards. I have a good friend in Sweden who is keeping us up to date every six months. If you are building a pressure vessel, you purchase the necessary code books from the ASME, and you have everything you need inside. Here you go, cherry-picking the different standards you need to use to produce your product. For example, if you are a manufacturer using pressure vessels made of carbon steel that are welded using conventional welding processes, you need 35 standards, which is significantly cheaper than purchasing the full ASME code books that you would need. So that's an advantage.
How does it work with the ASME Boiler and Pressure Vessel Code in Europe? Well, the ASME stamp is not recognized. The manufacturer can use the Boiler and Pressure Vessel Code, but the conformity assessment is done by a notified body, which is a nationally authorized body for inspection and verification of conformity. And that explains the distortion I was talking about before. The second thing you can use is the ASME Boiler and Pressure Vessel Code, but you have to restrict its use to those safety requirements provided by the European directive to make a practical example.
Let's take one of the most commonly used materials, tubes and piping, which is the ASTM A106 Grade B, probably the most widely used. You can use it, but its carbon content should be lower than 0.23%, because that's an essential requirement of the PED.
Another interesting point is that impact testing is always required. Always. Independent of the temperature and material, impact testing must always be performed during the qualification of welding procedures.
The third good example is that the welders' qualifications expire every two years, and the welders' qualifications and the PQRs cannot be certified by the manufacturer. A notified body should qualify it. Now you can see some distortions that force the manufacturer to use only a subsection of the code, rather than the entire code, in order to fulfill the directive's requirements.
These may result in severe restrictions on applications. Nevertheless, as I said, it is still widely used in Europe. We should wonder why, and that's on my last slide. There is a bubble or a technical island in Europe, which is the nuclear sector. And that's because the approach to nuclear energy in Europe varies significantly from country to country.
Let me express my opinion. Unfortunately, we cannot build any nuclear power sources in Italy, but we have plenty of nuclear power sources from our neighbors in France, as you can see from the picture. Therefore, it’s an option to use the Boiler and Pressure Vessel Code, but then it is still up to the national organization of nuclear safety for the site. The largest one is in France, and France has its own code so they’re not using it. That's different from other countries.
The last point I wanted to touch on is another key difference between the European and international standards and the standardization approach used here, where the ASME committees meet. This is based on my experience as a delegate to the ASME Section IX Committee and my deep involvement in ISO standardization.
What you see here is just a small part of the steps required for a new standard or a revision of an existing standard. The first step is to ask all member bodies of ISO worldwide if there is a need for a revision of a standard. This happens every five years. Then you go to a preparatory stage where a working group of experts is formed. It’s a new group every time. Then you have a committee stage where you start discussing, followed by an inquiry stage, then an approval stage, and finally the publication stage.
The target for ISO publication time is two years, and if you think of what is happening again in the rooms that are just close to us, where every meeting you have revisions, interpretations, new items, and new discussions, you should feel very lucky. And I can tell by my experiences that while some others in the room have the same experience, maybe they cannot be as frank as I am: Attending an ASME committee is exciting. Attending an ISO committee is boring. Nothing happens. Then why is it so widely used?
First of all, and that's my own interpretation, there is a historical reason because, according to my research, the 1914 edition of the code was the first.
Second question: easy access. That's a question mark, because I think it's easier to find a place where you can have all the requirements in a single book. However, I have already mentioned that by cherry-picking standards, you may save a lot of money. The third reason is coverage, because it's accepted widely and globally.
The fourth reason is that it continuously updates. Before I had this job, I was a trainer for welding engineers. When I was explaining differences, I always used to say the ASME Code is a live code. The ISO standards need to be reactivated periodically. The main reason is that it's imposed by regulations. That's the easiest one – specifications, and that's for those who are using the equipment or manufacturing it. They find that the ASME Code is very reliable, and they decide to use it.
But there are also possible technical abuses, which is one of the things I realized in my professional life. I have also been an inspector. Sometimes I found products where there is no real applicable standard, and they were using the ASME Code because they just do it. That was completely outside the field of pressure vessels and boilers.
For things like machinery, of course, it's better than nothing, but the background of every discussion in the committees is the safety of boilers and pressure vessels. And the need for machinery equipment is completely different. That's what I call a technical abuse, but the technical abuse is based on the reasons I mentioned before: history and easy access.
The final point is that I conducted a brief evaluation of the primary drivers for obtaining an ASME certificate and an ASME stamp in Italy. And here you see the answer, exporting capability and regulatory compliance in countries where it is mandatory.
The second reason is that it is the best tool to ensure that you can export your products.
And that comes back to the final answer to the question I raised earlier when talking about the fact that in Europe, you can use an ASME Code, but it is restricted. It's much easier for a manufacturer to use the same code for all the products regardless of where they are delivered.
In conclusion, I believe you should feel lucky because you are living in a country where the ASME Boiler and Pressure Vessel Code is mandatory.
Thank you so much.