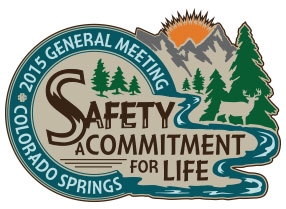
The 84th General Meeting Featured Presentation
Nathaniel Gee, P.E.
Hoover Dam: Maintaining a Giant
The following presentation was delivered at the 84th General Meeting Monday afternoon session, April 27. It has been edited for content and phrasing.
Introduction:
Nathaniel Gee is a professional civil engineer with the U.S. Bureau of Reclamation in Boulder City, Nevada. In this role he serves as project manager for dam safety and examination of existing structures programs. His responsibilities include performing rope access and dive inspections in some of the largest and oldest dams, including Roosevelt and Horse Mesa Dams on the Salt River in Arizona. Also, the Parker Dam spanning the Colorado River near Lake Havasu City, and the majestic Hoover Dam. Certified in ultrasonic testing, he also evaluates dam penstocks to ensure the continued safe and efficient operations of the facilities. Nathaniel received a bachelor's degree in civil engineering from Brigham Young University and a master's degree in civil engineering from the University of Nevada, Las Vegas.
Mr. Gee's slide presentation can be accessed here.
MR. GEE:
Thank you so much. I am honored to be here today to talk to you a little bit about what it is like to maintain such a large structure as Hoover Dam. I’ll begin by speaking a little bit about the Bureau of Reclamation. The Bureau of Reclamation manages water in the West. We cover 17 western states from the Mississippi out. I work for the lower Colorado region. We cover southern Nevada, most of Arizona, and parts of southern California
It took six companies, over 6,000 men, and five years to build the majestic Hoover Dam. When they finished, it was the tallest dam on Earth at the time. It impounded the largest man-made reservoir on Earth, and through its 17 generators, it is capable of generating four billion kilowatt hours of electricity in a year, enough energy for two million homes. It could pass enough water for farming 1.5 million acres of land. There’s no doubt that when the designers and planners looked at the job they had, it seemed insurmountable. In fact, I got a little bit of insight about the struggles of their day-to-day work lives when I first moved to Boulder City and purchased a little home that had been built during the building of the Hoover Dam. It was actually built by a worker named Jerry Lasada to house him and his mother. When we were renovating the attic upstairs I came across a letter in the insulation. I want to quote a little piece of that letter to you today:
Dearest, I was the most surprised man in the world when I got your letter. I have practically lived with that little snapshot that you gave me, remember? I quit alcohol like I said I would try, and I haven't had a drink for two days. That's the longest I have ever gone without it, and it sure is making me sick. And on top of that my mother is pretty sick, so I have got that on my mind. I tried to get off [work], but they won't let me. We are awfully shorthanded here on the job.
Unfortunately, that letter never got to his dearest. It was stamped "return to sender" and left in my attic. But it gave me insight into the day-to-day struggles that the workers had; the same struggles that we have, whether it's sick family members and trying to get time off, sobriety issues, and the like. But despite their day-to-day challenges, they built a wonder in the West -- truly an engineering masterpiece.
The challenge we have today is no less important. Many of us deal with maintaining America’s infrastructure. Hoover Dam is now over 75 years old. Much of the piping, gates, and valving is well beyond its original design life. And that leads to the question, how do we safely and reliably continue to maintain this great structure for the public today? The Bureau of Reclamation takes very seriously the importance of inspecting, maintaining, and doing analysis on these structures.
I want to talk particularly about some of the unique issues of Bureau of Reclamation's inspection program. The first thing is unique to the Bureau of Reclamation – the inaccessible feature of use. We all know the importance of seeing every aspect of those things that we inspect. For the Bureau of Reclamation, when it comes to the dam, it means getting to places that aren't easy to access. In order to do that, we have a team of highly-specialized engineers, biologists, and other scientists who are able to get to areas of the dam that are not accessible.
This first picture that I want to show you is actually a picture of me doing an inspection of Davis Dam looking at the distilling basin. We are able to get hands-on and up close in these areas. Not only do we have areas that are underwater, but we have areas that are difficult to access just by the sheer size of our properties.
This is another picture of me in the spillway at Hoover Dam looking at the concrete and deterioration. Also I had to test probe the drains to make sure we were living up to the pressure behind the spillway.
Every eight years we go through all our dams and inspect every aspect. Every item in the dam is inspected thoroughly in what we call CR (comprehensive review) inspection. Not only do we try to inspect the dam visually in all aspects, but we also look at discovering any changes to the seismology in the area (the seismic hazards with the dam). We look to see if there have been any advances in the hydrology in the area and any hydrology risks imposed to the dam.
As we do these inspections, we come into difficult maintenance situations and there are three in particular I’d like to share with you.
First, this slide is a cutback schematic of the Hoover Dam where you are able to see the internal workings. On each side of the dam there are two intake towers, one from the upper penstock and one that drops down from a lower penstock, and off those penstocks we feed the generator units, the combined pass of our dual propeller, our paradox gates, as well as our jet flow gates.
The intake tower is where I want to focus first. This is where we draw in water. The intake is over 360 feet tall. It has openings. This is our upper opening and lower opening. In order to isolate those openings, we have cylinder gates that actually slide over the whole thing. They look like a large cylinder that goes over the top. We are able to isolate that and close off water to the intake towers so that we can do maintenance on the penstocks as well as on the generator units. We take an outage on each penstock roughly every four to eight years so that we can close it off and do an internal inspection and perform maintenance.
Well, an interesting issue came up. Someone brought up the gates, which we look at regularly, but no one had looked closely at the cylinder gate stems that operate the gears due to the amount of grease build-up on the stems, as well as something we call quagga mussels. Everywhere below the line they have been covered by this invasive species, so we cannot actually see how the cylinder gate stem looked.
So we repelled down to these gate stems as you see here. This is a member of my crew looking at the gate stem, and these are what actually operate the cylinder gates. We began to remove some of the grease and chip away the quagga mussels, and, sure enough, there had been significant metal loss and significant pitting. And while we can measure the pitting on the outside, we do not know how much internally had occurred. There had been so much metal loss and damage that we couldn't get good measurements using ultrasonic techniques. It was clear that they no longer met the design intent. It seems easy enough to rip them out and replace them. But, of course, this is a very expensive job. They are over 360 feet tall. You can imagine what it would take to scaffold along that penstock intake tower. And to add to the complexity of the situation, all scaffolding and everything that you touch and bring in would have to enter through this little manhole. It's the only way into or out of the penstock.
As we started to look at costs, it was clear that we needed a better idea. Even though these no longer met their initial design, we had questions: did we still have factors of safety? Would these still safely operate if we needed to do an emergency shut-off of the penstocks? We are scheduled now to remove and replace three of them, and then we will continue to do destructive testing to test the limits of those to see what factors of safety we still have after their design life. That work will begin next year.
The next thing I want to talk about is another situation along the penstock. Many of you may be familiar with pipeline design. There is an incredible amount of thrust that occurs right where you turn down and go into the generators. Pipeline design nowadays use large thrust blocks, thrust joints, as well as what we call crotch collars or crotch plates to handle that thrust force.
At the time Hoover Dam was built, that was not how they did it. They used something called tie rods internally inside the pipe. Here is a picture of some men during the construction at the tie rods inside the penstock of Hoover Dam. Now, there has never been much concern about the tie rods. There have never been any visual signs that there was an issue with them. But in 2004, another dam that was built around the same timeframe as Hoover Dam, had two of the tie rods fail and their penstock failed. Suddenly there was huge concern regarding the tie rods at Hoover Dam. Managers began to ask a lot of questions: How are our tie rods different? Will they stand up? Do they stand the same risk? Would we lose our penstock if we lost our tie rods? And, there was the biggest question every manager has on his mind: is this going to fail before or after I retire?
So we began to look at them. First we took some instrumentation on the tie rods and began to look at what stress/strain they went through during normal operation and during analysis when we take out the penstocks and do draining and refilling. We wanted to understand the stress/strain that the tie rods went through, and the big thing we found was that the worst time was during the outage. Not surprisingly, when you drain the penstock and when you refill it, that's when we get the most thrust, and that's the riskiest situation. And so the people who were doing the modeling came to us and said they needed to know how many times since the late 1930s (when the dam was put into service) that we had taken out one of these penstocks.
Luckily for us, the operators at Hoover Dam have been very good about keeping records. As we looked through those old records, we knew exactly when they had taken an outage from the beginning of the dam and how many outages it had been through. So we were able to get that information to them. Then they did some finite element analysis of our penstock and tie rods to look at how we were doing, when they would fail, and when it would be a concern. If a crack began to propagate in the steel, how long would it take for that to continue, and when would we ultimately have failure? The good news is that at the end of the study we were able to tell the managers what we like to tell every manager: no, this is never going to be your problem, and in this case, it's likely not going to be your grandchildren's problem. Due to some design differences between Hoover Dam and the other dam where the penstock failure had occurred, there was no concern. The Hoover penstocks will last a long time.
As I went through this penstock/tie rods situation, it taught me a few lessons that I think are very applicable to your profession. The first is the importance of record-keeping. I was so grateful as I went through those operators' notes that they had been so meticulous in keeping records. I thought about it, and I bet many of them, as they wrote their notes, joked that no one would ever look at them, and indeed very rarely do we need to. But when we need to, it is important that we have them. And I'm sure many of you deal with that in your professions. The importance of keeping regular notes and documentation of maintenance is important.
The second thing I learned is the importance of passing on near failures. You come to meetings like this where you are able to hear of near failures or actual failures so that you can learn from them and go back and apply the information to the work you are involved in. I was grateful in my case that it was a Bureau of Reclamation facility that had the tie rod failure. But imagine if they had decided it would look bad if word of the failure got out and they tried not to discuss it internally or externally? We would not have known of the situation. We would not have known to look at the tie rods at Hoover. Ours ended up being safe, but it was important to go out and review them.
The last thing I learned was just how long some investigations can take. We found out about our tie rods in 2004. We finished the study in 2013. That's a long time. For us to get the outages that we needed to do the instrumentation, it took several years for the initial outage. It took us a while to figure out what data we needed to pull out. It also took some time to get it in our 10-year budgeting plan and to determine whether we needed more money to do the study. Things do not happen fast. It's important during inspections to notice potential problems very early because it takes time to correct them. We need to be very proactive in catching things early.
The next thing I want to talk about is the spillways. This is the spillway at Hoover Dam. This is the crest and it goes into this pipe. If we are not able to pass enough flow through our generators, these are used. And actually at the top of the spillway we have drum gates. They are gates that sit on hinges and they float up as the water rises so they can hold back additional water. We are able to fluctuate those drum gates. We flood them a little bit to pass more water. In this picture you can see one of those long drums and the hinge that it sits on. This opening allows water to flood into the chamber and floats this gate up into place so we can hold back additional water.
Inspections had noticed for quite some time that there had been a lot of deterioration of our drum gates. Of particular concern are hinge pins. In fact, it's believed that due to corrosion, those hinge pins will not work in the case of a flood; that these gates would not float up and hold back water as they should. So again it seemed like it's an easy enough situation. We know that maintenance needs to be performed, fix it, get them working again.
The first step would be testing the gate. Unfortunately, there is no water up against it, so we have no way of testing these gates. As you are aware, we are in the midst of a drought and the water is very, very low. Here is a picture that shows what we call the bathtub ring at Lake Mead, well over 100 feet below the drum gates, and we continue to have water shortages. And that leads to a difficult decision for management: do I spend millions, tens of millions of dollars to rehab these gates knowing that they may never be used again? On the other hand, no one wants to be the manager who decides not to rehab the gates, and then one day they do need to be used again, and we watch precious water flow over or worse, due to large flows, actually cause damage downstream.
Without these gates in place, we cannot hold back enough water to keep safe capacity downstream of the dam. So it becomes a very important issue for us to decide: do we rehab the gates? And when do we rehab the gates? To add to the complexity of the situation, access to the gates affects costs. Rehabbing them now when the water is down is significantly cheaper. If we wait until we are likely to need the gates or even get close to that, our access decreases and the cost of rehabbing them will go up. So it becomes a difficult situation.
In closing, I have talked about three different scenarios we’ve had at Hoover Dam. I talked a little bit about the cylinder gates, our tie rods, and the drum gates. I focused on probably the least complex parts of the dam because those are the ones I understand. Those of you involved in the power side, you know that the most complex parts: the piping, the generators, the turbines, all aspects I have not talked about, have their own maintenance concerns. In fact, even more so than the areas I have discussed.
Clearly, maintaining such a huge structure has many challenges. But I know that as I walk through the structure, I get a unique opportunity to see just about every piece of Hoover Dam. I get to walk through galleries that hardly anyone will ever walk through; galleries that most of the time are flooded and pumped out. And I think about guys like Jerry Lasada, guys who worked on the dam, and I am amazed about not only the functionality of the structure, but also the beauty of it. Those people really did build an amazing piece of history for us. But as much of a challenge they faced, I continue to draw back to the challenge that we have today: that in order for that Hoover Dam to remain the great edifice that it is, in order to deliver the water and the electricity that it does, it takes people who are willing to look at hard problems and decide how to safely continue to operate it; to solve challenges that were never initially designed when we looked at it.
And I hope each of you will do that in your own jobs: that you will take on those challenges and continue to make what great men and women made great. Thank you.
Question and Answer
Mr. Cantrell: What kind of concerns do you have for the concrete structures and stuff that have been exposed for so long? I mean, are there concerns?
Mr. Gee: It really depends on the concrete. With Hoover Dam we are really fortunate that the concrete mix they used was very robust and has weathered very, very well. The biggest concerns we have for some of our structures, particularly the Mason Dam and Parker Dam where we have a lot of alkali-silicate reaction, or ASR, and the concrete just continues to deteriorate over time due to that exposure. And that has a lot to do with what areas they were able to batch and where they got their mix from, how well it was washed and different things. So it depends on the structure. We do have structures where that is a significant concern, and we have some that we continue to core regularly and do testing to make sure that they are not deteriorating beyond a certain point. But I can't say that that's an issue at Hoover. Hoover has really, really good concrete.
Meeting Attendee: What kind of steel was used to make the tie rods? Was it low carbon?
Mr. Gee: I personally don't know. We rely heavily on our materials lab in Denver to look at the different metals. They are actually looking at an issue regarding how the penstocks are bolted down. A different material was used in the pins compared to the material used in the rest of the penstock, and the lab is looking at the different metals.