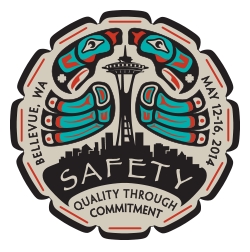
The 83rd General Meeting Feature Presentation
Douglas E. Smiley
“Biofuels - How Impacting the Greenhouse Effect Impacts Power Boilers”
The following presentation was delivered at the 83rd General Meeting Monday morning session, May 12, by Doug Smiley. It has been edited for content and phrasing.
One of the most discussed issues in the boiler and pressure vessel industry involves biofuels. Douglas E. Smiley is an expert on this topic. Mr. Smiley is a specialist in the area of jurisdictional inspections and machinery breakdown risk assessments. He is employed by Zurich Services Corporation as a senior risk engineering consultant. During his 33 years of loss prevention work in the insurance industry, Mr. Smiley has accumulated extensive consultative experience in the inspection and maintenance of production machinery and power generation equipment. Mr. Smiley has a B.S. in mechanical engineering from Northeastern University and a boiler inspector commission from the National Board which he received in 1982.
Mr. Smiley’s slide presentation can be accessed here.
Mr. Smiley:
In this presentation we will explore the use of biofuels in power boilers. This energy source is expected to grow over the next few decades and makes continuing research and development in the areas of boiler design and operation important. Those of us in the insurance industry need to keep abreast of developing technologies and share past lessons learned using this fuel.
We at Zurich believe biofuel is one of the green energy fuels that boiler inspectors should be familiar with. This is the third in a series of presentations dealing with green energy sources. We previously talked about solar power and biogas-fired boilers, and this presentation continues the theme, exploring the use of biomass as boiler fuel. Some categories of waste-derived biomass are considered carbon neutral and not adding to greenhouse gas emissions. The environmental impact and regulatory considerations of using manufactured biomass for boiler fuels are still evolving.
Let's cover some of the objectives. We will explore available domestic biomass sources, their supply distribution, and why companies are using it today, in quoting the current regulatory outlook, using biomass fuels from an environmental standpoint. Then we will spend some time talking about the challenges of using biomass as a fuel source for power boilers, and finally we will look at methods to help prevent some of the problems encountered when using biomass as a boiler fuel.
I have some personal experience in inspecting biomass boilers, and was surprised during my research to find that we have vast supplies of biomass fuel. Research efforts are ongoing on a number of fronts to develop biofuels in liquid form. However, these efforts are focused on applications to replace petroleum-derived fuels, such as gasoline, diesel, and jet fuel used for transportation needs. From a power generation standpoint, replacement biofuels could find applications for use in stationary combustion turbines.
Biofuels in solid form used for boiler fuel are characterized as biomass and is the subject we will explore today. Here is the current status of biomass power generation in the United States. The installed biomass capacity is about 16 gigawatts or about 1.4 percent of total installed generating capacity in North America. The United States added 549 megawatts of biomass-fired power plants in 2013, and some projections suggest by 2050 biomass could be used in over seven percent of the installed generating capacity across the globe.
[Slide 6] This is one of a number of biomass-fired generating facilities in California. We can see this biomass facility has a great deal of storage space for fuel since it was constructed in a rural area. Another observation I can make, that the fuel should be consumed on a first-in-first-out basis to control the age of the fuel piles. The decomposition of biomass can lead to odor generation and spontaneous combustion if not used for some weeks.
Current domestic biomass sources include: wood chips and pellets; various types of wood waste, such as bark, hog fuel, sawdust and wood clippings; residential and commercial construction scrap wood and demolition debris; agricultural wastes, such as straw, shells, husks and pits from harvesting and processing activities; animal processing byproducts; and trees removed due to insect damage.
Additional sources include: refuse-derived fuel, which contains, in part, organic material; and tire-derived fuel. (Using a gasification process outside the boiler, injecting the gas into the furnace or by shredding of worn tires fed into the boiler, tire-derived fuel is currently used to displace the use of coal). Waste sludge from paper mills and water treatment plants, which both contain organic material, are also regarded as biomass fuel. Their high moisture content prevents combination in the absence of other fuels. Reducing sludge moisture content to the 30 percent range is typically performed using filter presses or belt-drying systems. Black and red spent liquors which are burned in chemical recovery boilers in the pulp industry are counted as a biomass fuel. Their fuel value comes from hemicellulose and lignin dissolved from wood chips during the pulping process. And the last category is energy crops which are typically grown on land unsuitable for primary crop production. These include managed forest using short-rotation tree species including poplar, cottonwood, and tremuloides. Short rotation periods are considered to range from three to five years.
[Slide 9-10] Wood chips, the most common biomass fuel, have a high moisture content approaching 50 percent. Although recycling efforts have been made in many communities, I think we can all agree that we do not have a shortage of trash. With wood and other organic materials as part of the waste stream, this is another significant source of biomass fuel.
In addition to the existing short-rotation trees species mentioned, future source of energy crops are under development in the United States. These include dedicated cropland such as rapeseed and sunflower along with hybrid switchgrass; big bluestem; Miscanthus Giganteus, which is a perennial warm season Asian grass; and some sugarcane varieties.
Biomass boilers come in a variety of sizes, whether exclusively firing biomass or co-fired with coal. With an input of about 20 tons per hour to over 250 tons per hour, power boilers produce steam for heating, electrical power generation, and/or generation of process steam. The two most common technologies for biomass combustion are stoker grates and fluidized beds, with stoker technology far more prevalent in North America. Industries using these biomass boilers include pulp and paper and other forest products, as well as independent power producers. In recent years some utilities have begun converting their coal-fired boilers to partially or completely burned biomass.
[Slide 13] This chart shows the locations of larger biomass facilities in the United States. The green-colored states have at least one biomass plant. California has a significant share of these facilities, as we will find out later in the presentation. We can also see a few facilities in areas where agricultural waste would be expected to be plentiful.
[Slide 14] Here is an overview of forest-related biomass concentrations. The red areas have the greatest concentrations, then dark to light blue, and finally green to yellow. The same color coding will be represented in the maps that follow. In most cases, the larger biomass plants are located in the most densely forested areas.
[Slide 15] Now we turn to the largest concentrations of agricultural waste in the United States. We can see the Midwest has the largest concentrations. Iowa, Nebraska, Illinois, South Dakota, Minnesota, and Kansas are at the top of the list. These six states account for 64 percent of current supplies.
[Slides 16-17] Here is a better picture of agricultural waste concentrations. Again, the red color represents the highest concentrations. Let's take a closer look at this map again. It would seem that the use of agricultural waste as biomass fuel has growth potential due to the vast areas without any biomass-fed power plants.
[Slides 18-19] Here are some additional biomass sources consisting of primary mill residues. And our final source distribution slide of secondary mill wastes. So we see biomass resources are available throughout the United States, and there are significant growth opportunities for construction of biomass-fired power plants.
Why use biomass for fuel? Aside from saving valuable landfill space, biomass as boiler fuel provides an end use for waste products, assists in forest management hazard reduction programs by burning brush and tree thinnings, contributes to the local economy, and provides an alternative to fossil fuels. Last but certainly not least, biomass as a fuel is advantageous to use in the current and anticipated future regulatory climate.
[Slide 23-24] Here is a significant policy statement from the EPA which indicates they view the use of biomass fuels favorably. As we recall the concentration of larger biomass facilities in California, we again see a favorable climate in which to operate biomass facilities for power generation as far as state regulation is concerned.
Now let's turn to the use of biomass and issues encountered as a boiler fuel. I will start with the caveat: making generalization and engineering recommendations concerning the design of biomass combustion systems is made difficult by the variable physical properties of biomass. Biomass properties include moisture content ranging from 5 to 65 percent, with wood chips typically 40 to 50 percent, varying heating values, bulk densities, specific gravity, and thermal cone activity. These properties have only been determined for biomass constituents at ambient temperature. Determining the biomass properties in the combustion process during decomposition can be difficult in cases where the biomass mixture is not uniform.
Other factors, include the quality of wood fuels, varies more than coal quality, and some types of biomass used contains significant amounts of chlorine, sulfur, and potassium. These may result in heavy deposits on heat transfer surfaces, reduced heat transfer, and enhanced corrosion rates. Biomass fuels such as rice hulls have been discovered to act as an abrasive on boiler tube surfaces, a situation we would normally encounter with refuse-derived fuel. Boiler operators must pay close attention and periodically adjust feeders to maintain even fuel distribution as well as adjusting the ratio of over-fire to under-fire air.
Co-firing biomass with coal can cause severe slagging, fouling, and ash depositions depending on the type and percentage of biomass that is co-fired due to the interaction between the alkali in the wood and the sulfur in the coal. The effects of biomass co-firing in boilers designed exclusively to fire coal are still unknown due to the lack of long-term testing in this area. Transportation costs become an increasing component of the cost structure the further the biomass sources are from the facility.
Finally, future availability of low-priced biomass sources may be limited as businesses, municipalities and institutions pursue the use of biomass. This alternative source is being pursued to replace oil-fired process and heating equipment. The economics are particularly attractive where these facilities are located in areas not served by utilities delivering pipeline-supplied natural gas.
Now let us turn to methods to help reduce problems. During the design phase of the fuel feed system, selection of a proven fuel feed system is desirable. Dedicated feeder systems should be designed and installed for specific biomass sources or, where possible, blend all the fuels into a homogeneous mixture. This allows the boilers to fire at a consistent rate and maintain maximum load under all conditions which may avoid emission excursions which may violate environmental permits, excessively corroding heat transfer surfaces, and excessive slagging requiring more frequent shutdowns for cleaning.
Use care in designing the fuel handling system. For example, the ability to reverse drag chains on the dumper hoppers to make it easier to unplug fuel jams and adequate disk screens to reduce fine particle carryover. Boiler operators should use care when approaching the bottom of the pile in order not to add rocks or other debris to the incoming fuel stream. This debris can damage fuel-feed components such as augers.
Biomass from building demolition sources often contains waste material, and boilers using this fuel consequently have an increased risk of corrosion. Providing additional protection against corrosion can be accomplished by installing cladding on the lower sections of the boiler. As previously mentioned, fuel should be consumed on a first-in-first-out basis to control the age of the material which can lead to odor generation and spontaneous combustion. Operations personnel must be particularly sensitive to odors if the plant is located in an urban or residential area. A mitigating factor is the plant footprint is often limited in these areas, which also tends to limit the storage capacity. Adding a hammermill to the fuel processing system to allow the use of a broader range of biomass, this can reduce fuel costs by allowing a facility to process opportunity fuels such as railroad ties, brush, and tree prunings.
And finally, the point of installing boilers designed to optimally mix fuel gases. I would like to expand upon this topic particularly in the area of plant management. Biomass with abrasive biomass characteristics can cause accelerated wear on boiler tubes leading to premature failure. Ideally, plant management should establish a minimum allowable tube thickness prior to the scheduled inspection shutdown for each biomass boiler based on historical wear rates, boiler operating schedules, and the type of biomass fuel fired. Some management organizations which operate multiple refuse-derived fuel facilities have established on a corporate level a minimum tube thickness allowed for continuous in-use service until the next scheduled shutdown. If tubes are found during a scheduled shutdown under the predetermined thickness as measured by nondestructive examination, local management has no discretion on postponing tube replacement until the next scheduled shutdown. Obviously this practice can reduce the incidence of unscheduled shutdowns.
On this topic, the gasification of biomass used as a fuel for power boilers has been implemented for several facilities in the last decade. Future studies recently awarded involved the use of flue gas to dry wood chips, development of a solid boiler fuel that has potential for direct stand-in use at power generation facilities, and development of distributed generation in rural environments using rural biomass as fuel.