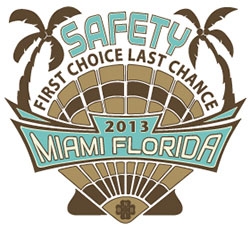
Biogas: The Hidden Costs of Going Green
By Robert "Buddy" Dobbins
The following presentation was delivered at the 82nd General Meeting on Monday, May 13, by Robert “Buddy” Dobbins. It has been edited for content and phrasing. To follow along with Mr. Dobbins’ slide presentation, click here.
Introduction:
Biogas is a topic of considerable interest to the boiler and pressure vessel industry. In his presentation, Biogas: The Hidden Costs of Going Green, Robert "Buddy" Dobbins of Zurich Services Corporation will provide an update on biogas and the real costs of going green.
Mr. Dobbins is a specialist in the area of machinery breakdown risk assessment. He is also technical director of machinery breakdown and team leader of Zurich's Global Technical Center. Possessing 25 years of loss prevention experience in the insurance industry, he has extensive consulting background in the fabrication, operation, inspection, and maintenance of machinery and equipment used for power generation. Mr. Dobbins is a commissioned boiler inspector holding A and B endorsements. He's also a sitting member of the National Board Inspection Code committee as well as the NFPA 85 committee.
Mr. Dobbins:
I am going to give you some information this afternoon that I hope you find useful. I want to take you back to a place -- some of you may not be inspecting very much these days. I know I'm not. I sit behind a desk a lot. I want you to use your imagination if you haven't been inspecting. If you are regularly inspecting boilers, then you should be able to do this with me. We are going to go and make an inspection.
Many of us have been there. It's late in the summer. It's hot. It's our first time to this particular facility. As we roll up on the job site, it's late in the day. Maybe we didn't pay much attention to the sign at the entrance because we know where it's at and we are just trying to get this one last inspection of the day finished so we can head home or to our office. We were told where to drive and how to get to the boiler house, and that there was no need to check in at the gate. They are expecting us. So we get there. We drive through, and we park at the boiler house. We grab our clipboard. We get our flashlight and we are getting ready to head to the trunk of the car so we can get our coveralls and our tools, and we are looking at the boiler house and the surroundings. We open the car door and we jump on out.
Oh, my, what is that smell? I know I'm not at a chicken plant today. It's not a processing plant. And I know it's not a pet food processor. But I look around and I see some gas lines coming across an open field. They are well protected, of course, and they go off into the distance a little ways. And then I see it. The sign that I missed coming in. It's down by the road next to the gatehouse. It says something like Smithtown Municipal Landfill, or maybe Smithtown Municipal Wastewater Treatment Center, or maybe even Farmer John's Biggest Hog Farm in the World.
We all know at least one of the hidden costs of going green. It's the cost to our sense of smell. I want to discuss a few of the less obvious costs of going green today. Some you might be well aware of and some of you might not.
Why are we considering the cost of biogas here today? In 2012, one of my colleagues, Tim Zoltowski, and the esteemed Chief of California Don Cook, spoke to you about a different type of green energy: solar energy. Today our society continues to search for ways to mitigate the effects of global warming while providing sufficient electricity to growing population centers, as well as markets emerging in Third World countries that are hungry for electric power. We heard about that earlier today. This makes the research and development of all types of green energy that much more important to the energy industry.
Those of us in the insurance industry are finding it increasingly more important to continue to research these so-called green industries. We need to stay in touch with advancements in the science and the engineering that makes these technologies more efficient while helping keep them safe to use. We at Zurich believe biogas and its potential effects is one of the green energy fuels that the boiler inspector, whether it's an insurance inspector, an owner/user inspector, or state inspector, should be familiar with.
I think it's important to talk about how we get biogas, the places we find it in use, and why companies are using it today. Then we need to discuss the components of biogas so we can understand why it does some of the things that it does. Then we will spend some time talking about the challenges of using the fuel. This is where we may find the hidden costs that I have alluded to in the presentation title. Finally, we will look at methods to help prevent some of the problems that biogas usage can bring about. That's also related to those hidden costs.
Biogas is one type of biofuel. It is a type of gas that is formed by the biological breakdown of organic matter in an oxygen-deficient environment. It's counted as a fuel that's friendly to the environment, which is why it’s considered “green.”
Biogas is composed primarily of methane and carbon dioxide. It can be employed for generating electricity or even as an automotive fuel, so it's very versatile. Biogas can also be used as a substitute for compressed natural gas, which is how we get to boilers. As I intimated in my introduction, I think many people immediately think of landfills when they think of biogas. There are various other sources of the fuel, however. Biogas can be obtained from sewage sludge, energy crops that are grown specifically to produce the gas, agricultural waste -- i.e., John's Hog Farm -- or even food waste. It's basically an output product from any of those various sources.
The resulting biogas is commonly used in its raw form as boiler fuel, but it can be upgraded by removal of all the gases except methane to produce a purified biomethane. What does the product do to the boiler? First, we need to look at the components of a typical biogas produced from a landfill or wastewater treatment facility. I think it's helpful to compare these components to those found in natural gas since we are familiar with its use.
In today's economy, 50 percent or more of biogas is actually burned off in flaring operations due to the high cost of its production exceeding the value of the end product. Let's look at some of the production costs. We find considerably more carbon dioxide in biogas than we will find in natural gas. The carbon dioxide can be stripped out, but it can also be used for other applications that make it valuable.
If we leave it in the biogas, we also know that it will lower our flame temperature, thereby reducing the nitrogen oxide, or NOx, formation by about 40 percent. So a decision of some type has to be made by the end user. We either modify the burner to handle a higher overall gas flow rate, or we install an additional burner for burning landfill gas only. That in the beginning is a potential hidden cost.
Also part of the picture is water vapor, or H2O. This is corrosive to the fuel piping. The moisture can be removed; not usually a problem in natural gas applications, but this is another hidden cost. Or we can replace the existing fuel train and certain burner internal parts with corrosion-resistant materials. Again, that's going to be another hidden cost.
Then we have gas contaminants, hydrogen sulfide, nitrogen, and other very small components of negligible amounts, none being of much consequence to this discussion. But we come to a component, siloxane, which is a ubiquitous white powder that appears in boilers that use landfill biogas. It is very important and we will talk about it at length.
There are some other challenges besides the makeup of the biogas when using this green energy producer. The user of this biogas has to consider the variability of the gas production flow rate. Gas flow from a landfill will be variable. There is really no way to control the rate of the breakdown of the materials in the landfill that leads to its formation.
These two charts are of the same readings, but it's an example of an actual flow rate from a landfill over a three-month period. It's in thousandths of cubic feet. It's a typical large landfill, and you can see how the flow rate varies over time. With biogas from a landfill or a wastewater treatment plant, there is going to be a need for some type of accumulater system or the need to supplement gas flow, because you can't run the boiler on this type of flow rate by itself. You are going to have to either supplement it with a supply of natural gas or use an accumulater system that you can pressurize it with. That is going to be another hidden cost if you hadn't thought about it.
Biogas is going to require conditioning. As we saw in its composition, there are contaminants that will need to be removed: moisture, hydrogen sulfide, et cetera. One widely-accepted practice to address both the flow variability and the removal of contaminants from the fuel is the installation of a collection and filtering system.
The collection stations in the landfill are piped to a central collection point by compressors and piping systems. The landfill gas is then treated at the collection station to remove the moisture and contaminants, and then transported by pipeline to its end use. It's a great way to kill two birds with one stone, but if you are not thinking about it ahead of time, it is another potentially hidden cost.
Now we come to what is probably the biggest problem found when using biogas. If any of you have inspected boilers from a landfill, supplied from a landfill, you have probably seen this at one time or another. Some might say it's not a problem at their particular installation, and it may not be. It can depend on the type of landfill waste that's being used. At other facilities, however, it is a big problem.
As the waste products in the various fuel sources begin to decompose, many chemical reactions occur. One of the reactions involves a chemical compound called siloxane. This is a class of organic or inorganic chemical compounds of silicones, oxygen, and usually carbon and hydrogen that are used in many consumer products and industrial processes, such as makeup, hairspray, and other personal care products.
These siloxanes turn up in wastewater and landfills to become a component of biogas from wastewater treatment centers as well. The particular compound tends to pass off as a vapor or what is called volatilize into the forming biogas as the waste product decomposes and the gases escape. It's part of the gas.
We next see the evidence of what they are called now as organosilicones or siloxane inside the boiler. There are actually various types of siloxanes composed of different types of compounds, and this is why I didn't try to memorize this. The types of compounds formed depend on the type of biogas in use. They can be made up of halogenated compounds, hydrogen sulfide, corrosive acids, or volatile silicone components.
Now, where we find problems in boilers with siloxanes are on the boiler tubes and tube sheets. Here we see a build-up of one of the compounds from one of our clients. It's in a water tube boiler across the outside of the thin water tubes. It's estimated in some installations that a boiler tube's life could be extended by 300 to 400 percent in those operations where siloxane is filtered prior to removal. Of course, we all know what a build-up of an insulating-type material on the tubes can do to boiler efficiency, so now we are using more fuel to obtain the required boiler output. And we also know what an overheating of the material can do in the long-term to that material.
Many times we will see the siloxane build up on the tube sheets of fire tube boilers from deposits made during normal firing operations. Now, we can clean this boiler up when we open it, and a lot of times it can be washed off. It appears to be a fine white powder that brushes off and washes away. So when I read this presentation to my wife, she said, “Well, what happens when they wash it away?” I said, “I don't know.” And I didn't at the time. But it's going to get reconstituted, especially if it's a wastewater situation. It would be reconstituted and revolitilized back into the system and you'd have to deal with it all over again. So it was a very good question.
But many times the powder or what is called filimentous type is generally composed of pure silica and silicone crystals. Another type of siloxane build-up can appear light gray in color and look like a thorn. That type of siloxane has a large carbon content. None of our inspectors have run across it yet or at least have sent me a picture of it or I would show it to you, but I have seen it, and maybe you have too. That type of siloxane is a needle-like siloxane which is the organosilicone. Then there is the needle type, and then there is the type of siloxanes that will not wash off. Those are the silicate-based scales that reduce the heat conduction and cause metal corrosion to the metal surfaces of the boiler.
The problems caused can vary depending upon where they turn up, but those can be quite severe, greatly reducing the economic benefits of using the biogas. The most obvious problem, as mentioned earlier, is the build-up of the layer of the silicone. When the siloxane produces microcrystalline silica, you have a residue with physical and chemical properties similar to glass. All of this leads to a significant decrease in the heat transfer capabilities across the surface of the tubes or the tube sheet on which the build-up occurs. That build-up naturally leads to a decrease in boiler efficiency and more and more fuel usage to obtain the required energy output, not to mention the effect of the build-up of the heat on the metal surfaces.
Not as evident but potentially as damaging is the corrosive nature of acids and halogenated compounds that may also be found in volatile silicone compounds. These compounds are not removed easily, and they will help lead to a layer that can cause serious deterioration of the metal to which they are attached, and they will do it in a short period of time.
There are methods by which the siloxane can be cleaned from the boiler surfaces after deposit, but these methods can actually cause additional damage to the boiler as well. Being able to wash the siloxane is obviously the most preferred method and the most hoped for method. Where we find the more stubborn types of siloxane compounds, however, the use may have to turn to more abrasive methods, or they even may turn to acid cleaning, depending on the severity of the scale build-up. Of course, that's obviously another potentially hidden cost in the use of biogas.
The most effective treatment programs for siloxanes are currently pretreatment methods of the biogas before it's actually burned in the boiler. These are called curative treatment methods. Heretofore adsorption of activated charcoal has been the preferred method for siloxane removal. Other adsorbents include molecular seeds or polymer beads. Another adsorption mechanism that has been used is nonvolatile organic solvents. It should be noted, though, that when an adsorption method is used, frequent replacement of the adsorption bed is required, sometimes on a weekly basis depending on the type and use of the system. That can be an expensive proposition and one of the largest hidden costs of using biogas.
Some of the adsorption beds can be reclaimed through a heating process. However, the most popular one, carbon, cannot, causing this type of adsorption treatment to bring about high disposal costs.
Cryogenic condensation or a refrigeration method is also another way to remove siloxane. By decreasing the temperature of the biogas prior to its use, the condensate is formed that contains part of the siloxanes that are present in the gas. It's easier to remove the siloxane from the condensate through filtering methods when that type of process is used.
One other method for siloxane removal is chemical abatement. Certain types of acids have been found to have the capability to dissolve the silicone-oxygen bond in the siloxane, taking away its adhesive properties. However, the high stability of the siloxane compounds require solutions with very high or very low pH values and/or high temperatures for this method to be effective. It's going to depend on the type of facility, the gas in use, and the resources available in selecting that method for siloxane removal.
In conclusion, I would first contend that the use of biogas has been shown to save money in installations that have properly planned to address the issues I have discussed. If those involved in the installation are looking ahead and thinking about this type of gas, the type of landfill they have, or wastewater treatment center they have, and they have a good engineer who understands what he's up against, they should be able to properly plan.
If it's a situation where there is an existing installation and they are planning on putting another burner in and using the gas that's next door, they could run into a problem later on if they don't have the right informed people involved.
Proper planning can make all the difference in a successful or failed operation if the following conditions are not at least considered when planning to use a biogas installation: removal of carbon dioxide to allow a hotter flame and more efficient boiler; removal of moisture from the biogas to prevent corrosion of the metal parts the gas comes in contact with; regulating the pressure of the gas formed in and drawn off of the landfills; cleaning of siloxane from the boiler surfaces; and prevention of siloxane build-up in boilers using adsorption systems.
There is an environmental cost in some facilities that is worse than others: odor – smells that some may actually call odor pollution. That condition can actually drop property values around the facility.
Regardless of the method used, it seems clear that it's difficult to use biogas in boilers without ill effects unless a proper abatement program or technique is also in use. These techniques are all an added expense. Adsorption still appears to be the most efficient and economically feasible siloxane-abatement technique today, but research continues on other adsorbents, as well as other abatement or prevention methods.
As our scientists, engineers, and inspectors continue to seek new ways to generate power for our growing population centers, it will continue to be one of our responsibilities to remain cognizant of new technologies and of the new and different types of previously unseen conditions that these technologies can bring about in the equipment and boilers we inspect.
We also must remain alert when older technologies like biogas are used in new ways and other unexpected conditions arise. Communication with one another and within our industry in these cases may not only save money for well-meaning companies, it could very well save lives.