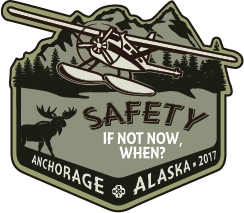
The 86th General Meeting Speaker Presentation
"Safer by Design: Building Intrinsic Safety into High-Pressure Steam Boiler Plants"
Michael Gerhart
The following presentation was delivered at the 86th General Meeting Monday General Session, May 8, 2017. It has been edited for content and phrasing.
INTRODUCTION: Michael Gerhart serves as sales manager, national corporate accounts, for Miura America Company, Limited in New England. Mr. Gerhart graduated from the United States Naval Nuclear Power Training Program, and went to serve as a mechanical operator and engineering laboratory technician aboard a Los Angeles class fast-attack submarine. Mr. Gerhart joined the boiler industry in 1999 as a manufacturer's representative. Over the past 18 years in this capacity, he has accumulated a range of pressure equipment experience with manufacturers, engineers, inspectors and contractors.
Mr. Gerhart's slide presentation can be accessed here.
MR. GERHART:
It's an honor to stand here and be able to speak to you today. I don't know about any of you, but I often get quizzical looks from people when I tell them what I do for a living. They can't imagine what people use steam for anymore. The general public doesn't really think about steam-driving machinery or any of the other uses that it served over the past hundred years. But as a matter of fact, steam is still a vital utility in today's world. It produces a lot of products around the world. And as the uses for steam have actually narrowed over the past hundred years, they have actually started to lean more towards the usage of high-pressure steam. So that's kind of the vein I want to talk to you about today.
High-pressure steam boiler safety is as relevant today as it has ever been. As locations around the world continue to industrialize, they look to long-established standards, such as those codified by this body, to ensure that the boilers they purchase and the standards by which they are constructed, operated, inspected and repaired offer them the highest levels of safety, and that means the lowest risk to the lives of their people and to their property. And we probably spend a lot of time in this group thinking about our local jurisdictions and the codes and how they affect our local lives, but I invite you to remember that the codes and regulations of this body are honored in over a hundred countries globally. And I would venture to say that it's these emerging industrial economies around the world, where there is little existing infrastructure in the way of experienced fabricators, inspectors and operators such as those gathered in the room today, that the codes and standards of this body are put to the strictest tests.
So as we consider the safety rules and how we consider boilers around the world, I invite you to remember that there are many people around the world who look to this body for their own safety standards. In jurisdictions throughout the U.S. and Canada, governing bodies are seeking to ensure they are enforcing the best standards and following the best practices to ensure the highest levels of safety for those entities operating under their governments. Many jurisdictions are enforcing laws and regulations written many, many decades ago, which they acknowledge on some level as being somewhat outdated and in need of revision. They, too, are looking to the members, often their fellow members of this group, to provide them with some standard or point of reference they can refer to on which they can base changes to their local regulations.
It's been clear in the industry for nearly a century now that generating steam, and especially steam at pressures of over 15 psi or roughly twice atmospheric pressure, is a uniquely dangerous business. A great deal of attention has been paid to making sure boilers are constructed and repaired with methods and materials that can handle the elevated temperatures and pressures they are designed to produce without catastrophic failure. A great deal of attention has also been given to protection against overpressure conditions, as well as other controls and safety devices to mitigate the safety risk posed by combustion. In fact, many of these same codes or similar codes have been applied across closely-related heating boiler and hot water heater product sectors, and thereby increasing their operational safety. Many jurisdictions, as well, require special operator licenses and define operator attendance policies for high-pressure steam boilers in their jurisdictional reach. Regular inspections serve to enforce these codes, laws and regulations.
While each of these considerations had a significant impact on improving the safe operation of high-pressure steam boilers, explosions and explosion-related deaths are still occurring today. While the existing codes and regulations unquestionably cover many critical aspects of safe boiler design, construction and operation, and even acknowledge by their very existence that high-pressure steam or power boilers pose a unique danger that must be addressed by additional layers of safety. In the end these measures are falling short in what they are attempting, to make what is essentially an inherently dangerous object safer. If our goal is to try to build intrinsic safety into our boiler plants, then we must acknowledge a huge source of energy within the boiler itself. And that is the most unique to their operation, the potentially explosive energy contained within them and the volume of pressurized water at saturation conditions. It's a loose analogy to be sure, but if we looked at a bomb and its shell thicknesses and at its ignition system, but we didn't take into effect the amount of explosive material contained inside that bomb, we would be doing it a disservice.
It is well known, and no doubt well understood by this group, that the unique properties of saturated water and steam, its enthalpy and its latent heat are what make steam such a useful source of thermal energy. It's also just these properties, however, which are the basis for the unique danger posed by high-pressure steam boilers. In order to generate steam, some amount of liquid water must, of course, be present. As the water is heated and converted to steam, the temperature and pressure of the two remain in close relation to each other under saturation conditions. As pressure rises, so does temperature rise, so does the temperature which steam formation will occur. Therefore, to produce saturated steam under 150 psi pressure conditions, the steam table tells us that enough heat energy must be added to raise the temperature to 366 degrees Fahrenheit. Since steam boilers are operated to a pressure set point, as more or less steam is needed, pressure fluctuations inside the boiler create more or less boiling, and the heat input is varied to maintain pressure. The unique danger of high-pressure steam boilers is what results should the pressure inside the boiler no longer be contained or allowed to equalize with atmospheric pressure. According to the laws of physics, a pressure change to one portion of a confined fluid is transmitted equally throughout that fluid. Therefore, if one portion of the pressurized volume inside a boiler is equalized to atmospheric pressure, the entire saturated water contents of the boiler would assume atmospheric pressure as well, almost instantaneously.
Since under atmospheric conditions, water boils at 212 degrees Fahrenheit, and the temperature of saturated water at 150 psi is 366 degrees, a portion of that liquid water will instantaneously, or in a flash, turn to steam. The specific portion of that water that will flash to steam is directly related to the temperature and pressure that existed prior to the pressure transient.
And what this chart is showing you here is that based on the operating pressure of a boiler, a certain percentage of that operating content will flash to steam. And as you can see, as that pressure increases around 15 psi, that percentage of flash steam is about four percent. As you reach towards 100 psi, that flash steam percentage reaches up to 15 percent. As you climb further and further up in pressure, getting close to 600 psi, almost 30 percent of that volume of water would immediately flash to steam.
Now, since steam occupies roughly sixteen hundred times the volume of water it was generated from, the force of this flash steam phase transition is quite substantial. In fact, in a technical article which could still be referenced on the National Board website published in the Winter 1996 edition of the BULLETIN, it described a portion of a flash steam explosion of a 30-gallon tank at 90 psi and at 332 degrees Fahrenheit saturation conditions are enough to propel a twenty-five hundred pound object, roughly the size of a car, about 125 feet into the air. That is a tremendous amount of force.
To reference a more recent occurrence in St. Louis just last month, it was enough force to propel a ten thousand pound boiler pressure vessel over five hundred feet through the air, crashing through the roof of a nearby commercial laundry facility and leaving three unfortunate souls without their lives. May they rest in peace.
With this in mind, then, it should be clear that the unique danger posed by a high-pressure steam boiler which distinguishes it from other types of boiler and pressure vessels is that of the potential energy contained within it under normal operating conditions. As we will discuss, however, the magnitude of this danger can vary greatly based upon boiler pressure vessel design independent of steaming capacity. Specifically, the magnitude of the risk can be quantified by two closely-related parameters. One, the operational volume of pressurized saturated water present and, number two, the operating pressure above ambient that the saturated volume is at. So to put this into perspective and to look at this in practical terms, if you have a large water mass operating at a very high pressure, it is less safe than a smaller water mass operating at a lower pressure. In fact, historically the industry has recognized this as the case.
Across the many styles and capacity ratings of boilers, as operating pressures and steaming capacities have increased, boiler models transition from high-water volume low operating pressure fire tubes to lower-volume higher operating pressure water tubes. I'm sure if you have gone into very many plants, you will notice this trend. However, there has emerged lately a disturbing trend whereby larger and larger water tubes, or fire tubes, are being produced, thereby overlapping with safer water tube designs. In fact, one prominent manufacturer out there today is producing a fire tube rated for 75,000 pounds per hour steaming capacity, which contains 7,500 gallons of water that could be pressurized all the way up to 250 psig. That is a tremendous amount of stored potential energy in that plant.
So what would it take then to make a high-pressure steam boiler inherently safe? That is, to reduce the operating risk level from that of a site-wide catastrophe to one of localized equipment failure? Operating pressure, one of the key risk factors outlined, is often dictated by the process or system being supplied. If a process could be performed that will lower temperature or pressure, it probably would be to conserve energy.
Water volume, on the other hand, provides a much wider range of design flexibility and can vary quite widely for rated steam output capacity. I have compared some different styles of boilers to show the differing water capacities inside each. Every one of these boilers is rated to produce 3,450 pounds per hour of steam, or roughly 100 horsepower. As you can see, the average per gallon for a 100-horsepower fire tube is somewhere around 600. For flexible water tubes, we are looking in the range of about 150, so less than a quarter of the fire tube.
And then we have another class of boilers called ultralow water volume water tubes, and those are averaging in the range of 45 to 53 gallons, so roughly around 49 gallons of water, less than one-tenth of the amount of water contained in a fire tube and less than one-third of that in the even safer flexible water tube designs.
Every one of the boiler designs above will produce 100 horsepower. They are all certified with an ASME S stamp, meet CSD-1 requirements, as well as other certifications within their jurisdictions. From a code standpoint and even many jurisdictional regulations, they are considered to be equal. By the laws of physics, however, their levels of operational safety could not be more different. In fact, the significant difference in operational safety was demonstrated to the TSSA of the Province of Ontario when a manufacturer who once, through a force-flow water tube steam generator, showed that even with all low-water level safety devices disconnected, the resultant failure was limited solely to the 500-horsepower boiler itself, imposed no threat of steam explosion to nearby personnel.
What would have posed with other boiler pressure designs a site-wide catastrophic risk of life and property, instead was limited to a localized equipment failure. The boiler simply melted down due to the inherently safe combination of water tube architecture, and especially the ultralow operational water content within that boiler. Five hundred horsepower, all the low-water safety devices completely disconnected on this boiler, it did not explode. It simply overheated, and eventually the burner was tripped off-line.
To be sure, there are design challenges and operational trade-offs which arise from such a massive reduction in operational water content. Clearly the obstacle as we search the volume to which to produce steam, water as the primary heat transfer fluid also serves to cool the pressure vessel. Maintaining the structural integrity of the materials of construction, the volume of water also impacts the time it takes for a pressure transient to occur as it dampens or buffers the heat input from the combustion system, impacting the amount of time required to match heat input to steam output. Therefore, reducing the volume of operational water content to a minimum then requires very efficient flow of flue gases and water throughout this boiler in order to maintain cooling and the amount of steam that needs to be produced and a matched shorter burner.
Amazingly, though, beyond this accompanying tightening of design tolerances, configurations for ultralow volume models can vary dramatically. As General Patton used to say, don't tell people how to do things, tell them what to do and let them surprise you with their results. So looking at a couple of different ultralow water content designs, those around 50 gallons for about a 100-horsepower rating, you can see that the burner configurations vary dramatically among these boilers. Some are down fired, you have one that's fired from the bottom up, and there’s one that even has a boiler that is fired horizontally into the boiler pressure vessel itself -- the same minimal water concept, completely different designs. One of these boilers has no refractory whatsoever. The boiler in the center has refractory top and bottom to protect the tube sheets. Other differences you could see in these boilers were multiple vertical water tubes versus a single coil. So there is quite a lot of variation between these designs, and there isn't one particular design or one particular way to achieve an outcome here. And I point this out just to say that the diversity demonstrates that designing for minimal water content does not necessarily mean that only one particular pressure vessel design can succeed or that only one or two manufacturers can meet the need. In fact, I would premise that there is more significant diversity of design amongst these ultralow water volume models than amongst most major boiler categories, and there is plenty of room in continual striving to improve these designs over time. As with any boiler design, there are always trade-offs as engineers seek to maximize one operational or maintenance attribute over another, or conversely minimize one operational or maintenance limitation.
Let's discuss some of the more prominent operational or maintenance trade-offs intrinsic to ultralow water volume designs. First, when you take all the water out of a boiler -- and I'm sure you have realized this when you are boiling water on your own stove -- if you have a smaller pot of water, it's certainly going to boil faster than a larger pot of water. Almost every one of these ultralow water volume boilers can go from a completely cold drained condition to producing its full rated capacity and pressure of steam in less than five minutes. It is a significant difference between what you probably see in a fire tube or flex tube for start-up time.
Water treatment. One of the things that I hear often in the industry about water treatment is that when you have an ultralow water content boiler, the water must be pristine, of a higher specification. And this is actually a myth that's out there. Water treatment across boilers is relatively the same. When you take the water out, just like the start-up time, what changes is the amount of time you have to react to poor water conditions. If you feed bad water into a fire tube, you will scale it up. If you feed bad water into a flex tube, you will scale it up. If you feed bad water into an ultralow water content boiler, it will scale up a little faster. So talking to the different chemical treatment companies around the nation, I often ask them the same question. What is the difference? Do you treat these boilers differently? And at the end of the day, practically speaking, for each boiler -- the chemical mixes are the same. There is an awareness that if out-of-spec chemistry occurs, it must be addressed sooner rather than later. Without that huge buffer of water, you have to react a little quicker to contaminants coming in.
Another thing as you remove that water mass, the burner inputs are much more direct into the boiler. Instead of there being a lag time between a burner input and steam capacity increase, the input is almost instantaneous. With no stored energy in the boiler, which is what we are trying to get away from, the reactions are very quick to system loads. Pressure builds and it dissipates very quickly.
Operational flexibility. With the ability to start up and shut down boilers, instead of having to run multiple boilers all at once, you can run only the ones you need. And, of course, footprint. When you reduce the amount of volume of water a pressure vessel holds, that pressure vessel shrinks in size. It is a significant difference when you talk about water content being one-tenth of the amount and a footprint of the boiler, the metal shrinking to roughly a third for the same rated capacity. But these trade-offs need to be thought of in the fashion of safety. If we are talking about improving boiler safety by reducing the amount of pressurized water content to a boiler, don't think of these trade-offs simply as operational decisions that need to be made. If somebody told you you could have a safer car but there was going to be some trade-off in operation, would you weigh that against the amount of trade-off you’d be willing to accept for higher-rated safety? And I want you to think about inherent localized failure versus potential for site-wide catastrophic damage and loss of life.
The other thing we talk about, because I mentioned earlier that we had to pay closer attention to flue gases flow and water flow inside of a boiler, because those tolerances are tighter, naturally out of the box, these ultralow water content boilers also happen to usually run at higher operational efficiency, somewhere in the mid-80 percent.
And, finally, fuel selection. When you tighten the tolerances for heat transfer inside a pressure vessel, you have to be a little more selective of what type of fuel you put into that boiler. You can't just burn anything. So a lot of biomass type fuels are out. You can't necessarily burn coal anymore. You can't burn other types of wood chips inside these boilers. You need to have a clean gas or liquid fuel, like No. 2 oil, that burns a little cleaner and does not soot up the heat transfer surfaces. So there are some limitations there with what you are able to burn.
The other issue is that you typically need to deliver a higher gas pressure in order to operate these boilers, because there needs to be enough gas volume under pressure to compensate for the quick changes in the burner that typically occur to meet the load in the system. So these attributes for which ultralow water volume boilers are purchased today, of course, continue to displace more traditional designs. It is this technology that is proving its viability more every year.
A few of the manufacturers of these ultralow water volume designs have been building and continuing to improve their boiler designs since the 1950s. This is not a new technology. In fact, some of these in Europe and Asia now command 60 percent of their home markets, and a leading product of the largest boiler manufacturer in the world is an ultralow water volume high-pressure steam boiler. Boiler selection is not simply a matter of operational preference. It is a matter of safety.
I have been pleased to talk to you today about the specific safety risk factors unique to high-pressure steam for power boiler operation and share with you some general information about these designs in a related technology of ultralow water volume, high-pressure steam boilers which minimize these risk factors. But if I stop there, this opportunity to address you today would be wasted. After all, the theme of this year's meeting is, Safety: If not now, when? If you agree with this premise, that the volume of pressurized water held within the boiler and operating pressure above ambient pressure are the main risk factors of safety, then you have to ask yourself how does that compare to our current codes, laws and regulations.
While I don't have time today to go jurisdiction by jurisdiction, several prominent trends emerge from a review of related laws and regulations around the country in the standards or benchmarks around which they are based. And what I found as I looked around at the differing jurisdictions is that generally they tend to differentiate among their operator licensing requirements based around steaming capacity. Whether it's Btu's per hour, kilowatt, horsepower, heating surface area, or safety relief valve capacity, these are all essentially measuring steaming capacity of the boiler. And as you can see from the previous slide that I showed you with the 100-horsepower designs, steaming capacity has very little to do with operating pressure or even water content of a boiler. It's virtually unrelated. Little, if any, consideration in most of the laws that I looked at was given to operating pressures greater than 15 psi. Most of the laws simply say anything over 15 psi is a high-pressure boiler, and it doesn't look at any of the other pressure ranges above that which are common in the marketplace. Little, if any, consistency exists between jurisdictions regarding requirements or the benchmarks that they base the different levels of licensing and attendance on.
And I talked to some of the chiefs in this room this weekend and around the country as I prepared this, and what I'm also finding is that if there was a scientific basis for those benchmarks, it seems to have been lost over the years, and we don't know even what these benchmarks are based upon in the first place.
I live in New England, and Massachusetts was one of the earliest leaders in crafting laws and regulations to improve operational boiler safety. They were one of the first in the country due to the industrialization going on in New England to enact boiler safety laws to try to protect lives and property. So I put forth this example based on our current laws in the commonwealth, and I compared two boiler plants for you. And really the only similarity these two boiler plants have to each other is water content. On the one side, we have a 200-horsepower fire tube boiler. It's got roughly 1,274 gallons of water in it, operating at about 150 psi. That's about six and a half gallons per horsepower. Operating requirements in the State of Massachusetts say because the boiler is less than 500 horsepower in the aggregate and it's operated at greater than 26 psi, from nine to about 250 psi, what's required to operate that boiler is a third class engineer's license and periodic attendance, which is the lowest level of attendance in the state.
On the other side, we have eight 300-horsepower ultralow water volume high-pressure steam boilers. At 135 gallons each operated at about 125 psi, that's about half a gallon per horsepower. About 1,072 cumulative total gallons compared to 1,274 in the 200-horsepower boiler. We are looking at 2,400 horsepower versus 200 horsepower. Because it's 2,400 horsepower, it's greater than 501, in the aggregate it requires a higher class engineer's license, the second highest, the second class engineer's, as well as continuous attendance while in operation. Even though it has lower water volume and that water volume is spread across eight boilers with eight separate burners, the requirements to operate that plant are quite a bit higher than to operate a single 200-horsepower boiler.
Massachusetts is not alone, though. There seems to be very little consistency across jurisdictions as to the levels of rated steaming capacity and associated licensing requirements. Even the Province of Ontario through the TSSA, which is one of the first jurisdictions in North America to acknowledge that operational pressurized water volume does have a correlation to operational safety, also has long had a limit of 75 gallons to earn that low water classification. Research into the 75 gallons, what's that 75 gallons based upon? It is because when they made the law, a 50-horsepower boiler, the average water volume was about 75 gallons, and a 50-horsepower boiler was deemed to be operator exempt in the province. So even though there is some acknowledgment there, it is even arbitrary.
Shouldn't safety benchmarks be based on science? If we acknowledge that water volume is actually an important safety factor in the pressure in which the boiler is operated, then somehow we need to adjust our laws inside the jurisdictions and update those laws to reflect the actual science of a boiler. Maybe we could look at things like saying gallons per boiler horsepower. Maybe less than a gallon per boiler horsepower would be considered to be ultralow water. I'm hoping to have a discussion with you about what the standards could be.
I look at other regulatory bodies, like the National Highway and Transportation Safety Agency and their codes on how to build a car. The headlights have to be a certain height, the hood has to be at a certain angle so that pedestrians aren’t harmed in a low-speed crash. Now they require you to have a back-up camera and other controls and safety devices on a car: Seatbelts, airbags, ABS. But at the end of the day, those cars are tested under worst-case conditions. They crash-test those cars. You can have all the specs you want on paper, but at the end of the day those crumple zones and safety devices will be tested.
As the boiler was tested by the TSSA and proved that it was inherently safe, even though a worst-case scenario for most boilers, low-water conditions, it did not explode, maybe there is some way this group can come up with a standard that could be used as a reference and maybe standardized across jurisdictions that would actually reflect real levels of boiler safety.
So in conclusion, operational saturated water volume and operating pressure are the primary safety factors uniquely associated with operating high-pressure steam boilers independent of steaming capacity. It's really what makes high-pressure steam boilers unique compared to water heaters or low pressure or heating boilers. Ultralow water volume, inherently-safe high-pressure steam boilers, which mitigate these risk factors, are a diverse and mature category of boilers with substantial North American and global presence. It's a feasible technology that is only being improved every day.
ASME and National Board members have tremendous influence over the safety standards of the boiler industry. People's lives and livelihoods depend on its membership to bridge the gap between the laws of nature and the laws of men. If the laws of nature and our law of safety do not match, the laws of nature always win. So I hope that we can have a discussion. I would love to hear your feedback on this idea and where we go from here. Any questions?
MR. BROCKMAN: Good presentation. There are inconsistencies. I would love to see uniformity. Less laws. What I would say is that the very same system that the TSSA tested is responsible for semi-close receivers that had to be there because of the steaming capacity, and that's what killed four people, not three, in St. Louis. So taking away the steam from the boiler itself doesn't necessarily reduce the –
MR. GERHART: Right. If you have pressurized water content, it doesn't matter where that pressurized water content is. It poses a danger.
MR. BROCKMAN: That's right. So we still have a system that has to be operated.
MR. GERHART: Right. Go ahead.
MR. MOONEY: What's the failure rate based on cold water or comparing the water to the other boiler? Do they fail at a greater rate?
MR. GERHART: I honestly don't even know how to quantify that. I mean, here is what I'm going to say about water treatment. There is a lot of bad water treatment out there. And the ultralow water content boiler is not the cause of the poor water treatment, but it will certainly bring it to light very quickly if it exists.
MR. MOONEY: Right.
MR. GERHART: But, again, I would ask you, safety, site-wide catastrophic risk versus isolated equipment failure? Trade-off, you have to take better care of the water. Is that a legitimate enough trade-off to offset the massive increase in operational safety to people and to property that results?
MR. MOONEY: You mention safety, but there is the loss of property as well. So if you are losing the boiler every eighteen months where I can have a larger boiler that holds more water but is able to last ten years and I have a guy who can be a less licensed person operating it, I'm spending less money there, so there is a balance.
MR. GERHART: If that was the case everywhere, then I would agree with you. But this style of boiler has 60 percent market share in Europe and in Asia, and it's gaining greater and greater market share here in the U.S. And our rate of failure at least for my company is fairly low on this front. I have operated in New England now for nearly twenty years, and out of that twenty years, of all the pressure vessels that I have been involved with, I have lost one that we had to replace, and that was because rock salt was being put into the brine tank rather than softener salt, which made a huge difference.
MR. CANTRELL: When you speak of uniformity, is your first choice in operator qualification requirements, like the power engineer that has to run the boiler, or is it in inspection criteria?
MR. GERHART: Well, steam systems inherently require maintenance; there is no question about that. It's not like a hot water boiler where it's an open loop system. You need operators. And what I would say to the operators as well is, wouldn't it be better for you, wouldn't your wife and children be happier to know that you are not the last line of defense for safety on a boiler? That you are actually there to maximize the performance of that piece of equipment; that your life isn't on the line every day when you walk into your plant if something goes really wrong? And the other thing I would say is our operator laws today, again, I'm looking for uniformity, something scientific-based. So if we look at 15 psi boilers, most of the boilers produced today are produced to about 150 psi spec, and then to about a 300 psi spec, and then above that you are typically getting into power generation, co-generation, something where the plant is much more sophisticated anyway because you have all this electrical equipment, so you tend to have higher qualified people running those plants, making them safer. Somehow I think that as we look at operator requirements, water volume should be a definite consideration when we are looking at the real risk of this piece of equipment. A lower water volume boiler is inherently safer than a large water volume boiler. Now, the operating pressure also plays a part in that. The amount of flash steam, the size of the explosion is going to vary based on pressure. So if we say 15 psi, those right now are exempt. Maybe the next classification should be 150 psi design, and maybe the next classification should be a little higher. I'm posing this to you guys to say let's look at the real operating environment that our customers are operating in.
MR. CANTRELL: I guess the reason I'm asking is in the State of Nebraska, we don't have an operator requirement.
MR. GERHART: Okay.
MR. CANTRELL: So you are looking for uniformity. The National Board Inspection Code, which we adopt, doesn't have operator training requirements. National Association of Power Engineers does not have that.
MR. GERHART: Right. So it's my understanding that ASME and the National Board can set standards. They can say this is what we believe the standard to be out there. Now, whether the local jurisdiction adopts that standard or not is up to them. And the State of Nebraska could say we are perfectly fine the way we are and we don't want to adopt -- we recognize this standard and its value scientifically, but we are not going to recognize it from an operator licensing standpoint. And I doubt that the National Board or ASME would say operator licensing needs to be X, Y, Z from state to state. But what I am looking for is some point of reference on which to base those type of laws so that they are not completely arbitrary, 200 horsepower here, 50 horsepower there, 300 horsepower over here.
MR. TROUTT: So what would you like to see us put this in? The NBIC?
MR. GERHART: I don't know. You guys are the experts on this.
MR. TROUTT: We have some problems here. So just like Chris, I don't have an operator's license. Don't get me wrong, I wish I did, I truly do.
MR. GERHART: Okay.
MR. TROUTT: But in just about every jurisdiction that doesn't have an operator's license, it's because we don't have a law for it. And if we don't have a law, that means you have to have a law change. And in today's day and age, getting a law change to form more regulation is next to impossible.
MR. GERHART: Is CSD-1 a law that your jurisdiction has to accept?
MR. CANTRELL: No.
MR. GERHART: It's a code; right? Now, you may choose to accept it as your local jurisdiction or you may not; right?
MR. TROUTT: Right.
MR. GERHART: That's the type of standard I'm saying to put forth. I am identifying a gap between the laws of physics and the laws that we see across the country for boiler safety. Somehow we need to close that gap. How we do that I don't know. This is my first time at a National Board meeting.
MR. STENROSE: Michigan sees enforcement of CSD-1 as the alternative to requiring a licensed operator. There are one or two cities in the state that require licensed operators, and certainly utilities all have their own programs for doing it. We look at the CSD-1 as reinforcement instead of trying to get a legislature to increase regulation.
MR. GERHART: In many cases if we went by water content and operating pressure, the amount of regulation would decrease, because the market would say this is deemed to be a safer design. If the insurance companies say this is a safer design, they write their insurance policies accordingly. If the National Board and ASME say this is a safer design, the regulations will be written accordingly. When you look at cars that have crumple zones, and they have safety devices on them and back-up cameras, those cars sell much better, because the perception of safety is what consumers care about. If I'm building a factory in Brazil -- and, again, think globally about this -- if you are a big brewery and you want to build a new factory in Venezuela and you don't know what kind of inspections there are locally or what codes are enforced there, you are going to say there are no trained operators. I want to buy the safest design that I can buy, so I am going to buy an inherently safe boiler. Because I know that even if those operators completely screw it up, it will melt down. And it will cost me something and maybe I will lose some product in the meantime if you don't put redundancy in it, but nobody is going to die and my factory will still be standing tomorrow.
Any other questions? I know I am challenging you. I know I am challenging very, very old laws and very old ways of looking at things. And I appreciate this opportunity to have this conversation with all of you, and I hope it does continue.
Thank you very much for having me today.