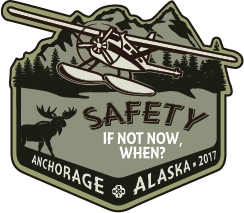
The 86th General Meeting Speaker Presentation
"Historic Introduction of Plate Heat Exchanger Rules into ASME and National Board Codes"
Michael Pischke
The following presentation was delivered at the 86th General Meeting Monday General Session, May 8, 2017. It has been edited for content and phrasing.
INTRODUCTION: Mike Pischke began his career 38 years ago as a pressure vessel welder. Ten years into the profession he earned a Bachelor of Science in Metallurgical Engineering and later a Master's degree in Materials Science. For the past 21 years he has worked in quality management positions for Alfa Laval and GE Power. In those positions he has been responsible for quality and welding programs in compliance with ASME Codes Sections 1, 8, 9; and NBIC codes. Mr. Pischke currently serves on ASME Section 8, 9, and QAI-1 Standards Committees, as well as the Tennessee Board of Boiler Rules. He chaired the Task Group on Plate Heat Exchangers, and is the technical project manager for the incorporation of the Mandatory Appendix on Plate Heat Exchangers in Section 8 Division 1.
Mr. Pischke's slide presentation can be accessed here.
MR. PISCHKE: Thank you very much. It's an honor to be here today on behalf of the Task Group on Plate Heat Exchangers. I hope I represent them in this presentation. Today we are going to talk about this historic introduction to plate heat exchanger rules into ASME and soon National Board codes. Our topics are going to be the plate heat exchangers themselves, the components and operating principles; the history of the PHE technology throughout the years; various designs that are incorporated in this appendix; applications, typical applications where you inspectors will see these in the field or have seen these in the field; and elements of ASME Section 8 Appendix 45.
First, we are going to talk about the components and the operating principles of the plate heat exchanger, the main components, which are the heat transfer plate pack, the fixed and movable end plates, the connections, and the tie bolts. The operating principle is very simple. You take one fluid and you heat it up with a hotter fluid, and vice-versa, the hot fluid going in one side and the cold fluid going in the opposite direction. In the single-pass arrangement to the left, which is the most common, it's exactly that, it's just a single pass. [Slide 6] There are no multiple passes through the heat exchanger.
In the multi-pass arrangement, you get counter-flow in various directions. And these designs can handle up to eight connections. In fact, even more if you add inner-connection plates in the plate pack. These allow the heat exchangers to work with various fluids. For example, on a ship, it could use seawater to cool various fluids, including lube oil, engine coolant, various hot and cold fluids all at the same time. So that's one of the advantages of the multi-pass arrangement.
Heat transfer plates themselves are where the heat transfer takes place. They have two types of plates. One is a low theta, which has a high angle and slows the fluid down a little bit. And then there is a high theta, which has a low angle and slows it down more. A combination of these heat exchanger plates can be used to customize the flow and heat transfer within the plate heat exchanger. And that's one of the elements of these heat exchangers that manufacturers and users like about them. You can customize them by changing the low and high theta plates to customize the flow in the heat transfer. This is a graphical example of the flow rate. [Slide 8] If you use just low theta plates together, you get low turbulence and a low pressure drop. Medium, which is a combination of a low and high theta, gives you medium turbulence and pressure drop. And then, of course, two high theta plates will give you high turbulence and high pressure drop.
Now we are going to cover the history of the plate heat exchanger technology. The first plate heat exchanger was developed in approximately 1923. There is some discussion about the exact date of the first plate heat exchanger, but these were designed and used for pasteurization of milk. That was the first use. The heat transfer plates in these were machined-out thick plates that they used for heat transfer, and some of the first plates had what they call a chocolate design, which the grooves were square. It was just a series of square channels. Somewhere around 1960 they came up with the herringbone design, which we looked at earlier, and then as these progressed they developed the brazed-plate heat exchanger in the mid '70s, semi-welded in the '80s, fully-welded in the '90s, and then finally fusion-brazed heat exchangers in the early 2000s. We are going to cover some of the various designs. There are so many designs out there, but these are the most popular and the ones that we tried to address with the appendix, the mandatory rules. The basic PHE design categories are gasketed, semi-welded, fully-welded, block type, and, of course, brazed.
Now, here are the approximate pressure and temperature limitations of each one of these.[Slide 13] As you can see, the gasketed have the narrowest pressure and temperature ratings. The brazed, believe it or not, has the largest, due to the variation in braze material that can be used in this application. So for the gasketed and semi-welded PHE designs, the gasketed heat transfer plates are very similar. In all gasketed, as you can see, there is a gasket between each heat transfer plate, and the only thing that seals these from leaking is the gaskets on the heat transfer plates.[Slide 15] On semi-welded it's very similar, with the exception that two plates are laser-welded together to create what's called the cassette. Oftentimes these cassettes are used to handle fluids that can permeate gaskets. One example is refrigerants. Semi-welded are usually used in refrigeration applications because it won't allow permeation through the gaskets. Characteristics of gasketed and semi-welded design: They are modular. They are expandable and contractible. You can adjust them for how much heat transfer is required. You can easily replace parts in them. You can also use nonmetallic heat transfer plates, which we will look at some of the designs that use those. And they may be disassembled for installation. Through the years I have seen several applications where the heat exchanger had to be disassembled and put into a cargo elevator in order for it to be reassembled in the location, like in the basement of a nuclear plant or on a ship.
The next is the fully-welded heat transfer plate designs. In this case, all of the heat transfer plates are welded together using a laser lap joint weld. This is a more difficult design to produce because you basically have to keep welding one after another on itself, and you end up with a plate pack module that is more or less fixed in size.
A variation of the all-welded is the block type heat exchanger as well. This is similar in design but not quite the same. In this design, as you see, the fluid flow comes in at a 90-degree angle instead of all from one end or the other, but it's used in high-viscosity fluid applications. [Slide 21]
Characteristics of the fully-welded: Higher temperature and pressures than the gasketed because it's not limited by the decomposition of gaskets. You don't have to replace any gaskets. That's another advantage. It avoids the gasket fluid permeation, as I mentioned earlier. And one of the downfalls is that it is much more difficult to alter or repair once they are in the field. Not impossible, but they are more difficult.
Next is the brazed-plate heat exchangers. These are typically smaller in size. This is a cutaway view of them and how they are assembled with the herringbone heat transfer plate alternating with brazed material. [Slide 25] In this case, it's copper. One of the most common is stainless steel with copper, but they make various materials. The most robust one is actually stainless material with stainless brazed material, which is fusion brazing. There is a cutaway view of the copper. That's the heat transfer surfaces. As you can see, there is a lot of area for heat transfer in these. Most of them are very compact. They can range in size from one you can hold in your hand up to about the size of a small refrigerator. They have the largest range of temperature and pressure. They have a very robust design. I have pressurized some of these up to five thousand psi before they actually rupture, so they are very robust. But they must be cleaned in place. You can't disassemble them. And they are one and done. Once they go bad or leak, they are disposable.
Now that we have covered the basic types, I wanted to talk about some of the applications. What's listed up here is just some of the primary applications that you find these in. [Slide 27] If you are an inspector in the field, I'm sure you have all seen these. Oftentimes you probably use them to rest your clipboard while you are inspecting a circular vessel, but here are some in the chemical and petrochemical and, on the far right, a liquid natural gas application. [Slide 28] As I mentioned earlier about the nonmetallic heat transfer plates, these are using graphite heat transfer plates for strong acid applications. You will notice on the heat exchanger on the left, the timing bolts have springs on them, and that's to avoid cracking the graphite heat transfer plates, which are not obviously as malleable or flexible as the metallic heat transfer plates. [Slide 29] Here are a couple brazed units and then a gasketed unit in HVAC applications. [Slide 30] Highrises use them a lot at various levels throughout the building for their HVAC systems because you can tear them down and take them up and down an elevator. Because they are compact in size, they are often used on ships. Here are a couple maritime applications. [Slide 31] As I mentioned before, if you have a multipass unit, you can use it to heat and cool various fluids throughout the ship.
Here are a couple power generation applications. [Slide 32] One is an economizer, and the other is a lube oil cooler for a gas turbine. That's a very popular application for it.
Ethanol production uses distillation and evaporation condensing quite a bit. [Slide 33] Also there are other fluid applications that use these types of heat exchangers. Another application where it kind of just ended up filling in for other types of heat exchangers is in ultrapure water, primarily for production of semiconductors. [Slide 34] Hot, ultrapure water is used in the production of semiconductors.
Sanitary and brewery. The one on the left is for the production of yogurt. [Slide 35] We see these a lot in all types of sanitary food applications, dairy, and peanut butter. They use that production. If you go into a mini-brewery, you will see a heat exchanger like that one on the right in the production of beer, which is very important.
Next we are going to talk about the elements of the mandatory plate heat exchanger appendix. This took six years to develop. It was not easy, but we got all of the important people together, including the jurisdictions, the design engineers, the plate heat exchanger manufacturers, the users, and the authorized inspection agencies. The key elements that we have to determine, and the first one was the toughest - definitions and terminology. We all had to get on the same page with what we called these components. That took the longest time.
The next was the design application. We had to discuss how everybody was doing the design. It was apparent right off the bat that the primary method of design was using Section 8, U-2 (g), and variations of UG-34. But we couldn't use UG-34 itself because it is intended for symmetric design, and plate heat exchangers are almost always asymmetric design. So we had to use U-2 (g) for most design applications.
The next was materials - what kind of materials are applicable for this - especially for heat transfer design. And one of the things to remember about the heat transfer plates is the materials that work best for heat transfer are not necessarily the strongest materials. They are the most conductive materials, not necessarily the strongest. And so in a plate heat exchanger design, heat transfer plates are constrained by the stronger materials.
How we pressure test was another issue that we had to address. And then documentation. The plate heat exchanger does not work well describing it on a standard U-1 or U-3 data report. And back to this picture, the definitions and terminology. Many of these components are not pressure-containing components, but rather the components of the heat exchanger used to assemble and disassemble it. [Slide 38] So we had to explain all of them, but we had to focus on the pressure-retaining components for the rules.
As far as the design, the fixed and movable end plates, as I mentioned, are designed to U-2 (g) currently. We would like to move forward as a task group to come up with more specific design rules, and I think we are moving in that direction. We kind of have to wait for the U-2 (g) committee to come up with some guidelines for us, but that's where we want to move. The gasketed plate packs, for design purposes, only have to handle 1.3 times MAWP. They do not have to go through a full UG-101 proof test. Fully-welded does have to go through a UG-101 proof test. Brazed, same with that. And then all other pressure parts that are common to Section 8 Division 1 are designed. An example are the nozzles, those would be designed in accordance with Division 1.
The materials. End plates and bolts, like any other ASME vessel, the material must either meet Section 2 or a specific code case. Heat transfer plates may also be used using a special limited code case that would limit that material to heat transfer plates only. In other words, nobody can use it for a vessel itself, just the heat transfer plate. And that's what we were after, because as I mentioned earlier, some of the best heat transfer plates are not the best materials to design your entire vessel out of. Nozzles and fittings are Section 2 for the most part. It's possible to code case it. Nozzle liners are exempt. In a plate heat exchanger, the liners themselves are not considered in the strength calculations. They are just liners. Oftentimes they are made out of things like rubber. Some of the liners are combination gaskets and liners, so they are nonmetallic.
Pressure testing. The pressure testing is in accordance with either UG-99 or UG-100 pneumatic, and, like any other vessel, they must be tested to 1.3 times MAWP for hydro and 1.1 for pneumatic. Now, here is the catch. The internal heat transfer plates in accordance with UG-99 or UG-100 must be tested at least at MAWP. This is important for plate heat exchangers, and we will try to go through an example and I will explain why. If you pressurize one chamber at maximum test pressure, in order to pass that with a gasket heat exchanger, sometimes you have to compress it to a point where you damage the plates, the heat transfer plates. You will pass the test, but you will damage the plates. What you want is it to pass the double-sided 1.3 times MAWP and MAWP between chambers. And so what I have here is an example of how these are often tested. [Slide 42]
Now, this doesn't apply for all designs, and there are some designs that you can pressurize at two times MAWP on one side and they will never leak, but some of the larger designs we have to test this way. And that would be by bringing it up to test pressure on both chambers, and then dropping one chamber by MAWP down to test minus MAWP, and then doing the same for the second chamber. And this methodology or this procedure meets the letter of the law of UG-99 and UG-100, and it also tests the heat exchanger for top-rated conditions. One of the benefits of doing the cold water hydro is that that's probably the worst condition that some of these heat exchangers are going to be in. Once they are in service, many of them aren't using water; they are using other fluids and at higher temperatures, and so they tend to seal better than they do with water.
Finally, the documentation. The task group has developed two forms specific for plate heat exchangers, the U-1 (p) and U-3 (p). When we first started, I was hoping both documents could be one-page documents, but unfortunately they are both two pages.
That was one of the deliverables of this task group. Moving forward, the task group will continually revise these rules as the technology grows and we will continually address the industry requirements.
I would like to thank you for allowing me to speak here in Anchorage. I very much appreciate the opportunity. Thank you.