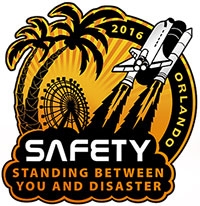
The 85th General Meeting Feature Presentation
Mark Masters, P.E.
What's Under Your Hood?
The following presentation was delivered at the 85th General Meeting Monday afternoon session, May 9. It has been edited for content and phrasing.
Introduction:
Mark Masters is the director of code services for the HSB Latin America Division. He has over 20 years of extensive experience in the pressure equipment industry, with most of it focused on Latin America. Mr. Masters began his career as a boiler machinery inspector, and also filled roles of authorized commissioned inspector, project manager, business development manager, and product marketing manager. Mr. Masters is in charge of HSB's Latin America Region, with commercial and technical responsibility for the company's services in Mexico, the Caribbean, Central America, and South America. Fluent in English, Spanish and Portuguese, Mr. Masters holds a bachelor of science in mechanical engineering from California State University-Sacramento, and an MBA from the University of Phoenix. Additionally, he is a registered professional engineer and is commissioned by the National Board. He is also a loss control specialist, an equipment reliability specialist, a project manager, and a manager of ISO registrar business. He is also manager of a technical inspection services group supporting manufacturers and owner/users in complying with international standards, including the ASME code.
Mr. Masters' slide presentation can be accessed here.
Mr. Masters:
Good afternoon. The topic that I'm going to address today is actually a presentation that we have designed for buyers of pressure equipment, as well as regulators, outside the United States, and focused especially on South America and Mexico. In addition to reproducing the slides and information that was presented to that audience, I also added information to put it in context, and then finally, described some steps forward as the ASME Boiler and Pressure Vessel Code (ASME code) and the National Board Inspection Code (NBIC) are potentially adopted by countries in that area of the world.
To put things into context, in the summer 2012 issue of the National Board BULLETIN, I wrote an article called “To Stamp or not to Stamp,” which was intended to help educate the marketplace, particularly in Latin America, about the differences between formally certified and stamped ASME equipment and compliant ASME equipment, which could be who knows what. After the article was published, we found an increased level of awareness on the part of many manufacturers, but the message still didn't really reach the buyer.
Similar to what Scott Lynch discussed in his presentation about the challenges ABMA faces, there are similar challenges regarding how users specify the use of the ASME code (or not) in the pressure relief arena. To describe the market environment in Latin America specifically, about 10 percent of equipment built in accordance with the ASME code is actually certified or stamped. There has been some market research, most recently in Argentina. The organization, the quasi-governmental entity there responsible for adopting standards for use in that country, went out and actually surveyed all of the installed pressure equipment in the country, and what they determined was that about two percent of all the installed equipment was actually certified as having met the ASME code.
I have yet to run into a single instance in Argentina where a code other than ASME was used or specified for fabrication. That's the low end of the spectrum. We get the 10 percent number by simply looking at the volume of vessels produced by those shops we support as an authorized inspection agency, and determine the percentage of those vessels that are actually certified by ASME, about 10 percent. In Mexico, the percentages are a little bit higher. In places like Brazil, the numbers are significantly lower.
There is little to no control over repairs or alterations of pressure equipment. The NBIC and the role of the National Board are not understood at all, although that's changing. I have been to several presentations with Chuck Withers (National Board assistant executive director – technical), and others who have helped try to expand awareness of how the National Board Inspection Code is intended to be used. One of the misconceptions we see is that most folks who understand the National Board Inspection Code are under the misconception that it can only be used if it's been certified by the ASME code of construction, which obviously is not true. So we are trying to help improve the understanding.
In terms of what drives the use of the codes, there is no country in Latin America that mandates the use of any code or standard for new pressure equipment or for repairs or alterations of pressure equipment. The closest to that is in Brazil. Brazil has a standard called NR-13. It's similar in some ways with the pressure equipment directive, but NR-13 allows you to use any internationally-recognized standard to fabricate or construct pressure equipment. But when it comes to actually certifying that standard, it’s not required. So in Brazil, for example, if ASME is used as the code of construction -- and that's how you document your compliance with the NR-13 law -- a Brazilian registered engineer has to evaluate the design, and hence the requirements of construction code and ASME, has certified that your design does or does not meet that standard. But there is no requirement for qualifying that Brazilian registered engineer. He's got to be a B.R.E., but he may have no understanding of what the ASME rules are or may not maintain current understanding. And when it comes to the actual installation and verification, there is no requirement for the qualification of the inspector. So there are some serious gaps.
What’s also interesting to know is that if you decide to use the ASME code as your construction code to meet the NR-13 requirements, one of the requirements of NR-13 is that you have a nameplate indicating what code or standard is used for construction. So you have vessels that have an ASME edition identified on the nameplate as being the code of construction, when the equipment is not actually certified to ASME, so that raises some interesting questions.
In terms of who builds and repairs equipment, in Latin America there is a lot of importation equipment, obviously, but the number of certificate holders is increasing quite dramatically. I have been involved with ASME and Latin America -- at least with the ASME market -- for about 10 years, and in that period of time the number of certificate holders has doubled at least, but we are still talking about a very small number of certificate holders. In total you have somewhere in the neighborhood of 350 certificate holders for all of Latin America, Mexico south; and of those, about 175 of them are in Mexico. And the obvious driver is that the Mexican industry also exports to the United States, where ASME code is required.
So how is compliance verified? Well, it may or may not be verified, and we are going to spend most of the balance of the presentation -- which again is geared toward the buyer of pressure equipment or the regulators -- to discuss how to verify compliance with the ASME code.
I started working in Latin America about 20 years ago. I was working outside the area of pressure equipment compliance, but in the area of equipment reliability, and there is a good understanding on the part of engineers in Latin America about the ASME code and the benefits of spec'ing equipment as being compliant with ASME.
When it comes to the actual purchasing function, which is quite a bit different from the specifying function, the idea is “we can save money if we require that the equipment be built or constructed to ASME code, but we don't necessarily require certification.” And I remember about 10 years ago, I got a phone call from a company that just had a boiler installed or assembled, an HRSG. And they said, “We've got this new HRSG, it's been erected, and we just need you guys to send an inspector down and stamp it.” There are some misconceptions on the role of the inspector, on the role of the assembler, and so on.
There is interest in using the ASME code officially, most notably, in Argentina. Argentina is likely, I think, to adopt the ASME code formally as law and require the ASME code as a construction code, probably not to formal certification simply because qualifying authorized inspectors required to mandate ASME compliance would be challenging at least at first, but there will be a mandate that compliance be verified in some fashion, the equipment will actually be stamped. But it's a step toward it, and to also use the National Board Inspection Code to cover repairs and alterations.
I found it difficult to help a buyer see or visualize the difference between ASME certified and ASME built. Several years ago, I noticed a couple of Bentleys driving around my neighborhood. I live in a pretty nice place, but not the kind of place you would expect to see a Bentley. So I looked a little bit closer, and I realized they weren't Bentleys. They were the Chrysler 300. There are actually companies that take the 300, which was deliberately modeled to look similar to a Bentley, and dress it up to make it look like a Bentley. You can buy one used online from a couple different kit manufacturers, and this is basically what you get:
With the Sebring/Bentley conversion -- and this is pulled right off the website -- you get a 2.7-liter Chrysler V-6 and so on, original Bentley badges and exhaust tips, a $3,000 wheel and tire package, and you basically pay for a three-year-old Chrysler Sebring that's been dressed to look like a Bentley for about $20,000. That car is probably worth about $3,000. If you get an actual Bentley that's comparably aged, it's going to cost you about $64,000, but you get a 4-liter twin turbo V-8, and more. It's significantly different -- it's completely different. It looks similar, but they perform very differently; they are equipped very differently.
Extending that concept to pressure equipment, when it comes to the Chrysler or Bentley, it's pretty easy. You open the hood and you can see right away that you are not getting the same car. But what's more important is that you can't operate the Chrysler like you can operate the Bentley. Some features that come with the Bentley cost extra tens of thousands of dollars, including things like a totally different braking system, totally different suspension, or a roll protection system. If you are operating a Bentley at its limits and you get out of control, you are protected; whereas, you can't operate the Sebring that way, so you don't necessarily need those same features to still be safe.
When you extend the concept to pressure equipment, it becomes very, very difficult to tell whether or not a completed pressure vessel actually incorporates the requirements of ASME just by looking at it. You can look at documentation, but when it comes to something like the volumetric quality of the welds, it's not possible to judge by an external inspection. What's more potentially concerning is that you can place that pressure vessel in the exact same kind of serialization code as if it were compliant with ASME. And so what kind of hazard are you potentially introducing by waiving the compliance verification portion of the ASME code that's inherent in the code?
The biggest single driver that encourages the purchaser to seek ASME-compliant equipment, but not require certification, is dollars and cents. It's not uncommon for us to find, having surveyed some of our manufacturing clients, that they are almost always invited to bid or to propose providing pressure equipment in two ways: stamped and not stamped. What they found is in some instances, they have to provide a 30 percent reduction in price over what they would charge for stamped pressure equipment to be able to compete and sell their pressure vessels or their boilers, which raises the question: Where does this 30 percent savings come from? If you have a manufacturer who is offering to provide equipment that meets all the requirements of ASME code and they are going to charge you 30 percent less than another manufacturer that provides you a stamped pressure vessel or boiler, what is generating the savings?
And at first blush it's obviously not just the inspection. The inspection doesn't add up to that much. I wish it did. What are the methods that the manufacturer is using to get that kind of cost reduction? That's something that the buyer needs to consider. And so we go through and we help the buyer identify some of ways that a manufacturer reduces price to meet the buyer's requirements so they can sell their equipment. Following are some of the most common that we find.
The first one is that they use other material, especially in South America where a lot of the code materials have to be imported. They also reduce in-process inspections. Not just in-process inspections by the authorized inspector or third-party inspector, but their own internal inspections, production inspections. They don't necessarily use qualified welders or welding procedures, or they will misapply the procedures and welders that they have. Misapplying NDE methods, you can't provide the same level of evaluation. They do outsource critical activities. Of course, with the ASME code, if you are going to outsource certain construction activities, the person to whom you are outsourcing also must be qualified to perform those functions. Well, if you are not certifying the equipment to ASME, then how are you controlling the outsourcing? For example, you decide to outsource welding or heat treatment or NDE. Who is ensuring that that outsourced function is still being performed to the level of quality you would expect as the buyer of that equipment? Other examples we’ve found: reducing calibration frequency, keeping different records, not retaining records, and, finally, not using qualified third-party inspectors.
I have several slides for case studies and real-world examples of what we found as we have been engaged to provide verification of equipment not stamped by ASME. One thing we remind buyers is that with the ASME code, every three years the manufacturer is audited to determine if they still have an ASME-compliant quality program, written description, and can they demonstrate their ability to implement that quality program, so a joint review. And the manufacturer knows three years in advance that they are going to be audited. They know several months in advance when that audit is going to take place. A highly-qualified auditor goes in, and at least for our customers, we provide a pre-review. We go in about two months in advance of the joint review and audit the manufacturer's quality program ahead of the joint review just the same exact scope of the audit that would be performed in the joint review.
What we find is that there are, in order of frequency, design calculation and drawing issues that need to be addressed and resolved; welding issues; NDE issues; purchasing issues; and material control and calibration. There are other issues, but those are the main problem areas. The point is, if you are expecting the manufacturer (who knows no one is going to be looking at them), to meet all the requirements of the code without third-party verification, and we demonstrate that a manufacturer who’s met all the requirements (a written program in a format that can be implemented), still has issues, it doesn't necessarily mean the manufacturer is not a good manufacturer. What it means is the verification for your client is important, and you can't just abandon it and expect that everything is going to be okay.
Here are some real-world examples. I want to stress again, this is not ASME equipment. This is equipment that purportedly meets the ASME code but is not certified and inspections have been engaged to verify compliance with the ASME code. In one example we have a boiler manufacturer who took welded pipe and substituted it for seamless pipe for cost reasons. They painted it to make it look seamless. The manufacturer's inspectors knew about this, and they knew it was a code problem, but they had been told by production not to worry about it, just go ahead and use it. And the reason for not waiting for the seamless pipe (at least what we were told) wasn't so much the cost of the seamless pipe. It was the delay in waiting for that pipe to arrive and get through customs so it could be installed. Fortunately, there was a third-party inspection performed. I identified the issue, informed the buyer, and the issues were resolved. But if you didn't have some sort of third-party verification, you wouldn't have that.
Another example: the buyer in its specification required ASME compliance, one of which is if you have welded parts, they need to be ASME parts. Well, if you are not required to stamp the actual vessel you are purchasing, then do you require stamping for the parts that are being incorporated into that vessel? And the buyer decided, “No, I guess we do not.” But what they didn’t understand is they were purchasing welded heads, and who knows what kind of welding process was used, if the welders were actually qualified to weld, and if there was a heat treatment performed, and so on.
Another potential issue: when most of these issues crop up, the buyer thinks ASME is ASME and all I'm doing is saving a little bit of money by not requiring stamping, but they don't really appreciate and understand the comprehensiveness of the code, whether it's ASME or whether it's National Board.
I personally participated in this next welding example. I was auditing one of our supervisors, who was auditing an inspector. One of the very first things the supervisor did was to pull up a PQR. When he looked at it, there were five or six different stamps on it from different inspectors who looked at it. And he's looking at the PQR and the WPS, and in comparing it to the joint being welded, realized that the qualified ranges on the WPS did not match up with the weld for production. So the question is, “Why is this WPS stamp acceptable? Does it just mean it exists and is compliant as supported by the PQR?” I guess by itself it was fine, but as soon as you start preparing to use that WPS for actual production, there were problems because of the range that was qualified.
In a similar example, there was another inspector who was requiring the manufacturer, for every welded joint that was being welded (even with the same process) to requalify the welder. He wasn't extending the code's latitude in Section 9 to allow for ranges of qualification. And the manufacturer fought and fought and fought with him and he couldn't get anywhere, and the buyer didn't know enough about ASME to say whether it was okay or not. So they finally said, “Fine, just qualify the welder on every single joint,” and then they looked for other ways to save costs to maintain the margin.
Another example is nonconformity. We inform buyers that they should be looking for evidence that the manufacturer has got a system of addressing nonconformance. If you don't see nonconformities, it’s not a good thing. That means there are going to be nonconformities, no matter what. The question is how they are addressed and if they are properly addressed, and who decides whether or not the proposed disposition is adequate.
In our suggestions to buyers, first we recommend that they should define their mandatory requirements up front. Some examples might be that in no case will they allow the manufacturer to substitute material. They want ASME code material, no what matter. They want ASME-qualified materials in their country. They may relax requirements, again, understanding they are not going to stamp the final work. Most countries in South America, especially Brazil, Argentina, and countries like Mexico, do have internal programs for qualifying nondestructive examples, and the programs they have in place are robust, very similar to ASMT’s, and yet they don't meet the ASME code. But the buyer might decide that's fine and are willing to accept the national program for nondestructive examination as meeting their requirements.
The other thing they should do is to demand the manufacturer identify the source of the cost savings. Don't just accept at face value they are going to save 30 percent. Ask them to document for you how they are generating savings.
To summarize -- and, again, this is a summary for the buyer – it is key that you basically do what the ASME code and National Board Inspection Code have already incorporated, and that is to require qualified, third-party verification to make sure that it actually complies with your specifications and especially if that specification includes the ASME code or elements of the National Board Inspection Code.
But the take-away for this audience is that we see opportunities, especially with encouraging increased adoption of the National Board Inspection Code. With the economic climate we are in, the focus in Latin America, especially in certain countries like Colombia, where nearly all pressure equipment being produced to ASME code, stamped and non-stamped, is for oil and gas, and the focus there now is extending asset life and on repairing or altering assets that are already installed rather than purchasing equipment. There is opportunity.
We see opportunity for the buyer to insist on repairs certified to the National Board Inspection Code. If you were to look at the pedigree of equipment installed in countries in South America, especially the major markets (Ecuador, Colombia, Peru, Chile, Brazil, and especially Argentina), which has widespread adoption of the ASME code (although it's not necessarily formally used), you can establish the original code of construction, you can use the National Board Inspection Code, and you can use a manufacturer that's got an R program, or a repair firm that’s got an R program in place, to certify the repairs and demonstrate to the buyer the difference between the approach used by ASME and by the National Board to ensure the integrity of the repair to the original construction, and I think that will increase the formal adoption of the code.
At least that's what our focus is now. And I think it also demonstrates the value of the cost reductions that have resulted. Because the fact of the matter is, if you are asking for equipment that meets our requirements of the ASME code, and your expectation is you are going to save money by finding a manufacturer that doesn't have a certificate of authorization and use inspectors other than those that are authorized to perform the inspection, your costs actually go up. If we are talking 100 percent compliance and we are talking the same level of qualification, the cost actually increases, it's not reduced. But I think the only way to demonstrate that is by helping the buyers to see the connection.
MEETING ATTENDEE: Does HSB provide inspection services for non-ASME repairs and construction?
MR. MASTERS: We do, we do. And in fact, that's where we get into the demonstration of the cost differences. One of the drivers behind this presentation of "To Stamp or not to Stamp" is that we frequently have buyers or manufacturers say to us, “Look, I don't want to certify this equipment, but I want you to certify it and to provide me documentation saying that it meets all the requirements.”
So the next question we ask is, “What's the scope? What do you mean by it meets all the requirements of the ASME code? You mean you use it in the design formulas and the design meets the code? Do you mean that every single aspect of the ASME code will be met?”
And it's when you try to pin down the scope with them when things start to get a little bit fuzzy. Further than that: “Okay, if you want me to verify that this equipment meets the ASME code, I need to look at your quality program to make sure it meets the requirements of the code and make sure you can demonstrate you've implemented it.”
The alternative is that I can inspect the equipment 100 percent, which of course throws the inspection costs through the roof, and that's where the cost differences come into play.
So the answer to the question is we absolutely do provide that service. Probably 90 percent of the time when we have an invitation to quote those jobs, it doesn't turn into an actual inspection process because we can't pin down the scope or the level of inspection that would be required to verify that the equipment actually complies with the ASME code.