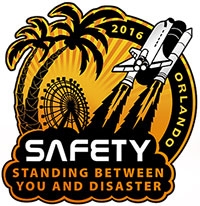
The 85th General Meeting Feature Presentation
Gary Scribner
The National Board Inspection Code
The following presentation was delivered at the 85th General Meeting Monday afternoon session, May 9. It has been edited for content and phrasing.
Introduction:
Gary Scribner served as Deputy Director for Missouri for seven years before joining National Board staff in January of 2014 as the National Board manager of technical services. The Baltimore native served 22-1/2 years in the United States Navy, where he received much of his boiler training. He joined the state of Missouri as a field inspector in 2003. He was made interim deputy director in 2006, and later that year was named permanent deputy director. Mr. Scribner became a National Board member in 2007. He was elected to the National Board’s Board of Trustees in 2009 and later as second vice chair. One of the most active National Board members, he served on the National Board Inspection Code (NBIC), and continues to be an advocate of many National Board safety programs.
Mr. Scribner's slide presentation can be accessed here.
Mr. Scribner:
Thank you. When I was first asked to make this presentation, I wondered why I would talk to this group about the NBIC. But as I talked to people this week, I realized that many of us tend to refer to the part of the NBIC we work with all the time and forget about the other parts of the NBIC.
The NBIC has evolved and will continue to evolve, and there are parts of the NBIC that, even though we don't use them on a daily basis, we have to look at them to provide proper guidance to our clients and to those we are providing inspection work.
The purpose of the NBIC is to maintain the integrity of pressure equipment after fabrication, and we do this by providing common rules for installation of the equipment, inspection after it's been placed in service, and guidelines and requirements for doing repairs and alterations to this equipment. And this ensures equipment will be operated continually and safely.
When the ASME Code was formed, it was a code of construction, but it had no standard rules for inspection and repairs of pressure-retaining equipment. So the chief inspectors approached the National Board and asked the members to help them establish these common rules. The first edition of the NBIC was published in 1946, and it became an ANSI standard (American National Consensus Standard) in 1992. And this is where we really started to take off.
So what does it mean to be an ANSI standard? The NBIC must be balanced. Committees have to be balanced to ensure all individuals with a concerted interest are able to participate in its development. I would recommend that anyone who wants something added or changed in the NBIC to please let the committee know. This is not just what the committee wants to develop; it's what is needed by those people who use and repair the equipment on a daily basis. There are guides in the NBIC for submitting those types of requests which I will cover later.
Our current interest categories for the NBIC committees are regulatory and government agencies, users of boilers and pressure vessels, manufacturers of pressure equipment, repair companies, and inspection agencies.
Additions and changes are made to the NBIC, and they have to go out for public review and comment. Every two years when we think we have a book that's ready to go to print, before we can do this, it still has to go out for public comment. This provides the public the opportunity to have input, which can include governmental agencies, owner/users, or the public at large. When it's out for public review, anybody can put in a comment. All these comments have to be addressed by the committee. They can't just say, “Well, we don't agree with that, we are not going to do it.” They must address it to some degree and go back to the commenter with what they think about his comment. And it may be to open a new action item; it may be a way to improve this in the future. The NBIC is never finished. We just continue to improve it.
Currently the committee is made up of the main committee, which has the final approval of what they hope to put in the next edition of the NBIC. They get all their information from subcommittees. Subcommittees do the final polishing work on whatever has been presented to them. They send information down to the lower groups, which would be the subgroups, task groups, and working groups, to help develop the content and do all the real footwork to develop the NBIC. The four main subcommittees are installation, inspection, repairs and alterations, and pressure relief devices. These subcommittees also have subgroups that do all the footwork. We have some very unique subcommittees that research and have expertise in unique items, such as your locomotive boilers, graphite vessels, fiber-reinforced pressure vessels, and historic boilers.
The NBIC is issued and updated every two years. As most of you know, the last edition came out in July 2015. The committees meet twice a year, and it's typically for four days. I want to point out that just because the committees only meet twice a year, that doesn't mean the work stops. There are letter ballots that go out and small task groups that get together (typically by teleconference and sometimes in person) to continue developing content to be ready for the meetings.
January is our first meeting of the year. We typically hold it in various locations that are chosen by the committee. The next meeting is January 2017 in San Diego. All these schedules are on our website, and I would invite anybody here that has interest in being part of the process or has concerns they want to address with the committee, to please come to the meeting and see how we develop the NBIC.
In July we typically hold the meeting at the National Board headquarters in Columbus, Ohio. That meeting is coming up very quickly. As I have talked with people this week, including some of my fellow presenters, it's amazing how long it's been since some of you have been to the National Board. So that would be a really good time if you are interested to come and see how much we have increased our training department and all the facilities to help train inspectors. All NBIC meetings are open to the public, and all the meeting schedules, agendas, and minutes are posted on our website under the NBIC tab.
The NBIC rules is an aspect of the NBIC that people don't fully understand. Most people think it's only for inspectors, and that is not a true statement. It's intended to provide rules, information, and guidance to manufacturers, jurisdictions, inspectors, owners of vessels, the users of pressure equipment, installers, contractors, and any other individuals or organizations performing or involved in any type of post-construction activities. And by doing this, it encourages the uniform administration of rules pertaining to pressure-retaining items.
The scope of the NBIC is this: the NBIC recognizes three important areas of post-construction activities where information, understanding, and following specific requirements will promote public and personnel safety. And these areas specifically are the installation, inspection of pressure equipment, and repairs and alterations of pressure equipment.
NBIC Part 1, Installation
So let's dig into it. Currently, Part 1, Installation, provides general guidelines dealing with pressure equipment in the following areas: the application of rules; certification and jurisdictional requirements; responsibility; equipment certification; jurisdictional review requirements; inspection; boiler installation report; and a guide to complete it. There is currently an ongoing effort within the NBIC Committee to move some of the more common requirements through Part 1 into the general sections that are not repeated. Some common things like ladders and catwalks that are spread out in different areas in the book will be going into the general section and it will be referenced so we don't continually repeat the same things and also to maintain consistency.
Section 2 of Part 1 defines specific requirements dealing with power boilers. The general requirements covers things such as supports, foundations and settings; the clearances for boilers; boiler room requirements, including the exits, requirements for ladders and runways when it's above eight foot off of the operating floor; drains, so you have a way not to flood the boiler room and get rid of all the waste, and also availability of clean water so you can clean the boiler. Source requirements include: feedwater, pumps, valves, fuel, electrical wiring, remote emergency shutdown switches, ventilation and combustion air requirements, lighting requirements for the boiler room (so the operator can see what he's doing), and emergency valves and controls. Discharge requirements include the chimney or stack requirements, ash removal when appropriate, drains, connections, and pressure rating.
Operating systems include breechings and dampers, burners and stokers, steam supply, condensate and return, blow-off, and controls and gauges. Pressure relief valves include the valve requirements for power boilers, so the number of valves, the location of these valves, capacity requirements, and set pressure. And there are some specific requirements dealing with other types of power boilers more in depth, such as a forced-flow steam generator, superheaters, economizers, pressure-reducing valves, and mounting and discharge requirements. Testing and acceptance is also included in this section. Once you put a new boiler in place, a lot of testing takes place, so there are some general guidelines that include pressure test requirements, nondestructive evaluation, and system testing. And the final acceptance by the jurisdiction or whoever would be doing this acceptance, and obviously the boiler installation report we talked about earlier.
Section 3 of Part 1 contains installation requirements like we have covered for the power boilers, but it covers these requirements for steam heating boilers, hot water heating boilers, hot water supply boilers, and potable water heaters.
Section 4 of Part 1 contains requirements for installation of pressure vessels. And these are very general when dealing with pressure vessels. They are not specific types of pressure vessels.
Section 5 of Part 1 has the rules for the installation of piping systems.
Section 6 of Part 1 is our supplements section, so it has specific rules for the very unique types of vessels such as Yankee dryers with finished shell outer surfaces, safety valves on the low-pressure side of steam-reducing valves, and installation of liquid carbon dioxide storage vessels (or the vessels that are used in the beverage systems throughout the country and the world right now).
In 2015, Supplement 4, installation of biomass boilers was added, as was Supplement 5, the installation of thermal fluid heaters. Sections 7 through 10 are actually the same through all of the books. Section 7 is the policy for metrication. So if you are doing a conversion, have a foreign boiler, it tells you how we would want you to convert it if you are doing repairs or alterations or something like that.
Section 8 is preparation for technical inquiries to the National Board Inspection Code.
Section 9 is the glossary of terms or definitions.
Section 10 was drastically changed with the 2015 edition. It has all the approved interpretations for previous editions of the NBIC listed, and it's done in a format now that can be looked up several different ways. The actual up-to-date and complete interpretations are found on the website under the NBIC tab, and when you go there, you are able to look up these interpretations, click on specific interpretations you may think is what is relevant to what you are doing, and it will take you directly to that interpretation. If it's not what you are looking for, you hit the back button, and it takes you right back where you were so you don't start at the top of the list; you can continue going down through all the interpretations.
A word of caution: Check with your local jurisdiction to see if they accept older interpretations and if it's still appropriate to what you are doing. We consider the interpretations only applicable to the edition or addenda they were issued to, so it would really be up to the committee (or jurisdiction) to answer if it is still appropriate.
And Section 11 has an index.
NBIC Part 2, Inspection
NBIC Part 2, Inspection, provides information and guidance needed to perform and document inspections for all types of pressure equipment. Once again, that's not only jurisdictional inspections; but for whoever is doing the inspection. Included is inspection information on personnel safety, nondestructive examinations, and tests. Also included: types of pressure equipment (good for training somebody), failure mechanisms, fitness for service requirements, risk-based assessments (helpful for companies more so than inspectors), and performance-based standards.
Section 1 of Part 2 contains general requirements for inservice inspection of pressure-retaining items, including: administration, personnel safety, personal safety requirements for entering confined spaces, equipment operation, inspection activities, pre-inspection activities, inspection planning, preparation for internal inspection, and post-inspection activities for pressure equipment in general.
Section 2 of Part 2 includes detailed requirements for inservice inspection of boilers and covers the service conditions, conditions of the boiler room, internal and external inspections, leakage, corrosion considerations, piping, parts, and appurtenances, flanged or other connections, gauges, pressure relief devices, controls, and records review. Section 2 also includes concerns for specific types of boilers such as cast iron boilers, firetube boilers, watertube boilers, electric boilers, fire coil water heaters, fired storage water heaters, thermal fluid heaters, waste heat boilers, or the black liquor recovery boilers.
For pressure vessels, we cover a lot of the same material: service conditions, internal and external inspections, inspection of the parts and appurtenances on the vessels, gauges, safety devices, controls and devices, and a records review. We also have requirements for specific types of vessels, such as deaerators, compressed air vessels, expansion tanks, liquid ammonia vessels, pressure vessels with quick-actuating closures (such as autoclaves), anhydrous ammonia nurse tanks, and pressure vessels for human occupancy (PVHOs).
The NBIC also covers inspection requirements for piping systems. And then we go into pressure relief devices, including inspection requirements for the pressure relief devices, rupture disks, testing and operation of pressure relief devices, and recommended inspection and test frequencies for pressure relief devices. The jurisdictions, I'm sure, get these questions all the time from owners and users as far as when they should test their pressure relief devices or set up a PM program for that.
Part 2, Section 3, Corrosion and Failure Mechanisms, is actually an area that all inspectors should be looking at from time to time to refresh their memory. If they are signing off on repairs and alterations and they are not familiar with some of these corrosion and failure mechanisms, they really are not doing the client any justice, because if they just repair the damage and send it back out, it could come back in. So it's very important for inspectors to review this from time to time to keep current, even if they don't deal with inservice inspection. And it covers a wide variety of areas: the macroscopic corrosion environments, control of corrosion, process variables, protection, material selection, coatings, and engineering design. Failure mechanisms include fatigue, creep, temperature effects, hydrogen embrittlement (if anybody has ever been inside an aerator, that's something you definitely would want to look for), high-temperature hydrogen attack, hydrogen damage, bulges and blisters, overheating, and cracks.
Section 4 gives us a description of the NDE or nondestructive examination methods. Testing methods for nondestructive methods is a good starting point for somebody who is not familiar with them, as it describes them very well. Also included: pressure tests, liquid pressure tests specifically, and pneumatic pressure testing. Also included is determining inspection intervals for vessels that are subject to erosion, exposed to corrosion, where corrosion is not a factor, and exposed to inservice failure mechanisms. And some good information on risk-based inspection assessment programs, otherwise known as RBI, is included. It gives you the key elements if you are trying to do an RBI assessment program to help you develop that and includes RBI assessments, risk evaluation, risk management, and jurisdictional relationships when setting up these RBI programs.
Section 5 covers the stamping, documentation, and forms and addresses replacement of the stamp data during inservice inspections, including authorization, replacement of stamped data, and the reporting of the replacement of the stamped data. And this is becoming more and more so. I know from my last 1-2 years in a jurisdiction, it went from a couple a year probably to 30 to 40 a quarter that were coming in.
National Board inspection forms, including the replacement of stamped data, boiler and pressure vessel data report, boiler-fired pressure vessels report of inspection, pressure vessel report of inspection, reports for fitness for service, and a guide for completing fitness for service assessment reports can be found in this section, too.
Part 2, Section 6, Supplements, provides information regarding specific types of pressure equipment, including locomotive boilers, historical boilers, graphite vessels, FRP vessels, Yankee dryers, DOT transport tanks, LPG service vessels, safety valve pressure differential, change of service requirements (and that is new for 2015), and high-pressure composite vessels (which is also new for 2015). One other thing we changed in the 2015 Edition at the request of those who utilize these supplements is instead of just having Supplement 6 on these tabs, each of these supplements are tabbed separately to help you find them.
Part 3, Repairs and Alterations
Part 3, Repairs and Alterations, provides information and guidance to perform, verify, and document acceptable repairs or alterations to pressure-retaining equipment. It provides alternative methods for examination, test, and heat treatment when the original code of construction requirements cannot be met. You simply cannot do all the things if it's been in service or if it has other piping systems installed, or based on what the contents are that you may not be able to do it in the factory when you are out in the field doing repairs and alterations, and the NBIC acknowledges this. Specific acceptances of proven repair methods are included.
Section 1 of Part 3 covers the general and administrative requirements, including construction standards for pressure-retaining items, the use of the National Board commissioned inspector, the National Board R program (it gives you the details of that, along with the quality system requirements for the R program), National Board VR program with the VR quality system requirements, and the National Board NR program for nuclear repairs, along with the quality system. The NR section is a complete rewrite for 2015, so if you deal with the nuclear side at all, I would recommend you go back and look at it. It's significantly changed.
Additionally, a lot of the administrative requirements can be found on our website under the Stamps and Marks tab. You can pull up the specific accreditation program you are looking at, and additional administrative requirements will be found there.
Section 2 of Part 3 covers welding and heat treatment: welding procedures specifications, standard welding procedure specifications, performance qualification, welding records, welder's identification, welder's continuity requirements, welder's continuity records requirements, AWS standard welding procedure specifications, preheating, postweld heat treatment, and alternative welding methods without postweld heat treatment can be found in Section 2.
Section 3 of Part 3 includes the requirements for repairs and alterations: material requirements, considerations for replacement and a guide for replacement parts, drawings, design requirements, calculations, routine repairs, examples of the routine repairs, repair methods, and defect repairs. We have found, as we go more international, things that we consider -- that we all understand, the terms we understand, are not necessarily understood throughout the world, so some of these terms are actually being defined right now. Even though we understand them, everybody doesn't. A good example is that I'm reading a book right now that deals with repair of fire-tubed boilers in Britain. And you would think with a common language, it should be all the same. To them a fire-tubed boiler only has one fire tube. Everything else is a smoke tube. Definitions are becoming more important as we move forward. This section also covers information on the requirements for wasted areas, seal welding, re-ending or piecing of tubes, patches, repair plan, alterations, rerating vessels, and examples of alterations.
Section 4 covers examination and testing, and includes: nondestructive examination requirements; pressure gages, measuring, examination, and test equipment; examination and test for repairs and alterations; test or examination methods applicable to repairs specifically; and pressure-testing parts and specific examination methods for alterations.
Section 5 covers certification, documentation, and stamping: the preparation and distribution of the R forms (R-1 for repair and the R-2, alteration). Requirements for an R log by the R certificate holders, stamping requirements for repairs, alterations, parts (specifically if you have small parts), fiber-reinforced vessels (very unique), and pressure relief devices. And if you have to remove the original stamping or nameplate during a repair or alteration, there is guidance provided in this instance.
Section 6, Supplements, has some additional information for those unique types of vessels: locomotive boilers, historical boilers, graphite vessels, FRP vessels, Yankee dryers, DOT transport tanks, and pressure relief devices. And then we go on to some design systems for pressure relief devices in compressible fluid service, and procedures to extend the VR Certificate of Authorization and stamp to ASME NV stamped pressure relief devices and LPG service vessels.
For 2017, current plans are to have a Part 4, so we will move from three parts to four parts, and Part 4 will be for pressure relief devices. The requirements for pressure relief devices in Part 1 and Part 2 will stay the same as they are today, that will not be affected, but they will be duplicated in Part 4. And this does a very important thing for us: it puts that information directly in front of that subcommittee constantly, so they constantly maintain it and make sure it's up-to-date, and that will thus keep Part 1 and Part 2 up-to-date dealing with pressure relief devices. The majority of the requirements for pressure relief devices in Part 3 will now be in the new Part 4.