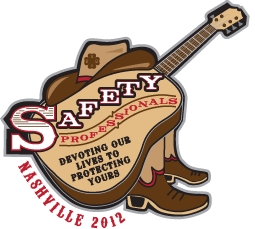
ESTABLISHMENT OF A FEDERAL INSPECTION AGENCY AT OAK RIDGE NATIONAL LABORATORY
The following presentation was delivered at the 81st General Meeting on May 14, 2012, by John Swezy. It has been edited for content and phrasing. Mr. Swezy’s accompanying slide presentation can be viewed here.
John Swezy is a mechanical engineer employed by UT-Battelle, which is the prime management contractor for Oak Ridge National Laboratory. In his capacity with the fabrication division, he oversees the inservice inspection program. Mr. Swezy began his career in the U.S. Navy where he accumulated 15 years of active duty. Having achieved the rank of machinist mate chief petty officer, he held a number of critical nuclear positions, including that of a submarine nuclear power plant operator and engineering watch supervisor. A native of Missouri, Mr. Swezy obtained his Associate of Science degree from the University of the State of New York. He entered the pressure equipment industry as a boiler and pressure vessel inspector for Lumbermens Mutual Insurance Company. In 1996 he became a member of the Kemper home office staff. Mr. Swezy subsequently became a staff technical specialist for Hartford Steam Boiler. In 2009 he started Boiler Code Tech L.L.C., an engineering consulting company. As an active ASME volunteer, Mr. Swezy has served on several important ASME codes and standards committees and subcommittees. He holds an inservice National Board commission.
MR. SWEZY:
Today I'm speaking about the establishment of a federal inspection agency at Oak Ridge National Laboratory (ORNL). Oak Ridge is a facility that was started during the Manhattan Project, and it has a fairly significant place in history.
The premise for pressure equipment safety at Oak Ridge National Laboratory started when we were required to comply with directives from the Department of Energy (DOE), since it operates the national laboratory chain throughout the U.S., most locations of which are located on U.S. federal property.
The boiler and pressure vessel laws of most states, though, specifically exempt federal property from their requirements. And so they recognize federal sovereignty over those venues, and they specifically exclude boilers or pressure vessels from coming under their jurisdiction. The U.S. government has ownership and ultimate responsibility over all these boilers, pressure vessels, piping systems, and other kinds of equipment installed and operated in these facilities. Responsibility for the safety and safe operation of that equipment falls under the federal government and the Department of Energy.
At Oak Ridge, our prime management contractor is my employer, UT-Battelle. We have assumed that responsibility by delegation from the Department of Energy. The primary expertise for pressure equipment in engineering and inspection rests within the surveillance office, which is the office that I work out of, and this is part of the fabrication hoisting and rigging division. Now, I could show you a big long chart of our organization, but suffice it to say, it's fairly short in terms of pressure safety. In my position as a mechanical engineer, I'm assigned to the surveillance office, and I've also been assigned responsibility for developing and managing the pressure equipment safety inspection and assessment program. This isn't my only duty, but it is one of my primary duties.
All federal property is subject to compliance with a federal regulation that is known in the business as 10 CFR 851. This regulation requires a safe workplace to be established for the workers. Part of the Code of Federal Regulations, 10 CFR 851 is a comprehensive regulation that requires the development and implementation of a personnel health and safety program to ensure a safe workplace. And it addresses many areas, not just pressure safety. Some of those include construction safety, fire protection, explosives, firearms, biological hazards, and occupational medicine. The list goes on extensively, but you get the idea.
10 CFR 851 requires that pressure equipment and systems comply with recognized consensus, standards such as the ASME Boiler and Pressure Vessel Code and ASME Piping Codes, among others, and the strictest applicable state or local codes to the greatest extent possible. You might hear that and think, how can it be subject to the strictest local or jurisdictional codes when they aren't even applicable by their own exemption? And their answer is that we read those codes anyway, even if they don't apply to us, so we have to try to apply the tenets of those codes when we develop our pressure safety program. So we do have some influence on jurisdictional laws in the area where we are located.
Whenever codes such as the consensus standards I mentioned can't be applied for whatever reason, and usually that's because the materials are not code-accepted materials, the configuration of the object can sometimes be a problem. But generally most of the codes have provisions for alternative design methods. But whenever we can't meet one of those codes, the systems and components have to be designed and constructed “to provide equivalent protection and ensure a level of safety greater than or equal to the level of protection afforded by the ASME or the applicable state or local code.”
There is a lot of opportunity in that statement. Equivalent protection can be defined a number of ways. What is equivalent, for one? And that's something national laboratories are currently struggling with, and in fact it's something that we tend to meet on a regular basis and try to come to some mutual understanding so we can report to DOE with the same plan for how we are going to meet that.
There are some specific measures that have been given which are intended to address how this equivalence is achieved, but those measures are not well detailed or defined. One of the things I have learned working at Oak Ridge National Laboratory is if you have a question of how DOE wants you to comply with something, they are not the best place to go to for the answer, because they generally won't answer the question. They will say, yes, you need to comply with this, now you tell us how you are going to do it.
And so this task team of all the other laboratories meets on a regular basis, and we have been working on implementing an equivalence document. And because of my experience with codes and standards and dealing with codes and standards for a number of years, I have been able to put together what I consider the primary draft document, and most of the other laboratories have chosen to adopt it as I have written it with a few minor changes.
And so we have kind of assumed the leadership role in this effort, which is also one of the reasons why we were one of the first to become a federal inspection agency. Under 10 CFR 851, Part 4, the pressure safety requirements require a personnel health and safety program for pressure safety to be developed and implemented. Now, this is an all-encompassing statement here. The Part 4 requirements specifically require you to address boilers and pressure vessels, yes, but they also address pressure systems and components. And the way that Part 4 is written, piping systems are included in this, and so are things such as vacuum vessels. And anyone in Section 8 who has had to deal with me for the last few years knows that vacuum vessels have become one of my more recent crusades. Because if you know Section 8 very well at all, you know that vacuum vessels are typically considered outside of the scope. So it's to our benefit to try to design vacuum vessels that meet ASME code whenever we can just because of this regulation that we have to comply with.
At Oak Ridge National Laboratory, we have something we call the standards-based management system which provides guidelines for the owners or purchasers of pressure equipment for the design, operation, hazard assessment, reconfiguration, et cetera. This guideline we call the pressure systems safety requirements is something that's taken a while to put together, and it's only been implemented within the last 12 to 18 months.
The ORNL's pressure systems safety program elements include the following: identifying personnel hazards and identifying hazard-mitigating strategies. And these include obviously engineering controls and administrative controls, but also personnel protective equipment whenever it is appropriate.
We also need to do periodic reviews of accidents to evaluate the effectiveness of mitigating strategies and to identify opportunities for improvement where they may exist. And again these things are all mandated by this regulation. These aren't things we just came up with on our own. Management audits are also required to determine the effective implementation and to identify opportunities for further improvement. And then we also have periodic inspections to ensure fitness for service, just like the jurisdictions do.
The pressure safety program that we have put together applies to both currently installed pressure equipment and systems, and to newly constructed and installed pressure systems. And the breadth of this applicability requires us to do a number of things.
First of all, we need to identify and evaluate currently installed legacy pressure equipment and pressure-retaining items for continued operation and compliance under the rules of 10 CFR 851. Now, if you think about this a little bit, you might realize that it can be a daunting task for a facility that's been in place since the 1940s during World War II, and the fact that even back in those days nobody seemed to care what they did out there because that was a government spook territory, and they kind of let people do whatever they needed to.
And in addition to that, the people who worked out there adopted a "this is a research project, we don't need to do that" attitude. So we got some real surprises when we started trying to identify and document this legacy equipment. And then we have to develop procedures and guidelines for procurement, design, and construction of new pressure-retaining items.
Some of the things we kept in mind when we were putting this program together were linkage to the NBIC and to jurisdictional laws, because that was already established within the tenets of 10 CFR 851. Yes, the federal regulation actually acknowledges the existence and importance of the NBIC, which I think is a good thing. They also recognize the importance and significance of jurisdictional laws. The National Board of Boiler and Pressure Vessel Inspectors is recognized by state and federal authorities as technical experts in the pressure equipment safety area, and so this was a big thing that we decided we would leverage it to our advantage as well. As a result of that, we chose to have an inservice inspection program that was intended to do a few things.
First of all, we wanted to implement and recognize the consensus standard, such as NB-23 of the National Board Inspection Code. We also wanted to apply some risk-based evaluation safety criteria, such as ASME FFS-1/API-579, fitness for service. And this is a process that's still continuing to evolve, but we've at least put a stake in the sand and are starting to work forward from it. We have to also apply objective standards for development of our own inservice inspection program, and conveniently for us, the National Board had developed NB-390, qualifications and duties for federal inspection agencies performing inservice inspection activities.
This is a real good thing for us, because as an entity serving DOE, we had to have some way of proving our credibility and to establish some kind of a basis for us to move forward as experts in taking charge of this responsibility. This was a real convenient vehicle for us. So we decided that we were going to attain accreditation by the National Board as a federal inspection agency which would earn us that recognition as a technically competent organization from a body that was also recognized as technically competent. So it wasn't a chicken or the egg kind of thing. We actually had a basis for establishing that we had proven our expertise.
We also found that this did a really good job of complementing our current ASME code accreditation to apply to ASME U and U-2 code symbol stamps, and for the R symbol stamp, which we already had. And in fact it's really been a great boon for us. Since we have an R stamp program and we are now a federal inspection agency, we are able to do the inspections for many repairs that are carried out by the fabrication shop on the lead. And we don't have a lot of them, but it's nice to be able to do that and do so at a moment's notice without waiting for an outside inspector to come in.
Our installation, as I mentioned before, originated with the Manhattan Project during World War II, so we have some real interesting pressure equipment relics, and we also have new equipment, too. You probably would be amazed to see how much new stuff there is at Oak Ridge National Laboratory.
As we began the process of trying to get a handle on what it was we had to deal with and to survey and catalogue these pressure-retaining items that were installed, we expected to have a lot of difficulties in assessing these items. Since many of these items are non-code, they have little or no identification; they have virtually no design of construction information or basis present or documented in any way, shape, or form. And to make matters worse, we couldn't do it all ourselves. We had to ask the area managers to go out and identify and notify us of the vessels that they had present in their facilities so that we could begin the process of assessment.
We knew that we would find more as we went on, but we needed them to make the initial identification and notification so we could start taking steps to record and document these items. It's hard to communicate with somebody when you ask them to identify what pressure-retaining items they have within their building, and they look at you and say, “Well, none.” And you ask them if they have a sprinkler system with piping? “Yes.” Do you have a hot water heater? “Yes.” What about heat exchangers and pumps and an air-conditioning unit? “Well, yes, we have all of those. Are those pressure-retaining items?” Well, absolutely they are. And there is other equipment on-hand that is pressure-retaining, and we have had to educate them a bit.
To give you a few ideas of what we are dealing with, one of the first things ever constructed at Oak Ridge is now an historical landmark, and I believe it's an ASME-recognized landmark as well. It's the graphite reactor project that was initially built there and operated/overseen by Enrico Fermi and Albert Einstein. The relics and remains of it are still present at the laboratory, but all you will see now is a big yellow painted brick structure with yellow and magenta ropes and signs around it telling you to stay away. But it's still present and it's identified as a landmark. It’s probably one of the oldest things we have at the lab.
I'm particularly proud of one of the newest items in the lab. It is called a cryo module. This module is a large cylindrical vacuum vessel that contains high and low beta cavities inside of it. These high and low beta cavities are surrounded by super-fluid liquid helium operating at two degrees kelvin for the purpose of providing electromagnets with super-conducting capabilities.
This is the very first linear accelerator cryo module that was ever built in compliance with ASME code, and this particular project is one of the reasons why I was hired by Oak Ridge National Laboratory to act as a codes and standards consultant to make this happen. This particular cryo module not only is the very first one to be built to ASME codes, but it was also recently put into the test cave and tested with a proton beam, and it tested with some of the highest performance numbers of any cryo module that was ever built. So we are very excited. And, in fact, when we went to build this thing, we had a design review meeting where we brought in experts of linear accelerator design and fabrication from all over the United States to throw darts at us and try to find reasons why we couldn't do it.
When we took care of all their darts and solved all the problems, they not only said well done, but they said we have established a new way forward for building linear accelerators. So I'm very proud and excited to show you this picture. This is a spallation neutron source. Those of you who aren’t physics geeks might not know what this is, but this is a place where they take a highly-energized proton beam and shoot it at a target filled with mercury to generate a stream of neutrons.
A particle accelerator is part of this process. In the target building, a proton beam comes in and hits a target. And because of its speed and interaction with the mercury, it produces neutron beams that are then sent down what we call beam lines to research projects.
These beams are controlled with the energy level that comes out of this neutron production process through a series of what we call choppers that break the beam up into certain frequency lengths, and then these beams are what are considered a cold neutron source to look at the material structures of various different objects.
Now, this might sound really esoteric, but let me boil it down for you. If you wanted to look at something to try to get its detail and you didn't have enough light, you might grab a flashlight or turn on an overhead light in a room. Compared to the neutron sources we used before this was built, this is like the difference between a 15-watt light bulb and a 1000-watt light bulb. This is a significant advancement in materials research and science, and it reached a one-megawatt energy level, setting a Guinness record after doing so multiple times up to that point. At the moment it’s the most powerful spallation neutron source in the entire world.
That's significant because of what they have been able to learn through the studies of carbon nanotubes and various other things that have advanced technology. They analyze things such as the structure of oils and lubricants. And you just can’t believe what they use this thing to study.
Next, a high-flux isotope reactor is a reactor about the size of the ones that I used to operate on submarines. It's a very small capacity, less than 100 megawatts, and it operates at a thermalized low temperature to produce cold neutrons again for doing materials research. Surprisingly enough, it only operates at a few hundred degrees, and it operates at very, very low power levels. This reactor was originally designed to create isotopes for doing other research, but it has since been turned into doing neutron research by creating neutron beams that we can study with.
Then we have a Jaguar Super Computer. Up until about a year and a half ago, it was the number three fastest and highest capable computer in the world. It's currently in the process of being re-racked with brand new multiple level Cray chips that are going to make it the number one computer again, and it's going to be renamed the Titan Super Computer. And when it's done with the re-racking and re-chipping process, it's going to have a capacity of 20 petaflops. That's a number I can't even wrap my head around, but from what I understand it's capable of twenty trillion trillion calculations per second.
I share all of this because these things are facilitated by auxiliary systems that have pressure equipment on them. If you were to walk in this computer room while it was operating, the noise level would be about 97 decibels because of the cooling fans that it has on it. The cooling fans push air through, and the floor that you see in front of the super computer is a false floor. There is about six or seven feet of open space below those computers where cooling water runs in and out. And we have several centrifugal air conditioning units providing cooling for this computer when it's up and running.
The same is true with a spallation neutron source. In addition to the normal hotel service type pressure equipment that you have like boilers and air receivers and things like that, we also have the vacuum vessels, we have a cryogenic cooling plant that's probably the most unique thing that you ever saw in your life, because it's basically a large refrigeration unit that uses helium as its cooling medium. And if you don't have an appreciation for how cold two kelvin is, when they start this thing up from a normal temperature, the cryogenic plant at Oak Ridge takes approximately four hours to get down to four to six kelvin, but it takes another eighteen hours to twenty-four hours to get down to two kelvin. So there is a large amount of work to get down to that kind of temperature.
Some of the challenges we have for pressure safety inspection is to establish a risk categorization criteria to prioritize our efforts. We wanted to identify the highest risk objects first, because we wanted to get any of the big smoking guns out of the way as early as possible. And once we did, we decided to apply a graded approach to their inspection and evaluation of the remaining items.
We also chose to implement a forensic engineering process to fully assess each pressure-retaining item that we have identified and inspected for current safety and to determine the item's fitness for service. And the reason why we had to enter into this forensic engineering process is because many vessels are non-code, they don't have a nameplate, we have no idea what the design basis was, and so we basically have to work backwards. So every identified pressure-retaining item is then subjected to a complete inspection following NB-23 guidelines, and I have written inspection procedures to tell our people how to do that.
Whenever physically possible, we also take UT thickness readings on every one of these items when we do the inspection. This gives us an idea of what the current condition is. And when I say UT thickness readings, we have an established model, if you will, of how those UT thickness readings are going to be applied so we get a good representative set of readings. Then that inspection report that documents all of the inspection in the UT thickness readings is sent to me, the mechanical engineer, for review and assessment. And at that point I apply screening calculations to verify the object is safe for continued operation at its service rating and to calculate a projected service life.
For those screening calculations, they are essentially the same as when you are designing a new pressure vessel or a new boiler per the ASME code, and we need some basis for applying that. It's really easy if you have a vessel that's got a manufacturer's data report. It's not quite as easy if you only have a nameplate but no data report. But if you have a big hunk of metal that's got nothing on it, you have to start from some assumptions and work your way forward. And so we have determined the pressure ratings for most of the systems in our facility, then we take the geometric shape, and we have a generic material identification that tells us if it's carbon steel or if it's stainless or something nonferrous.
And then based on those UT thickness readings, my calculation tells us what the maximum pressure rating of that object can be for whatever we expect the normal service temperature to be. There are several assumptions involved in that process, but most of the vessels we have to do this for are things that are pretty benign, like steam-to-water heat exchangers for building heating and that kind of thing. But it's been an interesting process because we probably go through a lot more review and evaluation of each object and assessing its remaining service life and applying some kind of a safety evaluation to it than probably even most of your jurisdictions do.
So whenever an inspection or safety deficiency has been noted, a non-conformance report is issued to document the identified deficiency and to track the corrective actions taken until the deficiency is resolved. The assessment concludes with the assignment of an appropriate interval for reinspection using the rate of deterioration that's been observed through these readings to calculate the remaining service life of the pressure-retaining item.
After, we calculate that remaining service life based on the most limiting thicknesses, and assign a reinspection interval that's equal to no greater than half of that remaining service life.
We use that interval for pressure vessels that are not fired, but for boilers and boiler-related equipment, we follow the NBIC guidelines for periodicity. And we have to do that for a couple of reasons. Number one is that we have very limited manpower. We have only identified about 1,320 pressure-retaining items that needed to be reviewed and assessed, and of those 1,320, only about 650 are still active. But I only have besides myself one commissioned inspector to do most of those inspections, and he's only matrixed to us part time. The rest of the time he's a Level 3 NDE person doing x-rays and other things, so I don't have his full availability. So every time this item would come up for reinspection, we would reinspect it, and in order to keep track of all of this information, I have put together an Access database that we use to record all the inspection data and the identification and other important pieces of information for each vessel.
So we take the information that's obtained during the inspections, we put down what the current status of the item is, the date of the current inspection, and the upcoming inspection due dates. And, yes, at the same time we also do a program for pressure relief valves. That program is still not fully developed, but it's developed enough that we have a reasonable assurance all the pressure relief valves that we have out there are properly operating and operating at their set points because of the way we test them. We do have our own testing laboratory at the lab.
We have the ability to do some minor set point adjustments as needed, but at the present time if anything is wrong with the valve, we either replace it or send it up for repair to a VR stamp holder. Some of the opportunities for improvement that we have identified and we are continuing to work on: Again, I just mentioned the tracking and documentation of overpressure protection devices. There are a lot of overpressure protection devices are not immediately related to a pressure vessel or a boiler.
Some of them are on piping systems, but we want to make sure we get them all. And while we feel pretty confident that we have identified about 90 percent of them and they have been tested and are being tracked, we know that there is probably another 10 percent that we don't know about yet.
We are trying to narrow the gap a bit. We are also in the process of developing a process -- a methodology for evaluating flow capacity so that we can make sure the flow capacity of the installed pressure relief device is adequate. As many of you know, in Section 8, Division 1, there are not really hard and fast rules on what kind of capacity you need for a pressure vessel pressure relief device, so it's been put into the purview of the user's responsibility to make that determination. We take that responsibility pretty seriously, and we are developing a method of dealing with it.