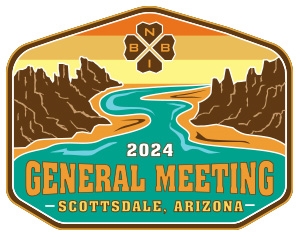
92nd General Meeting Presentation
Introduction of ASME Code Rules on Electrochemical Cell Stacks for Electrolysis
Kang Xu
The following remarks were delivered at the General Session of the 92nd General Meeting on May 13, 2024. It has been edited for content and phrasing.
INTRODUCTION: Kang Xu is a pressure vessel consultant and engineering fellow at Linde, Inc., and has been working in the industrial gas industry for more than 20 years in the areas of pressure vessels, structural integrity assessment, and materials behavior in high-pressure hydrogen. Xu, an ASME fellow, serves on several ASME committees and is leading the effort to incorporate code rules on electrochemical cell stacks into the Mandatory Appendix in ASME Section VIII. Xu earned a Ph.D. in materials engineering from the University of Maryland at College Park and has authored and co-authored 38 peer-reviewed technical papers and one book chapter.
His slide presentation can be found here.
MR. XU: I appreciate this opportunity to discuss the newly developed ASME code rules for electrochemical cell stacks for electrolysis.
First, I will briefly introduce the principles of water electrolysis. Then, I will go over some of the historical developments in electrolysis technologies. The primary focus will be the alkaline electrolyzers (AEL) and proton-exchange membrane electrolyzers (PEM). We'll discuss the ASME Section VIII Code scope and some relevant existing code rules. Then, I will give some details about the development of code case 3078, which is about the new ASME code rules on electrochemical cell stacks. Finally, I will summarize the presentation.
Water electrolysis is a chemical reaction that splits water molecules into hydrogen and oxygen. The hydrogen gas collects at the cathode side of the unit cell, and the oxygen gas collects on the anode side. Regardless of the technology used for this reaction, the total energy required is about 286 kilojoules per mole of water; 237 kilojoules must come from electricity, and the remaining 49 kilojoules are from heat. This amount of energy is the equivalent for a voltage of about 1.5 volts per unit.
Looking back to the historic electrolyzer development, we can see that the technology has been with us for more than 200 years. The first discovery of water electrolysis was reported to have been in 1789. Since then, the technology has experienced many milestones. For example, the first industrial production using alkaline electrolyzers was in 1888. The first large-scale commercial production using electrolyzers was in 1939. The first pressurized electrolyzers were developed in 1948. The PEM electrolyzers and Nafion-based PEM electrolyzers were developed in 1966. So now we are in the 21st century, and developing and utilizing water electrolysis again has become a priority.
The next couple of slides will give some examples of early electrolyzers. Alkaline technology started to come to market in the early 1900s. This slide shows an alkaline electrolyzer used in a diaphragm filter press technology developed in 1899. This unit has 44 cells and can produce about 66 cubic meters of hydrogen per day, which is about 14 pounds of hydrogen. At that time, believe it or not, the main application of hydrogen grew.
By the mid-1900s, the demand for hydrogen skyrocketed largely due to ammonia production, so large-scale commercial electrolyzers started to operate. Here, we have a 135-megawatt alkaline electrolyzer installed by Norsk Hydro in Norway in 1949. This unit is typically used to produce 28,000 cubic meters of hydrogen per hour, so the capacity is more than 10,000 times higher than that of the first generation of commercial electrolyzers.
Alkaline electrolysis has been the dominant technology for commercial electrolyzers for more than 100 years. Those types of electrolyzers typically operate over that pressure, which is driven by frequency. High-pressure electrolyzers or pressurized electrolyzers were developed in the mid-1900s. By the late 1900s, some advanced alkaline electrolyzers operated at fairly high pressure. Here are some photos and a sketch showing a cell stack inside a pressure vessel that can operate at pressure above 450 psi.
The current leading technology for commercial electrolyzers is PEM electrolyzers. This technology was developed based on the solid membrane electrolyte and was primarily used in the aerospace industry in the 1960s. It's used in the aerospace industry because it can be operated fairly efficiently at zero gravity.
Compared with alkaline electrolyzers, PEM electrolyzers have many advantages. For example, they have very high carbon density so that the efficiency can be very high. The hydrogen products have a very high purity and operate at a higher pressure, so the design is very compact.
Of course, PEM electrolyzers have some downsides; they cost more and are less durable. The picture here shows the structure of a single-cell PEM electrolyzer. In the middle is the membrane electrode, sandwiched between a porous structure for gas and liquid distribution. For the additional layers, we have the cell plate and bipolar plate with a gasket, which is really for electric insulation for the current distribution and the seals. The outermost part is the endplate, which provides support for the structure. And if you repeat this unit cell many times and put it together, you can make a much higher capacity PEM electrolyzer.
The cell stack for PEM electrolyzers can come with many different geometries, shapes, and dimensions. Here, we have a cylindrical shape and a rectangular shape of cell stacks. The supporting structure can be from a holding structure or a hydraulic frame. A large PEM cell stack can have hundreds of unit cells between the plates.
One concept is about the electrolyzer and PEM electrolyzer. The electrolyzer is a system that contains the electrochemical cell stacks of piping, storage tanks, power supply, hydrogen and oxygen separators, pumps, water purification, or some other functional components. In commercial products, those components typically are packaged into a container or a skid, but at the heart of this system are the electrochemical cell stacks highlighted in red. And that's really where this reaction started in the hydrogen regenerator.
Here, I'm using a 1-megawatt PEM stack to produce 200 cubic meters of hydrogen per hour, which is about 40 pounds per hour of hydrogen. The typical operating pressure is between 500 and 750 psi. The operating temperature is between 120 and 170 degrees Fahrenheit. In the design of the electrolyzers, sometimes we follow ISO 22734 or CSA B22734. Those are the standards that provide some general performance-based guidelines on electrolyzers, but by no means do they give the detailed design requirements.
In the European market, the pressurized electrolyzers are treated as pressure equipment. So, according to EU (European Union) regulations, they must comply with the PED (pressure equipment directive). And a CE marking is required.
However, in North America, there's some ambiguity regarding Authority Having Jurisdiction. Sometimes, a building code or a fire code is referenced for electrolyzers because they involve flammable products. Still, there's a general lack of understanding of the regulatory requirements for the Manufacturer and everybody involved in installing electrolyzers on-site. Because of their pressure nature, this type of equipment should be regulated as pressure vessels. That's the primary reason ASME Section VIII developed explicit code rules for electrochemical cell stacks for electrolysis.
Let's take a moment to review the code scope of ASME Section VIII Pressure Vessel Codes. As you know, the Section VIII Codes are the most adopted pressure vessel codes in jurisdictions in North America, and the code scope of Section VIII Division 1 is defined by exclusions. This means that a pressure container is a Section VIII pressure vessel unless it can be claimed as one of the 10 exclusions.
The first exclusion is vessels under other ASME Code sections. For example, a boiler is a Section I vessel, not a Section VIII vessel. Fired tube heaters, pump or compressor components, piping systems, or piping components are not Section VIII pressure vessels. That's pretty self-explanatory. Also, under certain conditions, vessels containing water and air are excluded from Section VIII code scope. The same goes for heated water tanks.
Section VIII currently excludes low-pressure vessels with pressure no greater than 15 psi or smaller vessels with internal dimensions less than 6 inches. The last exclusion is vessels for human occupancy, which are not Section VIII vessels.
As the 10 exclusions show, none can be claimed for pressurized electrolyzers unless they operate at low pressure or are small enough to meet the dimension exclusion limit. Therefore, in most cases, the pressurized electrolyzer cell stacks are within the ASME Section VIII Code scope. So, by current code definition, the pressurized electrolyzer cell stacks are considered as ASME Section VIII pressure vessels.
People are familiar with plate heat exchangers. The code rules for plate heat exchangers were developed not very long ago, I think it was 2017 when Section VIII Division 1 adopted Appendix 45 for plate heat exchangers. Mike Pischke (NBBI assistant executive director-administrative) gave an excellent presentation to introduce the code rules for plate exchangers at the General Meeting seven years ago. If you compare and look at the plate heat exchangers, the electrochemical cell stacks share many mechanical similarities.
For example, both have endplates, tie rods, gaskets, and layered structure. The code rules for electrochemical cell stacks were developed based on the code rules in Appendix 45 for plate heat exchangers.
The code case and the cell stacks have some specific considerations. The code case considers the code boundary for electrochemical cell stacks as metallic pressure-retaining parts, including the endplates, the bolting, and the nozzles. As highlighted in the sketch, these are the right components.
Those metallic materials must comply with the ASME material requirements, and the code case also recognizes that nonmetallic materials are essential for electrolysis. Those materials are selected based on their electrical and electrochemical properties. Those components include the dielectric plates, membrane, and some other internals, which are highlighted in blue in this schematic. The nonmetallic materials are exempt in this code case from the code requirements as long as they meet ISO 22734 or ANSI/CSA B22734 type testing requirements.
From design considerations, I repeat maximum allowable water pressure is determined from the endplate, bolting, and nozzles, similar to PHE in Appendix 45. The proof test or design calculations for cell packs are not required, also similar to the plate heat exchangers in Appendix 45.
The structure integrity of the cell stacks is actually guaranteed by the pressure test requirement at 1.5XMAWP for two minutes. This requirement is consistent with type test requirements in the ISO or CSA standards. But the code case goes one step further. It requires the pressure test is mandatory for every production unit. Where this ISO standard and/or CSA standard require type tests only for the type qualification, not for the production units, the Authorized Inspector must also witness the pressure test, as with all other ASME pressure vessels, unless they use mass-produced requirements.
The code case also requires overpressure protection in accordance with ASME Section XIII. It requires certification using Manufacturers Data Report U-1E/U-3E, and compliance with ISO or ANSI/CSA requirements is mandatory. Those are clearly spelled out in the code case.
Here's a snapshot of the approved code case. The code case was approved in September last year and is currently available for code use. The code case provides the Manufacturers Data Report. With the published code case, I'm hoping this provides clarity on the Authority Having Jurisdiction, and it will be easier for users to specify the lack of a product; it will be easier for Manufacturers to comply with the ASME code; and it will be easier for jurisdictions to accept the product in accordance with their local pressure vessel regulations. The task group in Section VIII was set up with the objective of incorporating the code case as a mandatory appendix.
I want to summarize as follows:
- Based on the current code scope, the electrochemical cell stacks for electrolysis are considered ASME Section VIII Division 1 pressure vessels.
- Code case 3078 is developed based on existing code rules for plate heat exchangers, with considerations of special materials and processes used in water electrolysis.
- The code case provides code rules on the design and construction of ASME code-compliant electrochemical cell stacks.
- The code case provides a path for ECS Manufacturers to comply with the jurisdictions' requirements for pressure vessels.
- I'm hoping the code cases will be incorporated as a mandatory appendix in Section VIII Division 1 and in the coming 2027 code edition.
Thank you very much.
I have a couple more minutes to answer any questions.
MEMBER: Is there any dominant failure mechanism for these stacks? If you've seen anything, what were they?
MR. XU: I don't think I'm the expert to speak about that, but it's like pressurized equipment. If you have a mix of hydrogen and oxygen, it creates a potential explosion condition – I guess that must also be considered in the process.
MEMBER: You mentioned some pretty high pressures. I think it was 30,000 psi.
MR. XU: No. In the example I gave, the typical opening pressure is between 500 and 700 psi. I've also seen somewhere around 1,000 psi.
MEMBER: I was concerned they would have stamped relief valves for this.
MR. XU: The No. 1 question is that this industry just started to come to primary commercial applications. There are some concepts about what to do with this vessel as a pressure-containing part. Looking at ASME Section VIII Code scope, it obviously falls in the code scope of Section VIII, so it's a pressure vessel. Then the question is: What code rules do we need to follow to design those types of equipment? The plate heat exchangers give us some precedence on how to handle this type of equipment. This is where we are. We’re trying to use the technology to learn from the heat exchanger to implement this into the plate and the electrochemical cell stacks.
MEMBER: If I understand correctly, your position is that all these vessels should be code-built even if they don't exceed the 6-inch criteria. Is that an accurate statement?
MR. XU: No. If they are below 15 psi or below 6 inches, at least they have the option to do something else, but if the size or pressure exceeds the limits, then it also falls in the Section VIII code scope.
MEMBER: Do you feel like the code's scope is the definitive standard for where a safety concern comes into play? If it exceeds 6 inches, you feel like there's a safety threat. And if it's less than 6 inches, you feel there's no safety threat. Is that accurate?
MR. XU: No, this is not what I'm saying. This is not really specific to electrolyzers. It's specific to every ASME code vessel, code vessel that's existing, and existing code rules in the code book. It has nothing to do with the electrolyzers and what I'm discussing.
MEMBER: Do you feel like it needs a follow-up inservice inspection in addition to an insulation inspection, or do you feel like this vessel needs to be built to code? If so, it's good to go from that day forward?
MR. XU: Well, that's the minimum. It needs to be built to the code and be code stamped. This is a new technology. A lot of new Manufacturers have started getting into this business. If this lacks monitoring or regulations, then I feel we don't have sufficient standards to guarantee the safety of this equipment. I cannot speak about the inspection requirement.
MEMBER: First, I would like to thank the working group ASME led by Dr. Xu, who developed it in a short period of time. I think that we need to understand one thing. Some new technologies are developing much faster, and as jurisdictions, we need to find a way to adopt them quicker. I had the chance to talk numerous times with Dr. Xu about this. We have a case where people are trying to register those designs, but there are no fabricators; bits and pieces are coming from all over the world and will be disassembled. There's no one company taking responsibility for that. We should be aware of these practices.
Recently, I attended a Canadian hydrogen conference, and there were three Manufacturers there. I asked them how they designed the pressure vessel. They said this was not a pressure vessel; it's an electrolyzer. It's just something that we should be aware of.
MEMBER: For most Section VIII vessels, the interpretation says if the inside chamber is less than 6 inches, it meets the exemption rule, but since most plate heat exchangers don't fall within that, it's not going to fall within that standard either, that interpretation. Are there other cells or cell stacks that do fall within that exemption?
MR. XU: To my knowledge, most cell stacks fall into the dimension of 6 inches. When you look at the dimensions, you control the pressure design. You cannot take those internal channels into consideration. Those dimensions do not dictate the pressure vessel design.
MEMBER: Your interpretation in Section VIII says you do take those into consideration?
MR. XU: I think that's how you get to the details about the code rules, but to my knowledge, most of the electrolyzer products that the dimensions, like the pictures I show, like this, the dimensions that control the pressure design were 6 inches.
MEMBER: Are they typically U or U-1 stamped?
MR. XU: I think the industry has come to realize this is a vessel, and they are participating in ASME activities. That's how I'm hoping to bring this awareness to this community. Those types of equipment should comprise code rules for East and North American markets and be code stamped. The jurisdiction has standard rules and is currently enforcing the standard requirements in the pressure vessel regulations, so they should be code-stamped.