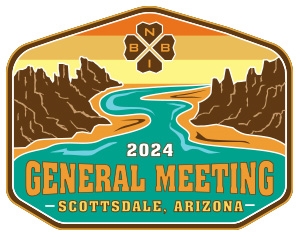
92nd General Meeting Presentation
Facts and Myths About Pressure Testing
Mark Lower
The following remarks were delivered at the General Session of the 92nd General Meeting on May 13, 2024. It has been edited for content and phrasing.
INTRODUCTION: For over 30 years, Mark Lower has worked in operations and energy-related R&D, with more than 20 years of experience with ASME Code in design, analysis, and fabrication of pressure equipment. He is a program manager at Oak Ridge National Laboratory. He also has performed accident investigations for the US Department of Transportation Pipeline and Hazardous Materials Safety Administration and authored several papers on pressure safety. Lower serves as the vice chair of the BPV VIII Standards Committee and is a member of other Section VIII committees. He is a National Board Advisory Committee member representing boiler and pressure vessel users. He also earned a Ph.D. in mechanical engineering from the University of Tennessee and is an ASME Fellow.
His slide presentation can be found here.
MR. LOWER: This was a bit of a daunting task, knowing most of you have more experience with pressure testing than I do, so let's see where this goes.
My first experience with pressure testing was sitting for hours in an old, dilapidated school bus, doing pressure testing on pipelines. Sitting and watching pressure tests is not overly exciting. And in pressure testing, the language isn't all that difficult. We all know a lot of the terms. It's a fairly simple process.
Let’s do a group participation exercise. And I know you're participating because I can see your lips move when you read the questions. Pressure testing, in general, is not all that difficult. As our wonderful executive director (Joel Amato) would say, "This isn't rocket surgery."
I've got five questions. The first question: Pressure testing is performed, and pressure testing is required for which of the following reasons? Pick all that apply. Looking through the list, can you tell which ones apply specifically to pressure vessels and boilers?
Leakage, first, is not allowed during the required visual inspection, so let's check off that. That's kind of a fact, right? Except what we always say is we have these exceptions. This isn't necessarily intended to be a gray area, but leakage might occur in temporary closures, and if you have some nozzles where we're going to roll piping on, we say those can leak, also. We certainly don't want to leak where we're going to have an opportunity to mask other leaks. We do have some exemptions, but overall, that one is kind of a fact. We do want to verify leakage during our pressure test.
Verify gross structural integrity. The intent of a pressure test is also to increase our maximum pressure more than it would ever see in service. This isn't always the case. Typically, there are some other perturbations here, but our intent is that the pressure test would be more than at any time this vessel is in service. So, hopefully, we will see gross structural defects.
We won't be able to identify minor fabrication defects, for instance. Certainly, this doesn't tell us anything about our fatigue and the issues associated with it. Those cycles take time to grow defects in material toughness problems. Typically, in many codes, we have requirements to keep you from enjoying some of the material toughness problems.
There have been some failures during hybrid tests. Usually, those are due to colder temperatures, so we have some rules. We won't be able to tell much of the material toughness issues during a pressure test. This is more of a gross-type application to make sure we don't have gross structural defects. So, again, another fact.
Verify the burst capacity of a component. I have been asked several times by people who come in with a vessel, throw it down, and say, "I don't have a design for this. Can I just pressure test it and use it?" What's the answer? I have no idea what the maximum operating pressure is supposed to be, and until we do a little investigation, I don't know what materials you're using. I don't have any idea what this is supposed to be. On a number of standards, we do have prescriptive requirements, certainly in some cases performance requirements, on what we need to do for burst capacity or determining what the allowable maximum pressure would be, but simply doing a pressure test isn't going to tell us that information.
From my vantage point, I'm not seeing those burst tests used nearly as much as they used to be. FEA (finite element analysis) has become quite popular, so we can do a lot of FEA assessments and ensure that we can look at the maximum operating pressure. But we're going to use a pressure test to determine our maximum operating pressure. It's not intended for that, so that's a no.
The pressure test also is not intended to blunt cracks. However, it is true that if we can blunt cracks, our material toughness does improve. This is the phenomenon: We apply a big enough stress that if we do have a sharp crack, we can blunt that crack and our toughness improves. The problem is that crack tip blunting only occurs when the stress is high enough to produce plastic deformation.
Many stresses usually are based on the specified minimum yield strength. And if we get material hardening, it is not considered when developing our allowable pressures. Typically, we're not getting anywhere close enough to blunt that crack. We will talk more about that in a little bit. The pressure test is not intended to help material toughness problems. Some of the literature actually lists that a pressure test will help with material properties. And it's not really true.
Verify the pressure-retaining capacity of all components. We just discussed leakage. I think the intent is that we want to verify the pressure-retaining capacity, but especially ASME, we always have exceptions. So again, we have quite a list of exceptions. One reason is that we don't want to do a pressure test every time we change a gasket or bolts, so it's not really intended for that. It's kind of why it's exempt from that.
Is everybody still at 100 percent? Or at least we'll play it that way.
Some of the conclusions we just discussed have different minimum hydrostatic test pressures and minimum pneumatic test pressures that are different, depending on which code and which edition you use. They have changed over time. So, if we really are trying to blunt cracks, that's going to be more consistent. If we are trying to have a methodology to develop burst pressures based on the pressure test, those will be a little more consistent, but they're just not.
So next, codes and standards allow any pressure test at the user's discretion?
Yeah, that's definitely false, and I've been pushed for that, too. Well, we don't want to do hydro tests. The codes make specific allowances for when pneumatic tests can be allowed. In some cases, even throughout the industry, I've seen that the regulators have tried to force companies to do another type of test. And one of them specifically tried to get them to fill some aluminum heat exchangers full of water. That's a bit of a problem trying to get the water back out. When you get these aluminum heat exchangers, you know they're not well supported because you want that thin material. So, the company did push back. We got it all sorted out, but the code has some specific guidance.
Also, a leak test is only acceptable if agreement is reached between the Manufacturer and inspector. And I wasn't sure which one to use here as far as the Manufacturer goes. If you have a stamp holder, it's a big M. If not, it's a little M. But if we're using piping, it's not a stamp holder, so back and forth. Regardless, we want some kind of inspector involvement here to make sure what we're looking at from a pressure test perspective, all those things we just talked about in question one, we're also looking at that process. We are still making sure we're looking at gross defects. We're still making sure we have leak-tight integrity.
In some cases, we had hydrogen lines in a reactor. We're looking at those kinds of applications. Hydrogen in a reactor environment with fire protection codes was a big deal. Leak tightness is a big deal, but we don't want to have a pneumatic test. We're not going to use water in the hydrogen lines because it was coal hydrogen, so we didn't want to use water. We didn't want to fill them with air. What are our options? We did go through a bit of a process. In some cases, a leak test is allowed, but there are limited applications for that.
Number three: There is no difference in a pressure test performed as a requirement for initial construction and those performed for post-construction integrity management?
Highlighting some key words there with initial construction and post-construction integrity management. And I'll say this is a bit of a trick question just to make it interesting at the end of the day. Let me explain a little bit. There are several post-construction standards, and the NBIC is one. We talked about ASME PCC-2 quite a bit, and we've also referred to API quite often. There's some general guidance in ASME PCC-2.
One of the bigger ones that is interesting is the inservice test pressures specified according to the original code of construction. I think this is helpful, and we will talk about that.
The test pressure should be at least 77% of the piping test pressure. It's interesting when you have piping, pressure vessels, and other components all linked together. If you look at that first bullet, pressure testing of a piping system through equipment is not recommended. And I've seen like gate valves, for instance. Hydro tests tend to be very rough on gate valves, and sometimes the gate valve has to be replaced. If possible, we want to isolate a number of components and isolate that system.
Remember that for pressure vessel or boiler construction, specifically, once the boiler or pressure vessel is stamped by the Manufacturer and comes out of their shop and gets put into place, it's already post-construction even though it's never started up. So, it’s a slightly different application here.
You may be invoking post-construction standards on something new that's never been in service. Most, if not at all, post-construction standards say that the resulting stress due to pressure should be limited to 100% SMYS (specified minimum yield strength). None of them want to take credit for you getting over that minimum yield strength. You deform it; it's yours. They don't want to take the warranty on that, I assume.
I think this is a pretty interesting little figure for components. It talks about how the pressure tests should not exceed the maximum stress limits of the original code of construction for each component. This is a neat little ASME figure. And sometimes the figures and the pictures help me in my mind. Dark green is the design stress limit allowed by construction codes. The red part, that curved line, is essentially the yield line. When you crossover, you're past the yield point of that material. Codes don't want you to go into the red part. They want you to stay in that dark green part for normal operation. And then we got this light green part that allows you to go there, but on very limited applications and circumstances.
Let’s talk through that. I also want to note that my background is in pressure testing with pipelines. Elevation changes are a big deal. If you've got 100 miles of pipeline and significant elevation changes, you can have significant differences in pressure due to the elevation changes. If you're not isolating that line, you might have one spot showing very low points and a significant pressure increase over something (high).
This might also come into play if you have something running through a shop where piping runs through a high place, and you have pressure to the top and then all the head pressure for the piping that runs throughout the plant. You need to consider how you look at those components in that elevation change throughout that process. When you're looking at what that other figure looks like, make sure that we're not getting into the yield space for that equipment.
This was the picture I just showed you. It's out of Section VIII Division 2 because I think it shows it better, but as I mentioned before, we have this green space. This is where we want you to operate. This is the allowable stress for that particular standard. And then we've got that big, arching dark curve. That's our yield point.
We have this other section here, this light green part that's called occasional loading. The codes don't want you to operate in this area, and they put limits on it to keep you away from the yield point. So that's where we're at for our pressure test. We've had some questions: Should I design my vessel based on what I need to do for my test pressures? The answer is no. As you can see, we still have limits to keep this within the safe realm. However, there are limits, too, based on the pneumatic and hydrostatic test pressures.
The yellow is where we're not into yielding, but the code still doesn't want you to go. We want to stay away from that yellow or cautionary area. And then, we want to stay out of the red. It talks about pressure components greater than 1.0, which is up in the red. You can see yielding, and this is Section VIII Division 2. Section VIII Division 1 for pressure vessels says if it doesn't have these same limits. It just says if you have distortion, you have a problem. Well, by then, it's too late, right? We've already exceeded that. I'm going to go back. Any intermediate value between the minimum test pressure and the maximum stress may be used.
When you're looking at elevation changes and different codes in materials, the point is, can we keep our test pressure within that light green area for all those components? That's certainly a band that we can stay within.
So, getting into a bit of the integrity management point, come up with the spike hydrostatic test. Requiring new construction minimum test pressures may not result in the best assessment. If you have some local thin areas, more than likely, if you're going up to the minimum test pressure, you're not going to notice those local thin areas are there.
The concept of increasing your test pressure a little bit above the minimum yield to check to see if it's OK, but for a very short hold time will often render better confidence in that you have a pipeline with fewer defects.
Of course, we're now in a situation where this needs to be controlled. We need to look specifically at our equipment and what we've got. What defect size are we looking for, and what pressures are we looking at? So, to me, this is kind of a very engineered type of application, but it certainly gives a lot better confidence.
The problem is that in some cases with specific defects, we can get something known as pressure reversals. As I mentioned, we could blunt cracks, in some cases, in older pipelines where we might have some sharp cracks on the outside. If you'd see some of these older pipelines that have been there since the '50s and '60s, that have been buried underground, that the cathodic protection has been gone for many years, the outside of that pipe with no coating looks horrible or it's tar, and the tar has come off.
You've got these outside defects going way up above the yield strength, creating this pressure reversal. Now, when we get our pressure test at 100 psi, for instance, the next time we pressurize it, it might fail at 95 psi. This is very prevalent in ERW (electric resistance welded) pipe seams. Of course, ERW has improved over the years, but it wasn't a very good method in the '50s and '60s. Typically, that shows as a bulge or a local indication. It's not usually a catastrophic failure, but it is interesting when you do this kind of test and all of a sudden, nozzles won't line up or you go to put a gate valve back in place, and now you can't get them back in place.
You took some data during this test, and most pressure reversals were fairly small. If it failed at 100 psi once, it might be in the 90 to 95 psi range. But there were some high statistics. Just looking at some of the data, my guess is they didn't look at their pipe very closely. In a lot of cases, you have a very corroded pipe; now you're trying to have these very high spike pressures and you've got these big failures.
Overall, I'd say we just have better technology today for pressure testing for pipeline integrity or other integrity management techniques. I don't know that I would use a pressure test to verify integrity management on a regular basis. There's a lot of downsides, and we just have a lot better ways of doing that. Some of these AI tools check multiple thousands of points in a very short time, so there's just better technology today.
The last two questions are fairly short.
Question four: Hydrostatic, pneumatic, and sensitive leak tests are all forms of leak test?
That answer is true. Everything leaks. In fact, PCC 2 gives examples of leak testing, including bubble testing, pneumatic testing, and hydrostatic testing.
Several factors go into leak testing and making it leak. One of the ways you can adjust that is through hold times. ASME has looked at hold times in the past, but with all the different factors involved – Section VIII goes from a very thin material, 1/16 of an inch, and some construct vessels up to 4 or 5 inches thick.
How do you design or come up with a hold time for equipment that spans that much and feel good about what you're doing when that hold time actually shows something? So far, we've been very reluctant to do so.
And the last question: Pressure testing is not hazardous if codes and standards requirements and guidance are followed?
This is relatively obvious, right? The answer is obviously false. Most of the hazards are associated with the sudden release of energy. It amazes me sometimes how you do a hydrostatic test, certainly pneumatic. We're doing it to code, and they've got people working very close by. I even got a video of some workers on a tank painting a handrailing while they're hydrostatically testing this tank. That doesn't make sense.
In fact, we've had a couple of accidents involving small piping and tubing with a person working in the area. Luckily, nothing happened, but it ought to scare all of us to see some of the miscalculations that go on with hazards that are right there in front of them, and they just don't see them as hazards. Doing it strictly to codes and standards doesn't remove those hazards.
There are several hazard considerations, with system volume being one of the big ones. Pressure is another, but system volume is a big deal. When you're looking at small vessels, maybe that's not a problem. But when you're looking at very large systems, there can be a lot of stored energy in that system. Also, proximity to other people and how we address our hazard mitigation and barriers is also a big deal.
This one is a hydrostatic test failure that we don't necessarily think of because water is not compressible. But the hydrostatic test; it's an incompressible fluid, but we still have the strain energy of all that material. If you have a large volume – especially if you have something like a pipeline where it's spread out quite long – you've got the strain energy of all that material. And when something does release, there's a lot of energy there.
Pneumatic, we all understand that we have a lot of energy that has to be released through that compressed gas, but then also through that strain energy of the materials as well.
This is the hydrostatic test. It took me by surprise, and I was glad to see he was back out of the way because it certainly didn't appear that he was expecting it. I'm thankful I’ve never witnessed a failure during a pressure test. Hopefully, I never do. It can be quite catastrophic, whether pneumatic or hydrostatic. The point is to keep people away, and it doesn't take much of an opening to release a lot of energy in these circumstances.
Thank you very much.