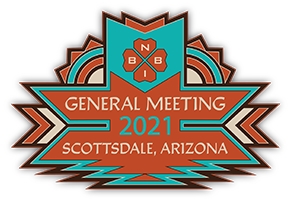
89th General Meeting Speaker Presentation
"Additive Manufacturing: Code Implications of Making Components from Weld Metal"
Teresa Melfi
The following presentation was delivered at the 89th General Meeting Monday General Session, May 10, 2021. It has been edited for content and phrasing.
INTRODUCTION: Teresa Melfi is a technical fellow at The Lincoln Electric Company, where she has been employed since 1982. Throughout her four decades in the industry, Melfi has had roles in operations, research and development, and international engineering. An active member of the global welding community, she holds more than 50 US and international welding-related patents. Melfi is the newest member of the National Board Advisory Committee, representing the welding industry.
Ms. Melfi’s slide presentation can be accessed HERE. Videos from Ms. Melfi’s presentation can be accessed HERE.
MS. MELFI: You will see the title of my presentation is Code Implications of Making Components from Weld Metal. And the very first line you will be able to see is in gray. And that first line is “Additive Manufacturing,” because I am never quite sure whether I am talking about something that's new or something that is old. If you look on the screen, you will see a picture up there, and it's a little bit hard to see, but this is a patent that was filed. It was granted in 1925, but it was actually filed in 1920. So additive manufacturing using weld metal is over 100 years old.
So, what's all the hype about? Additive manufacturing: is it something new, or is it not something new? When we talk about additive manufacturing, you hear words like 3D printing, and you think about those little components, little gears that come out of the machine looking exactly like a gear. What we are talking about is 3D printing, but a subset of 3D printing that's called directed energy deposition, and a subset of directed energy deposition that's called wire arc additive manufacturing, and even a subset of that that's called gas metal arc additive manufacturing. About 98% of the additive manufacturing done today in the welding world is done with gas metal arc welding (GMAW).
So, that's additive manufacturing. Those are all the cool, trendy words that you use if you want to sound cool and trendy. But if you are a welder like me – you talk about welding – you talk about weld metal and shape welding. Weld metal buildup has been around since the 1970s. There is a little bit of hot wire laser and a little bit of EB welding that's done this way, but mainly this is just good old-fashioned gas metal arc welding.
You start with a 3D print. This is a hollow-bladed propeller and the inside part – what you see in green is a different material than what you see in red. This is the part as printed. And you can imagine a hollow-bladed propeller would be really difficult to make any other way. Now you see it final machined and you will notice that shape is kind of different than what you are thinking about when you think about additive manufacturing. In the welding world, if we don't take one to two millimeters off every surface, it's unusual. So, what comes out is near net shape, but barely near net shape.
And you will see it's a six-axis robot. We manipulate the robots and the parts so that you are welding always in the most desirable positions, so that defects are minimized. Everything is done in a very controlled way with this type of weld metal build-up. You will see finishing off the propeller here, and this is fairly real time. It's not a really fast process, but robots don't get tired. They operate 24-7. We bring in the wire in one-ton packages, so it doesn't run out. And this is the type of result that you see.
So why are people doing this? The main benefits are a shorter lead time and some design flexibility, like what you saw with that hollow-bladed propeller. You get prototypes very quickly this way. And sometimes you will do multiple prototypes, where in the past you would be limited to one or two. So, it really speeds up the development process for different parts and components.
One of the things I think that's especially important today is mitigating the supply chain risk, because it's always so difficult to try to find suppliers that can handle things and can handle things quickly. And if there is a problem bringing ships in from China, you have a problem.
And finally, the green aspect. If you think about additive manufacturing as an additive process, and you think about machining as a subtractive process, the weld metal additive is somewhere in between. There is certainly a lot less waste than machining a big block of steel, but it's near net shape, it's not net shape. So there definitely is some material savings that come along with it.
When I talked about the different places people would use it, reducing cycle time is typically used for these large castings. So, by the time you put a casting together and you pour it, it takes a long time, and it just slows everything down in a development process.
The next thing that you see, where it says reduced material waste, this was a component that just required so much machining. It was easier to build something that looked kind of like what you wanted to end up with and then just do a little bit of machining on it.
We are finding a lot of people are using this for places where there is a really high tooling cost, because they can make these very complex tools and then just machine off a little bit from them.
Probably my favorite place to use it is to simplify joining. We ask our welders to go out there and join things in ways that no welder should have to join things. You have to be so skilled to get in there and make some of the welds that our designers force you to make, where what we can do here is make nodes and things like that that move the welds out to places that are lower stress or easier to get to.
And finally, it's the enhanced performance, going back to the hollow-propeller design again. Lightweight components, modifying shapes in ways that you can't do normally, putting integrated cooling columns in. It just gives the designer a lot more flexibility if they design with weld metal rather than a chunk of steel.
This example is a locomotive front end. And you will find that most of my examples are not from the boiler or pressure vessel industry because this is not well accepted in the industry yet. This was a locomotive where they wanted to make an integrated front end, but there is always a little bit of design iteration that comes along with it. Because you don't want to just build what you had before, you want to build something better. You want to see a few design iterations and figure out what works for you, so they compared doing it two different ways. They compared it doing the normal casting and that was a lead time of 10 months. The other way was putting together a 3D model on CAD, just giving a 3D-CAD print, and printing it out of weld metal. And you can see that the design time was about six weeks. So, they were able to play around a little bit to come up with a better design because they had four chances rather than one and came up with something a little bit better. I talked about additive manufacturing from weld metal. This one here is about a one-ton component.
When we are thinking about weld metal and additive manufacturing, a basketball would probably be the smallest thing we would even consider doing. Typically, these things are five to ten feet in any one direction and weigh many hundreds to thousands of pounds. These are big things, because again we are not doing net shape stuff. We are doing kind of near net shape and a little bit of machining.
Another place where we are finding that people want to use us is to replace obsolete parts. You think about companies like Caterpillar and John Deere who have to keep all kinds of stuff on hand so that when there is a breakdown, they can have it ready to ship out, because if you are a miner, and you have your frontend loader down, that's not a pretty thing. So, what they are doing is making sure that they have good 3D prints of these, putting them on the shelves and building them real time as they get orders. And they can generally do a turn-around in about three days, so it's not pie in the sky anymore. These things are being done, and there is a lot of examples of that out there. The one you see on the screen happens to be one that was in our manufacturing plant. A piece of equipment went down, and we couldn't get our machinists or any machinists to give us a reasonable quote, so we took an old 2D blueprint, turned it into a 3D drawing, and three days later we had a part to put back in the machine.
The other cool thing is you can make these from all sorts of metal. You can make them with phosphor bronze, you can make them with stainless, you can make them with high strength metals. And we have been welding this stuff for so long, we know what the properties are going to be like. We know what the tensile strength is going to be, we know what kind of residual stresses you will see and whether you need to post weld heat treat it.
Castings and valve designs – I didn't know that much about valve design before, but I'm learning a whole lot about valve design because that seems to be a big deal, that people have used the same valve design because it's just so difficult to change out these castings. Well, when they find they have got a quick way to change out castings and pull things together, they are starting to do some very clever things with their valves. This one here was printed, and then the flanges were welded on, but more recently we are seeing a lot of them that are being printed with the flanges as part of the valve design.
This one is one you can think about next time you get on an airplane. This is for the carbon fiber sheets that form the complex parts. And they were having problems because if they used forgings, first they had to take a lot of metal out of them, and they would have slight defects in the surface. And when you are trying to pull a vacuum and pull a carbon fiber sheet down, you need that to be perfectly smooth. They found building this up with weld metal and then machining it gave you a smooth mold to form in that vacuum.
And on the far side of the slide, you will see that the substructure for it is built from weld metal as well, and that's just not machined because it doesn't touch the carbon fiber. That one there is well over twice as tall as I am, and this one weighed about a ton-and-a-half. This is not atypical for the sizes we are talking about.
There were some structural designers in the seismic industry that were worried about the connections, so they would have a column, and they would have to make another box beam connection or an I-beam connection or connect a pipe to it, and they were having some real issues when they did their FMEAs on those points there. They decided to build up these connections right on there, so it was integral with that, and then the connection could be made a little bit further away from the stress point, and it would be an easier weld to make. In many cases, like the box column might just fit right in there, and then you just have a real simple weld rather than having to worry about fit-up and things like that.
This is one of my favorites, only because in my welding life I have looked at so many of these in failure. It's just a tough thing. If you look at the picture of the offshore structure there, you will see the circles at the bottom. That's what we call a TKY joint, and it's pictured up here. It's very hard for a welder to get to, and it's a difficult weld to make. We even test out our new consumables on these joints because they are so difficult to make. You have very complex welds, they are blind welds, they are right where all the stresses are. They are the worst thing you can possibly have. These are sitting out in the middle of the ocean. They are being buffeted by waves all the time, so fatigue is a huge factor.
We started looking at those and got a couple people from the Ohio State (University) Center for Design and Manufacturing Excellence to come in and do some redesigns. What they came up with was this crazy looking thing. All the connections are at the same point that you would see the connections on the left, but it's optimized for weight and fatigue resistance, and it really gives you a very simple weld. You can see the robot next to it, so it gives you an idea of the size. I think this was about 3-feet by 3-feet by 2-feet. Not a huge structure but you can do simpler things.
You can take piping systems, and you can create these nodes to help you out, and you can put gussets in the nodes. You can have your intersections perfectly integrated. You can see from the picture there that the welding was done in one direction, then a different direction, and then a third direction. And when you can manipulate both the part and the robot, you are really welding in space, and so it's very easy to create this kind of thing.
Casting conversions, that's probably the number one thing that we are seeing these days. The material cost is about the same, but there is a lot less labor when the robot is doing it. But more than that, the lead time is so much shorter, and the design flexibility is there, so if you want to make a change, you can make a change.
So, what's the big deal? You know, we have been doing this a long time. In the '70s during the heyday of the nuke plants, it was really hard to get castings and forgings. And, I knew of nozzles, I knew of manways and things that were built up from weld metal, and recently we had a group that sent out feelers, looking at just how many of these are out there and how long have they been in service and have there been any issues with them.
And I was very surprised especially in Europe to see how much of this had been done to the point that when they couldn't get some of these massive blocks that they needed to machine, for example, a nozzle out of, they would actually use submerged arc welding, and they would build these massive hunks of steel, and they would machine the things out of them. So, these have been in service since the '70s. When I asked the fabricators, who made these and how did they do it, they always kind of hang their heads down and look a little bit sheepish and grin because there aren't good rules for it.
The only way you can really do it is to consider it a weld build-up per ASME Boiler and Pressure Vessel Code Section IX rules. It's a little bit shaky as far as I am concerned, but that's how they have done them, and it's been working out OK so far.
The boiler and pressure vessel codes don't tell you how to make a casting. They don't tell you where your risers must be. They don't tell you how to get to the chemical composition you want. So why do we need rules here? Why do we need to tell people how to make these weld build-ups?
Section IX has been around for a long time, and we have a lot of experience. We went around to a lot of different manufacturers of these different parts that I have been showing you, and they said it's not onerous for us to go in and do these qualifications. So, we started writing rules. Section IX said we understand these materials, we understand what the weld metal is like, and there was a lot of pressure from industry for Section IX to write some rules that were very specific to additive manufacturing.
Most of that pressure came from outside the boiler and pressure vessel community. Section IX is the most widely used welding standard in the world, and so we were getting things from Europe, from API, from all different groups to get some rules in there so that they could show their customers that they were doing these additive builds in a very responsible, conservative way.
And there is a lot of data out there for GMAWs, so the first code case was written exclusive to GMAW. It was sent out for a ballot with review and comment to all the construction codes. So, Section I, Section VIII, Section III, B-31, everybody got to comment on this ballot. And I was the project manager on this, and I was nervous because I thought I would come back beaten and bloodied. It was going out to so many people. But people were eager for some rules because they could see in their industry where there was a real benefit. And we feel like right now we are being pushed.
Normally I consider code years to be kind of like dog years: if you can get something to happen in 12 years, you are in pretty good shape. But this is just flying along, so we already have a code case approved. Section III says that they want to see this in the next publication of the code, so we are going to have rules and code in 2023.
The rules that were set up are set up in much the same way that highly critical welds in other industries are done, so the bridge codes or the seismic construction codes require that you qualify at the highest heat input and inner pass temperatures. So, the slowest cooling rate and the fastest cooling rate, and then you can only weld between those two.
And because from what you saw in some of those examples, you sometimes had very thin and thick sections in the same part. We also require qualification of the thinnest and the thickest. Essentially you are building this box, and once you qualify, you can weld anywhere within that box.
Tension impact, composition, bend test, just the normal Section IX stuff.
We know GMAW weld metal well enough, so we know what the worst-case testing direction is, and we require all testing that way.
And other than that, the balanced rules are pretty much what you are used to in Section IX.
So, the parts can be made, but they can't be used, because it's just a Section IX code case. It just says how to build them. So now the other sections, Section VIII, Section I, Section III, B-31, they have to figure out what to do with this and how to bring this into their code, how to give the rules so the designers can actually design with this sort of thing.
We know castings pretty well. Weld metal should be able to replace a casting, it should be pretty straightforward. But we are seeing also that there is a big call out there for some of those piping nodes in the B-31 world and some of the large forgings to be replaced. Nothing is off the table right now.
So, what about inservice repairs, what do we do? Well, the components are clearly weldable, but what kind of paperwork goes along with it? We don't have ASTM specs for these, so everything is new, and we are sorting through these things but doing it real time, because we recognize that if we don't have rules there, we are still going to have this stuff in construction.
We might as well set the rules and make them reasonable enough that people will follow those instead of continuing to use these old weld build-up rules. I am here for two reasons: I'm here to tell you what is out there and what's coming and how quickly it's coming, but the other half is I really would like to get some feedback on this. Are we crazy? Are we moving too fast? What would make you comfortable? What would you want to see so that you could do the inservice repairs or the inspections? What sort of paperwork should go along with this? Is this something that you are eager to see or something you are nervous to see? I am really interested to hear if you have comments, suggestions, things we need to look at.
Thank you. I would open the floor for some discussion.
MR. JEFFREY OLIVER: Why gas metal and not flux-core?
MS. MELFI: So, I guess flux-core could be used, but because these are automated, it's really nice to not have to deal with slag. So, we typically use gas metal, sometimes gas tungsten arc, but usually just bare wire.
MR. OLIVER: Is that the reason for gas metal to come on first because of the code case and surely for the waste products and the ease of which there is less mess?
MS. MELFI: Exactly, yes.
MR. OLIVER: But, flux-core and gas tungsten can be used as well?
MS. MELFI: Yes. The code case currently is written for gas metal arc welding, and gas metal arc welding encompasses flux-core. So, if somebody wanted to use it, they could. It just makes it a little bit messier from a robotics standpoint. Because you want to be able to operate six or eight or 10 of these cells with one person.
MR. OLIVER: Isn't the metallurgy a little bit different for flux-core versus gas metal and gas tungsten?
MS. MELFI: Yes. Flex-core, depending on the slag system that is there, you will get different properties, and so you can't indiscriminately substitute one for the other. But if you were to do your weld box, your high cooling rate, low cooling rate with flux-core, you could expect to get properties that are within that. And that's kind of what they do in the seismic industry today with flux-core.
MR. OLIVER: Have these products been out long enough to prove longevity?
MS. MELFI: The ones that I am aware of that have been out there the longest have been out since the '70s. So, are they in real critical places? A lot of them are nozzles, manways, the current AP-1000 design using weld metal build-ups. So, they are out there. We just don't know that they are out there. I got something recently about a pressurizer that was done this way, and I was shocked. But it sounds like there is more out there, certainly more than I know of.
MR. OLIVER: API has accepted weld metal build-up fabrication parts?
MS. MELFI: API accepts anything that is qualified to Section IX. So, it does accept them. It just doesn't know that it accepts them. So now API is -- actually, I am sitting on a committee, they are writing some new code rules for this. But it's kind of like the cart is before the horse.
MR. PHIL DENBOW: You mentioned a lot about time frames when you were speaking. How about cost for traditional manufacturing versus this type?
MS. MELFI: It depends. If you are taking a big piece of steel and machining it, typically if it's a stainless, you will do better here using this method because you are using less metal, and you have less waste. But I would say that this is better if you are doing one to 10 of something. If you are doing fifty or a thousand, you might be better off with a casting.
MR. DENBOW: The other question, I'm thinking more like the press industry, have you come across anything there like large cylinders et cetera? There are usually huge lead times on those. Again, I'm talking from an insurance aspect, but any information along those lines?
MS. MELFI: I can tell you that there are prototypes out there. I don't know whether there is anything out there already, but there are prototypes out there, and they are definitely looking at this. And I think we will probably be seeing parts in use within a year or two.
MR. DENBOW: And how do they hold up fatigue stress-wise?
MS. MELFI: From a fatigue standpoint, typically you have to post weld heat treat to get rid of the residual stresses, but the nice thing is you have the design freedom. So, you can do those kinds of gusseted designs, or you can make them a little bit thicker where you need to. In general, they are very good in fatigue applications. But you have to know what you are doing. The designer has to know what they are doing.
MR. RONALD SPIKER: In the application like 1,500 psi to about 2,500 psi for extruded parts in the steam industry, is this something that might replace some of that long lead time for getting the extruded parts?
MS. MELFI: I would fully expect that that would be one of the places that you would see this used.
MR. SPIKER: Because that's where you have got critical pieces. It's usually right at the bend coming right out of it.
MS. MELFI: And because weld metal and GMAW welding is so well understood, there is quite a continuum of not only alloy types, but strength levels. And we have seen people using all kinds of different strength levels and all types of different alloys.
Thanks. And again, I am really interested to hear if you have comments, suggestions, things we need to look at.