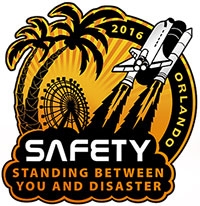
The 85th General Meeting Feature Presentation
Denis DeMichael
Overpressure Protection — Recent Improvements and Current Influences
The following presentation was delivered at the 85th General Meeting Monday afternoon session, May 9. It has been edited for content and phrasing.
Introduction:
Denis DeMichael chairs the ASME Subcommittee on Safety Valve Requirements and serves as senior consultant for the Chemours Company. Following his graduation from Purdue University, he was employed by DuPont for 40 years in various operations, maintenance, and technical capacities. For 39 of those years he was involved with relief devices including 22 as DuPont's pressure relief technology steward. Since the 1980s, Mr. DeMichael has taught pressure relief design seminars to over 1,800 participants. He is currently a member of the API Subcommittee on Pressure Relieving Devices. He is also a member of the National Board Subcommittee on Pressure Relief Devices. His ASME involvement includes membership in the TOM-C, ASME Section 8, and U.S. Technical Advisory Committee to ISO/TC-185. His technology contributions were acknowledged in 2012 with recognition as an ASME fellow.
Mr. DeMichael's slide presentation can be accessed here.
Mr. DeMichael:
Thank you. I would like to take you through a chronology of events, overpressure protection and pressure relief. I'm going to start off by identifying three significant safety enhancements that I think have contributed greatly to the overall safety of pressure relief devices. I'm going to look at some influences currently affecting how we design pressure relief systems, and I will finish up with looking ahead at what may be coming down in the future.
The three items I have identified for what I consider significant safety enhancements include capacity-certified liquid pressure relief devices, ASME-certified rupture disks, and finally the National Board VR stamp.
Let's cover the capacity-certified liquid devices first. Previously, valve capacities were certified using only gas or steam. Most of the time, the gas was air. Whether the device is a Section 8 or Section 1, it was designed pretty consistently. If you look at the circled area that I have on the diagram, the configuration of the valve, the geometry, was designed to take advantage of the expanding gas to obtain lifting forces to get the valve to pop open and stay open.
Now, when you use that same valve on liquid, you don't have the advantage of the expanding gas. The valve may not perform the same when you use vapor valves in liquid service. So the industry addressed that by designing the relief valve or sizing the relief device for 25 percent overpressure. So instead of the typical 10 percent, you were required to design to 25 percent, thinking that the extra delta-P across the device would keep the valve open. The only bad part was that it required you to set the relief device well below the MAWP, and in some applications that didn't work out very well. So they developed another capacity correction factor and said, okay, if you are using the valve somewhere between 25 and 10 percent overpressure, there is a capacity correction you have to apply, and that essentially made the valve bigger.
So we have a valve that was really designed for vapor service, and then we ended up correcting the capacity by making the valve larger, and in some cases the performance wasn't really what we wanted to see. So the code rules were incorporated in the code for the capacity certification of liquid devices. And if you look at the pictures, you can see that essentially what the manufacturers would do is redesign some of the arrangements of the details of the valve to be able to obtain sufficient lifting forces from the liquid.
Secondly, let’s look at ASME-marked rupture disks. Previously there were two capacity methods that were prescribed in Section 8 for sizing the relief devices. I have listed two methods there, but regardless of which method you used, the capacity was based on an orifice calculation similar to a relief valve. Now, the issue with that is if you had long inlet lines and long outlet lines, it affected the capacity, and there were not really any provisions for dealing with that. So in addition, there were no ASME requirements for markings, so most of the manufacturers that did have their own quality control systems, they weren't the same, they weren't a common quality control system as you would have with the ASME mark. So code rules were incorporated to require the devices be marked and capacity certified.
There are two methods of certification. One is capacity and one is a resistance-certified method. And the resistance method established a velocity head loss factor, resistance factor, just like you would have for an L4 remote valve. So when you did your pressure drop calculation, you were able to establish the maximum flow of your relief system, so you had a real good idea of what the relief system could pass.
Now, many of the manufacturers, because the new methodology required a significant amount of testing, put in their own ASME flow loops to help with the testing. The advantage or one of the benefits is that the manufacturers learned a lot more about their devices, the devices became better, they enhanced their performance, and a better performance safety device helps us all.
The last enhancement I want to discuss is the National Board VR certificate program. One of my years at DuPont I was assigned to a plant that had 1,500 relief valves, and we had a VR stamp. I had an opportunity firsthand to see how the VR stamp could enhance your relief valve repair. Over the years that I was involved in the program and saw how the repairs were approved, we saw how the mechanics and everybody associated with it learned more and more about how the devices performed. Training was improved.
One of the things it identified very early on is that -- well, with 1,500 relief devices, you can imagine, we had a pretty large chemical operation, so we had a lot of mechanics. And at one time we thought, well, the benefit of a large mechanics group is you try to train as many skills as you can to maintain your flexibility, and that included relief devices. So we had a dozen mechanics, let's say, qualified to do relief devices, and we learned early on that even at 1,500 devices, there wasn't enough devices there to keep that many mechanics qualified to properly repair relief devices. So we dropped that number down pretty quickly.
The other thing we learned is the equipment was very important. If you look at the chart -- if you look at the arrangement for the test equipment, you see a large test vessel. I talked about a vapor valve, needing to have it pop open and get a full lift. When you are repairing a valve, taking it apart and preparing it, when you’ve cleaned up all the parts, machine it, to help make sure and help convince yourself that that valve can do what it needs to do when you put it in a plant, you need to get a good, sharp pop out of it and activate it, and you are not going to get that unless you have a good size test vessel.
And if you go back many years, at one time people were testing the valves with a nitrogen valve and a pressure regulator, so that was way back when, but that was done. So let's look at some of the current influences that involve relief devices today. You want to look at how life continues to get complex, no matter what field you are in. Relief devices are no different. There is OSHA law that affects relief devices and overpressure protection. I guess if you had to pick a couple words or a sentence to describe the complexity of relief system design, I think I would pick it's just not good enough to size and spec out a relief device; what we really need to do is design relief systems. That's what's really changed. Because you could have a properly-sized relief device, and until you attach it to a vessel with the proper attachment, and until you put in the discharge line or the tailpipe and run it to some location and make sure that tailpipe doesn't improperly influence the capacity of the device, and you look at what's coming out the stack and you make sure that doesn't create another hazard when it does discharge, you really don't have a properly designed relief system.
So if you go back to the past when you were building the plant, you probably found that the required relief rate was developed by the process engineer, the instrument mechanic sized the relief valve, and the pipefitter or the pipe sketcher or the model builder designed the rest of the relief system. So we are way past that now, and usually one person now is responsible for designing the whole relief system. And if you look at the charts there, I have provided you some of the skills required to design a relief system. Someone has to have a broad background. In fact, if you look at that, is there anybody who is really going to be an expert in all of those skills? Probably not. But someone should be responsible that all those functions are properly done.
And that's especially important for any time you get skid units or packaged units. When you are designing the whole relief system, you know what's coming out of the device, you know what to expect, you know how to mitigate any hazard. When you buy a packaged unit, sometimes someone else designed the relief system, and you really need to understand it to design the rest of it and connect it to the discharge system. You really need to understand what's coming out of the device.
Now, to help you with the various aspects of the relief system design, you can go seek a lot of standards that could help you. There are a lot of recognized and generally-accepted good engineering practices for relief devices. I'm not going to go through all of these, but I'm trying to just give you an example of what all is involved and how much help there is out there for you.
API has a lot of standards. ASME has standards. Notice I didn't list Section 3. Just for the sake of this presentation, I just listed some nonnuclear “recognized and generally accepted good engineering practices” (RAGAGEPs). There are some materials like chlorine where organizations put out specific guidance. The Compressed Gas Association has their guidance. Ammonia refrigeration, National Board, NFPA has several documents, and U/L. So there is a significant amount of information out there available to help with the design of relief systems.
Now, in any given relief system, all of those standards aren't applicable, but the challenge is knowing which ones are. The ironic part of having all those documents and standards out there to help you, is that there is not one standard that gives you guidance on providing you the steps for designing a relief system, so we are missing that in the technology.
Concerning two-phase flow: the current state of the two-phase flow technology originated from some safety incidents that occurred on runaway chemical reactions. At that time, the common wisdom was if you have an energetic reaction take place, you generate a lot of vapor, but they always thought that you would have a nice liquid level maintained and you would vent gas. And what happened, several incidents occurred where the champagne-bottle effect occurred where they had a relief event, they essentially discharged almost the whole contents of the vessel. So this generated some questions. A couple of these events occurred, so 29 companies formed a consortium to develop the Design Institute on Emergency Relief Systems, and they pretty much developed all the technology and sizing methodology that's used today. They spent close to $1.6 million in investigating the phenomenon. The interesting item on this is depending on the type, and there are various types of two-phase flow, but one type of two-phase flow could actually require you to have a relief device that's 10 times the size of whether you were getting all vapor or all liquid venting.
So the required relief rate can be considerably greater, depending on the type of two-phase flow that you have. That committee, it is no longer a consortium, still works -- it's still out there working to enhance emergency relief systems, but the technology is well accepted now. There are more and more RAGAGEP -- guidance that is incorporating that technology into their design documents, and it's not just limited to reactive systems. So any vessel that contains a liquid level has the potential on an overpressure event to discharge two-phase flow material.
OSHA, 29 CFR 1910.119, process safety management. And this law applies for any employer that has one of the 119 listed chemicals in quantities greater than what they established was the minimum level, or it also applies if you have 10,000-pounds of flammable gas or liquid, and the law defines what flammability means. The law requires employers to document that your relief systems -- among many other requirements, be recognized and are generally accepted good engineering practices. So if you have five of those RAGAGEPs that I listed applicable to a relief system, you are required to document that the design does comply with that.
It also has a different interesting aspect to it. Now, if you could do that when the plant is brand new, that's fine, but the requirement kind of never goes away. So even as the standards you used get updated, the law still says that if you built your plant to existing standards that aren't commonly used anymore, and that would include old versions of existing documents, you still have to show that it's safe. So it puts a lot of emphasis on using the RAGAGEPs and incorporating them into your design.
This law has heightened awareness around making sure that your relief systems comply with recognized and generally-accepted good engineering practices. Some companies have carried it beyond the 119 materials that they list are flammable. They will use it for other devices on their site. Some standards development organizations have seen an increase in participation, especially ones that deal significantly with relief devices; they have had an increase so companies could learn more firsthand what the standard contains. And there have been several new companies that have formed to help companies comply with this requirement. So they will go out and hire them to help you design and document a relief system. They are becoming a central focus on the technology.
I mentioned that there wasn't any one document that helped you design a relief system from scratch; help you with the step-by-step process. So currently there is a proposal to help develop that type of document. Right now there is a proposal for Section 13 to develop a comprehensive overpressure protection resource, and the rules for the document would all be invoked by the construction codes. All the requirements for the devices would still have to come from the construction codes. And probably the best way to describe the content of the document is to start off by telling you what's not in it.
The rules for the application remain in construction codes. The types of devices, number of devices, maximum relief pressure, required relieving capacity, installation -- any installation requirements as they pertain to the protection of the vessel would be there, any conformity assessment requirements would still remain in CA-1.
Now, what's in the scope of the document would be content drawn from the existing construction codes. It would also include PTC-25, and you would see rules for pressure relief devices, materials, construction, testing, settings, capacity certification, and you would probably see some installation requirements as they pertain to the performance of the device. They would also include what's currently in the Section 8, UG-140, overpressure protection by system design, in cases where a conventional relief device won't work with a particular substance or the reaction occurs so fast, a pressure relief device can't respond. For example, the way it would work: let's say the UV requirements in Section 13, but the way they would appear in Section 8 is that Section 8 would say only UV devices are permitted in accordance with Section 13. So the requirement for using UV devices would still be in the construction code. It would include mandatory requirements and some nonmandatory guidance.
The mandatory requirements would be involved with the device itself and certification. Since we wouldn't necessarily be bound by the current code scope, although we would focus in on that, we would look at some other equipment, rotating equipment, low-pressure vessels less than 15 psi. But even as a resource that covers many topics, we still wouldn't duplicate what's already out there. For instance, we would cover the importance of maintaining your devices, but we would reference National Board Inspection Code (NBIC) for the repair of relief devices. We would incorporate it into our guidance, so if someone didn't know anything about relief devices, they could pull out the book, look up repair of relief devices, and the book will refer to the NBIC. But there would be one document people could refer to if they didn't know anything about relief devices.
What we are striving for is the consolidation and standardization for the relief device rules themselves, sort of like trying to take the best from the best. So you have all these rules split among the various code books, and we would take all the requirements, look at all of them, and incorporate the best from the books. Although the construction codes would be our primary focus, we are not limited to their scope.
We have an issue right now, for example, where users like ASME certified devices, they like the ASME certified relief valves, but you can't buy one for less than 15 psi. So where do we put rules for certifying devices for less than 15 psi? Do we burden Section 8? That's outside their scope, they are not interested. So we are free to look at topics that we could get into and provide guidance that we are not limited by the current scopes of the various construction codes. And we feel that when we have an organization to deal with low-pressure protection, we will be attracting more subject matter experts in the field, further enhancing the content of the book. And again, we are focusing on a comprehensive resource, still maintaining the control and the application within the construction codes, but having a document that is maintained by subject matter experts providing the construction codes with the best available technology for them to pick and choose what's best for their construction code.
One last thing I would like to cover is storage tank vent repairs. It's been my experience -- I haven't run into too many pressure vessels built to the code that have been damaged, but I have run into a few more storage tanks that either collapsed or have been oil-canned at the bottom. And there are a lot of reasons for this, but they do have safety devices on them. And many organizations go to the R shops for the repair of their relief device, their storage tank vent, and the guidance for these tank vents is limited. So we have an open work item in the NBIC to develop some guidance for repair of tank vents. Now, it won't be anywhere near the sophistication of the R stamp program, but it would be at least some high-level guidance to give VR shops some help with tank vents.
I have taken you through a little bit of history in terms of what I thought was some significant improvements, and then I covered a little bit about how the current laws, recent two-phase flow technology influences the design of the relief systems, how they are complex and need to be designed by at least having one person responsible for the overall design, even though they may not be an expert for all that, into possibly the developing of a Section 13 to provide overall guidance on relief system design.
MEETING ATTENDEE: Is the “lower pressure safety valve, lower than 15 psi,” driven by vacuum boilers starting to show up?
MR. DeMICHAEL: The less than 15 psi, not really, although that would be an application. I think it's really driven more by if you have a vessel that may be designed for 10 psi, some of the ASME devices could go down that low, but there is no way to certify them because there are no formulas, no equations. Once you get below 15, you are in substandard flow regime, you have to have a whole new set of equations to do the certifications.
MEETING ATTENDEE: Section 4, vacuum boilers, it is 7.5. That's for safety valve requirements in Section 4.
MR. DeMICHAEL: I guess at this point we would have to look at it to see how that would affect it, if anything.
MEETING ATTENDEE: It's called a vacuum boiler; it operates down to two or three psi once it goes through a phase.
SECOND MEETING ATTENDEE: And that's in Section 4?
MEETING ATTENDEE: Yes.
MR. DeMICHAEL: If there is methodology for that, we would look at the vacuum situation, because there are devices available for vacuum blowers, and that would be a source of technology that we could use. We would look at that. I'm not all that familiar with it so I can't say much more than that.
MEETING ATTENDEE: Could you go through briefly the process on Section 13 as far as the timing of it, how that is going to proceed?
MR. DeMICHAEL: I believe what's left is for the board to approval it. It's been through the construction codes. With board approval, I believe the next part of the process would be to appoint a standards committee to develop the final chart, then it would have to be approved, and then the document. The standards team would have responsibility developing the document.
MEETING ATTENDEE: One of the things that was mentioned under the chart was the overpressure by system design, overpressure affected by system design. As I understand it, that is currently pretty much limited to a few special cases in Section 8 and not really widely used. The vast majority of vessels are still protected by more or less conventional overpressure protection via devices, safety valves and what have you. I'm just wondering a couple of things. Whether you have or are contemplating growing expertise in understanding the processes that will help you understand the need for overpressure protection by system design? Because I think maybe that body of knowledge is currently being in Section 8. And I'm also wondering whether you are planning to generalize that so that it comes up in other book sections than Section 8?
MR. DeMICHAEL: Well, let me handle the last question first. It is the intent to put it in Section 13. But as far as generalizing it, the actual construction code would have to adopt it to permit its use. Now, if you mean by generalizing it, make it more applicable, that if another book Section wanted to use it, could they use it, is that part of the question?
MEETING ATTENDEE: I was wondering if you were going to somehow restrict the application of those provisions to Section 8 or whether Section 13 intends to publish this, whether it would be applicable to other Sections?
MR. DeMICHAEL: It would not be applicable to other Sections unless they incorporate it by reference.
MEETING ATTENDEE: So it would be set up in a way that book Sections would have to turn on that provision?
MR. DeMICHAEL: Right. The whole document is set up that way. This is to keep the construction codes really in control of what it takes to maintain to protect their vessels. Think of it as being a shopping cart where we will have one methodology for capacity certification, because you pretty much use the same methodology, but you will have different stages for boiler, a three percent overpressure valve, blow valve, or liquid. But it will all be in there, but the particular valve is going to have requirements for UV or for V valves and it will still have to be referenced by Section 1 before it could be used.
MEETING ATTENDEE: So it would still rest with the device -- with the boiler or pressure vessel manufacturer to decide how much of what is being generated and how much needs to be relieved, and once that information is known, then Section 13 would tell you how to do it?
MR. DeMICHAEL: Section 13 would provide the certifications for the devices.
MEETING ATTENDEE: Okay.
MR. DeMICHAEL: It's not much different from what it is now. Think of it as a big shopping cart. It's almost the best of both worlds for the construction codes. You have a group of subject matter experts that are optimizing developing the best technology, yet what the construction codes utilize, it's up to them and how they apply it. We are still going to have all the requirements for establishing the maximum relief pressure for the equipment, any installation requirements for the protection of the vessel, how many devices you could use. If you choose to use overpressure devices designed to Section 8, you would have to incorporate that by reference. Everything has to be picked by the construction code. Now some things are common in terms of valves, you would expect to have construction code people on the committee also. And I don't think we will go out and change anything below four percent blowdown or three percent overpressure. That's inherent with what the system is now; we are not really going to change that.
MEETING ATTENDEE: In terms of research going on for certification of relief devices for thermal fluid heaters, such as the organic and inorganic oils or even light-bulb phase systems which is considered fluid, what's going on in that realm?
MR. DeMICHAEL: I believe that's back at Section 1 and they are going through another ballot. They have all the comments back from safety valves, so that item is moving on. Any particular aspect?
MEETING ATTENDEE: Well, Section 1 right now only deals with vapor systems, and a lot of fluid systems remain in the liquid phase, and Section 1 doesn't address that right now.
MR. DeMICHAEL: Okay. So they have a new item active to discuss requirements for Section 1 liquid phase heaters. And from a relief perspective, safety valves have provided their input, and that work continues.