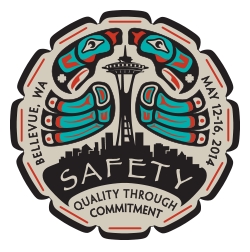
The 83rd General Meeting Feature Presentation
Earl Harlow, P.E.
“Relief Device Capacity Comparison from the Inspector's View”
The following presentation was delivered at the 83rd General Meeting Monday morning session, May 12, by Earl Harlow. It has been edited for content and phrasing.
Earl Harlow is a professional engineer and a mechanical integrity engineer for Sabic Innovative Plastics in Mount Vernon, Indiana. Mr. Harlow started his career with Babcock & Wilcox performing stress analysis of fossil-powered boiler components. During a career that has spanned 30 years, he has accumulated experience in a number of industries, including fossil power, nuclear power, aerospace, and petrochemical processing. He is a licensed professional engineer in California and Indiana, and also holds a boiler inspector's commission. After completing his bachelor of science degree in civil engineering at the University of Illinois in 1980, Mr. Harlow pursued his M.B.A. through postgraduate courses at four different universities. Mr. Harlow is a member of the Indiana Boiler and Pressure Vessel Rules Board, and was a presenter at the 66th and 76th National Board General Meetings.
Mr. Harlow's slide presentation can be accessed here.
Mr. Harlow:
We are going to start by talking about a couple of paragraphs in the NBIC (beginning with the 2007 Edition). The two paragraphs of interest are -- Part 2, Paragraph 2.5.2(c), and verifying the nameplate capacity on the relief device and, if possible, comparing the system capacity to the requirements. And Part 1, Paragraph 4.5.4(f) that had a requirement for the owner to provide the pressure relief device calculations for review by the jurisdiction.
With the two of those combined, we have something that was historically not done. Historically we did the power boilers and the water heaters and compared those capacities. It seemed like an easy thing to do. We can add the relief capacity for all the relief devices on the boiler and then look on the nameplate at the steaming capacity and verify that we have adequate capacity for the boilers.
Similarly on the water heaters, we can look at the kilowatt capacity of the fuel coming in and convert it to BTUs and again look at the rated capacity on the relief device, either ASME or the CSA capacity. Oh, wait: we have to figure out which capacity to use. Fortunately for you, the winter 2014 National Board BULLETIN published an article, “ASME/National Board vs. CSA Rating on T&P Relief Valves,” that gave clarification. It says use ASME capacity when it is ASME code stamped and use CSA capacity if it's not ASME code stamped. Furthermore, it says "if possible," and in the past that has allowed the inspector this little out to maybe skip over the unfired pressure vessels. Now when he says "if possible," the inspector always has the capacity calculations available to him, so he should always be able to compare the two.
But unfired pressure vessel capacity is a little more challenging because you must have knowledge of the process, and then you have to figure out what to use. Do I use API 520, 521 for my sizing, or do I use ASHRAE or NFPA? They have guidelines for flammable chemicals. We have to decide the right methodology and then from there do some sizing.
In this relatively simple diagram there is a process inlet at the bottom going into the reactor, the reactor has a reaction, it dumps into a drum, and from the drum it goes to a reboiler. The purpose of the reboiler is to heat a fluid into a column, and then the bottoms of the column come back to the reboiler. The heating process is usually steam, or in our case hot oil or steam. The steam comes in. You have relief protection for the steam system right here on the vessel, and the top of the column is going to have a relief valve. We are driving the heat into the system to vaporize some of the liquid here, and the liquid then comes into an overhead condenser. The purpose of the overhead condenser is to take that vapor, condense it back to a liquid so it's easier to handle, and from there, you will find we have cooling water on the condenser to condense it, and the cooling water relief. Now, the process side is a little more complicated than some of the other sides, because you will notice there is one process relief valve for many vessels in this area. One question you have to ask is where is this area? Is it a large manufacturing area where you may have areas that have flammable chemicals and others that don't, and which of these vessels need to be combined to give me a good capacity for my relief protection here? Not a trivial thought.
Keep that little process in mind, because now we are going to eliminate the confusion and take the process out of the picture, and for our purposes, we are going to focus on just the water side. And on just the water side, we are going to say that condenser, as most condensers are back here on the previous page, this condenser here has cooling water in the tube side condensing the vapors in the shell. So remember, the cooling water is in the tube side. It's a tube and shell exchanger.
Here we are looking at the contingency analysis. I listed five or six, but there are actually 16 contingencies to consider in API 520, and the last of those says, "And others not listed." So you get a good opportunity to do some free-wheeling thinking about what else might be there. Given all of those different contingencies, for our example, we are going to assume that steam is a controlling contingency. And it's going to be a fire case situation to create the steam for our contingency, and again water is on the tube side. If water is on the tube side, and I use these formulas for calculating, what is the required capacity when a fire case occurs? Hmm, what is the right area for that fire? Normally we say if it's within 35 feet of the floor, we are going to engulf a certain area of that exchanger, and that exchanger then, given that surface area overheating, gives us an area.
In the heat exchanger, we will assume that to be the shell; right? Not a good assumption, because remember in ASME, conservatism is all good, with one exception: relief capacity. Because the concern -- and you will see this when OSHA talks about it -- the concern in relief protection is that you don't make it too big. If you make it too big, everybody says, “Oh, it will be good.” No, make it too big and it will chatter. It will chatter until it stops. If it stops when it's closed, it won't open again, and we will have a catastrophe. So sizing properly is very important, not just conservatively.
The contingency analysis that we talked about is very time-consuming, and so for this poor inspector who is out there looking through this pile of calculations, maybe 35, 40 pages, he's got to assess for himself, what is the required capacity? If he's very good and the guy doing the calculations or the lady doing the calculations was very good, there is going to be a summary page. That summary page is going to be here, and in a minute here it's going to say 10,000 pounds per hour, .982 square inches in the D orifice, and the stamped capacity of the valve is 25 GPM.
Wait a minute. It can't be 25 GPM because we said we need 10,000 pounds per hour; right? Is the valve acceptable? It may be. Because if you look at the API codes and other articles, it says that the capacity rating of the valve installed should be what the liquid is normally in the vessel. Normally this is cooling water; right? Cooling water should be liquid, and so this valve should be in gallons per minute, and it should be a liquid relief valve as opposed to a vapor relief valve. Again, not a trivial thing, but given a little bit of reading, you can learn a little bit about this and go on from there.
Then we have to ask our question about area. Every relief valve has two areas. It has the API area and it has the ASME area. But which do we apply to this valve when we are looking at area? The first one says maybe it's not very easy for the inspector to just look at a capacity and compare it to a stamped capacity on the valve. The next one we are looking at is this area here. And so we will go to the next chart, and it says -- oh, look at that -- the two areas aren't the same. And I guess that shouldn't surprise us, right?
The summary sheet said API area was slightly less than that, the ASME area for this valve is slightly greater than that and it's either right or it is wrong. As an inspector out there, if you ever have a problem, think about all the resources available to you. Don't be afraid to call a chief inspector; don't be afraid to call Joe Ball. He's the guy I call a lot. These guys are wonderful in helping you do the right thing. Doing the right thing is what it's all about. Once I call Joe and he explains, “Well, this is what the API area is about, this is what the ASME area is about, then for this valve I can use the ASME area and it's acceptable. “
What I have to worry about is when we come to a turn-around and somebody puts in another D orifice valve and the API area of that D orifice valve is different -- the ASME area for that D orifice valve is different, the API area is going to be the same, then is it going to be acceptable? And the answer is again, maybe. You need to go look and see, and going to the area gets kind of confusing. My guess is the inspector's best, reasonable chance and reasonable best check is to go to the orifice size. The orifice size is either found in the model number or the serial number and gives the inspector at least a chance to get the right thing as opposed to getting confused.
The next thing I did was an unscientific survey. I called six of my inspector friends and asked, “Are you aware of this change, that we adopted this?” By the way, Indiana was a late adopter because it was a major change in the code. Until as a board we really understand what we were trying to adopt, we shouldn't be adopting it. And then we found some things in it that made us uneasy and we weren't really sure about, so we didn't adopt the new version of the code until about a year and a half ago. And then after six months, I ask the inspectors, “Hey, what about this thing?” And you get answers like, “I wasn't aware that the change happened,” or, “Wait a minute, that applies to just the new installation. It's only the inspectors that belong to the state who should be inspecting that. The initial installation, they will inspect that. I don't have to worry about it.”
And each of those answers weren’t very positive for me. They didn't feel trained. They didn't feel confident. They didn't feel like they understood what their role was. And then they said there wasn't any communication indicated in the requirement, but I know that there was a communication. Maybe that communication didn't get down to the inspectors.
The other concern I have is this effort to do the relief valve evaluation, which is very time-consuming. And I say time-consuming because not only do you go out to the vessel, you see, you read the stuff off the nameplate, you write that down. In the case of the boiler, you went to the nameplate, found the rated capacity, and away you go. In this case you go to the calculations. Those calculations may be in the same building, they may be a block down the road, and they may be in a completely different facility in some equipment file. So it's going to take a lot more time to do that inspection and do it right. I would say on average probably two to three times what it took today it will take if you do the comparison we are talking about here.
The concern I have is it says here inconsistent application from inspector to inspector is unfair treatment of the owners of the equipment. Now, that's what it says there. And then I have a note that says look on page seven. So most of you have one of these little books here; right? On page seven, it talks about our objectives. The first one says, “Promote uniform administration and enforcement of laws, rules, and regulations pertaining to boilers, pressure vessels, pressure-related items, and their appurtenances.”
Uniform. And this thing said inconsistent application from inspector to inspector, because it depends on an inspector and it depends on his own integrity and his own knowledge and his own willingness to go the extra mile and figure this thing out. Some will, and some will not.
You might ask, “What kind of training do we give the inspectors when we change the rules?” That's an area we need to improve. So what I said is suggested actions. And I suggested getting some input from the inspectors; have them give you input from what they have done in the last several years that this has been out there. And then you need to clarify what the intent is to the inspectors. I think that that helps them understand the expectation.
Now, does that come from the National Board or does that come out of the jurisdictions? That's a good question, but I think it's important to clarify the intent for the inspectors so we get consistent inspection from inspector to inspector, and then develop a management-of-change process.
When we made this change, the training wasn't out there, and in every management-of-change system, training is a key component. And so is communicating those changes to the inspectors. One of the questions is, how would I know who the inspectors are? Every year in Indiana, I have to renew my license, and so jurisdictions are going to have a list of all of those inspectors. If we had a communication developed for the jurisdictions, then the jurisdictions should have that communication to all those inspectors at least in the next year. And that would give a clear communication as to what the expectations are and where we are going with this thing so that we do get consistent application of the program.