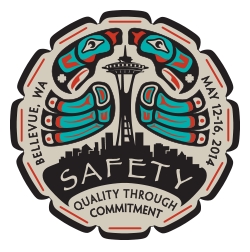
The 83rd General Meeting Feature Presentation
Melissa Wadkinson
“Overview of Thermal Fluid Heaters”
The following presentation was delivered at the 83rd General Meeting Monday morning session, May 12, by Melissa Wadkinson. It has been edited for content and phrasing.
Many in the inspection discipline have periodically dealt with thermal fluid heaters. Melissa Wadkinson has quite a background dealing with these equipment types. Ms. Wadkinson is the chief engineer for the Fulton Companies. Fulton is a global manufacturer of heat transfer systems. She possesses 20 years of industry experience that has included hot oil, steam, and hot water products and systems. Ms. Wadkinson's responsibilities have included new product development, applications engineering, system design, technical training, quality assurance, and codes compliance. She is a member of the NFPA 87 Committee on Recommended Practices for Thermal Fluid Heaters. She is also a member of the NBIC Subcommittee on Installation. Ms. Wadkinson has also served on several ASME committees and subgroups, including CSD-1, Section 1 Subgroup, Design and General Requirements, and Section 4, Heating Boilers. She holds a master's of science in chemical engineering from the University of Massachusetts, and a master's of business administration from Syracuse University.
Ms. Wadkinson's slide presentation can be accessed here.
Ms. Wadkinson:
Thank you very much for this opportunity. What do craft felt, an automobile windshield, a golf ball – I'm sure many of you are very familiar with those – and quartz countertops have in common? They all require the use of a thermal fluid heater in their manufacturing process. Generally, if people think of thermal fluid heaters at all, they think about large chemical plants and refineries. And what I'm hoping to share with you is that they are actually responsible for many of the day-to-day products that you use, and they are in your small plants in different types of applications.
As inspectors you may come across thermal fluid heaters, and I want to give you an overview of what you should be aware of. Compared to power boilers and heating boilers, there are a limited number of thermal fluid heaters installed throughout the country, throughout the world, and there hasn't been a lot of guidance. You can't go pick up a book, “Thermal Fluid Systems for Dummies.” It just doesn't exist. And even among the jurisdictions there isn't any one way to treat these systems. The purpose of this presentation today is to give you an idea of what's out there, some of the things to be aware of, some of the key components in the systems and how they are used, but also to let you know some work that's being done in different codes and standards committees to hopefully provide that additional guidance you would need.
I am going to touch on a brief description of the thermal fluid system, a short comparison of thermal fluid to steam, why does anyone care, what do they want to do with this, talk about critical system components, a few system and safety considerations, a couple points if you are reviewing an installation that you might want to be aware of, and closing with some of the work in the codes and standards committees.
So what is a thermal fluid system? There are two types. You can have thermal fluid in a vapor phase or thermal fluid in a liquid phase. I'm going to touch on a vapor phase system, but I won't spend much time on it because it’s really not a large part of the market today. Vapor phase systems could be one of two ways. You could have thermal fluid that's actually vaporized within the pressure vessel itself, or you can have thermal fluid that's in its liquid state and it is flashed into vapor through a flash drum external to the heater itself. In both cases for the vapor phase system, that fluid is being heated high above its boiling point, and there is a very specific set of fluids that are designed for vapor phase use that all boil at about 400°F.
In contrast, a liquid phase system keeps the thermal fluid or hot oil in its liquid state throughout the process. It's a flooded pressure vessel in which the heat transfer media is heated, but no vaporization takes place. It's important to note that this is a closed-loop system, and depending on the system itself, it can be open to the atmosphere or it could be closed to the atmosphere. The vapor phase system is very similar to a steam boiler. I’ve got vapor, it's condensing, giving up its heat. I’ve got to get that condensate back into the system in a gravity feed return or pumped return. A liquid phase thermal fluid heater is very analogous to a hot water or high-temperature hot water system. You are keeping it in its liquid state throughout the process.
This diagram is a schematic of a vapor phase system where we are going to make the vapor external to the heater itself, pump the liquid through the heater, heat it above its boiling point, come in to a flash drum where you've sized an orifice, and then the vapor going off to the system that will then be returned.
Next is a schematic of a liquid phase system. From our process, through a pump, through the heater, out to the process, and then we have an expansion tank somewhere in the system, because one of the unique properties about these fluids is that it expands in volume as it is heated.
There are some different design features to be aware of. Heaters are commonly direct-fired by combustion of fuel, or you can use electric resistance elements. The heater design can be similar to a firetube boiler, electrically heated boiler, or most commonly it's going to be a watertube-type boiler design. These systems can operate up to temperatures of 750°F depending on the fluid that you are using. There are large heaters that are fuel directed. However, the heaters that are smaller than 30 million BTUs are more commonly going to be found in some of your smaller manufacturing processes, and they are very similar in that fashion to packaged boilers, so you are going to find them in a lot of typical boiler room applications.
Many of the thermal fluid heaters are more of a watertube-type design. They are going to have a helical coil, most often carbon steel, vertical or horizontal heaters, and it's going to depend -- you are going to have wraps of coil in parallel, and you could have multiple coils, one within the other, depending on the specific heater design and the BTUs required.
Why would anyone use thermal fluid instead of steam? We have steam, we love steam, we have used it forever; right? So what are some of the advantages of thermal fluid heaters? Well, you don't have to worry about corrosion or freezing. This is a noncorrosive application. It's a simple circuit, especially when we are talking about liquid phase systems. There are no blow-downs, no steam traps, no condensate return systems. They have minimal maintenance. There are no handle gaskets, there is no re-tubing. There are not any water treatment requirements. And, again, they get that really high operating temperature with low system pressures. So that's one of the real driving factors with this technology. The other unique thing about thermal fluid systems is if you do have an application that requires heating and cooling, you can actually do that with a single fluid if you design a system properly.
Next is a chart comparing thermal fluid to steam. If you are looking at a process that needs somewhere near 600°F of heat transfer, if you are using steam, you are going to be looking at over 1,500 psi. If you are using thermal fluid and you want to get to 600°F, the pressure in your system is only that which is required to overcome the pressure drop of the heater, the piping, and the other system components. So that's your controlling factor.
Hot oil can be used with a variety of end users and applications. You can use thermal fluid to heat a variety of storage tanks, valves and kettles, heated rolls, reactors, presses and molds, fryers, ovens. Any type of process requiring indirect heat transfer and high temperatures is a potential candidate for a hot oil system.
Here are some more examples of products that use thermal fluid heaters. If you or your kids/grandkids have ever had a chicken McNugget, odds are the McNuggets were cooked in a fryer whose cooking oil was indirectly heated with thermal fluid. Baths and kettles are used in the adhesives industry, wax, and cosmetics. You are going to see reactors in the pharmaceutical industry. And has anyone been to Disney World, stayed at one of the hotels on the property? Disney has a large industrial laundry and they actually have what's called an ironer. It has a heated roll that's heated with thermal fluid, so the linens are fed across these rolls which simultaneously dries and presses the sheets. It's quite an operation. You can take a backstage tour. Presses and molds are used for gaskets and rubber compounds. If you are a Kentucky Derby fan, there is a company in Wisconsin that makes special rubber mats used in the stables of thoroughbred horses that are made with a heated press that's heated with thermal fluid. You will also commonly see thermal fluid being used to heat storage tanks.
About system components: in your hot oil system, there is a heater, a circulating pump, an expansion tank, and the user. Again, the users are presses or kettles, anything that we are heating. The air bag in your car, that material is cured over heated rolls, just another example. For anyone who still smokes cigarettes, I have been told there are 17 different types of adhesives used in cigarette packaging. All of those adhesives use thermal fluid in their processes, specifically for heated kettles and baths to keep the adhesive at the right temperature for processing.
With these systems there certainly are some system and safety considerations which should be taken into account. I'm going to touch briefly on the thermal fluid selection, the pump and the proof of flow through the heater, high temperature limit, a stacked temperature limit, and expansion tank design and fluid level.
Thermal fluid selection is critical and something for you to know if you are asked the question. There are a specific set of fluids designed to be heat transfer fluids. Lubricating or hydraulic oils are not acceptable, and neither is vegetable oil, although I have seen people try it. These fluids have a specific set of temperature-dependent physical properties, and those properties have to be available for somebody to look at to understand what's going to happen. The specific heat, the viscocity, the thermal conductivity, all is a function of temperature, from the lowest temperature they tell you the fluid is good for to its maximum bulk temperature. Anyone who is always asking, “is this a thermal fluid” and they can only show me that its boiling point is at 500°F or its specific gravity at 60° is .8, then odds are that's not really a fluid meant for one of these heat transfer applications.
When considering the fluids, it's important to look at the maximum bulk temperature. You never want to exceed that maximum bulk temperature. You are also looking at the minimum temperature you need if you are going to do cooling, and you are going to look at the temperatures for startup, and if this application is indoors or outdoors. Some of the unique fluids I was telling you about can operate up to 750°F, and are actually a solid at 65°F. Those systems have to be looked at very carefully in the design phase.
Another common point to look at when choosing a thermal fluid is its vapor pressure or boiling point. Typically in the liquid phase systems, those fluids run below their boiling point. For vapor phase you are purposefully heating it to its boiling point and beyond. Some common fluids that you might hear of are those made by Dow and Monsanto, which are an example of synthetic fluids. Paratherm and Petro Canada made some mineral oil-based fluids. You will be pleased to know that some mineral oil-based fluids used in food processing actually have been approved for incidental contact with your chicken McNuggets.
Fluids are one of the most critical components to the longevity of your system, so fluids need to be tested on an annual basis to make sure that the fluid integrity is maintained. There are going to be people out there who always want to run the system to the limits: “Oh, well, this fluid says it can only run to 600°F, but I can run it to 608°F.” Or the manufacturer says, “I need 500 GPM of flow through my heater, but I didn't design my system right and I can get by with a little less.” Well, those things are going to impact the longevity and integrity of the fluid. And by testing it annually, it gives you a very good idea of how the system is performing.
There are specific tests that the fluid manufacturers will tell you about or tell the customers, and a test that is done on lubricating oils that just includes dissolved metals is not adequate. They are going to be looking at things like boiling point and flash point and whether the fluids still have all the components in the proper ranges. People should never mix fluids, especially not between chemistries. You don't mix mineral oils with synthetic oils. But even if you have customers, clients, or end users who want to mix mineral oils themselves, once you do that, you have ruined your baseline that you use for comparison on your annual testing.
We tell people to track the inlet and outlet temperature of their process and the pressures (which is important for understanding how the equipment is operating), and record the amount and date of fluid addition. Remember, these are closed systems. Nobody should be adding fluid. If they are adding fluid, we need to find out what's going wrong with the system.
And then a question that comes up is, “I had a system that was designed for Fluid A and now I want to put Fluid B in the system instead.” It's important to note that all fluids are not created equally, and you can change from one fluid to another, but there may be considerations. For example, you may need a different motor horsepower on the pump; you may need a larger expansion tank. And there is often the process of changing from one fluid to another and using a special cleaning compound in a system before doing so.
The thermal fluid pump is important, and it's also really important to understand that this is a special pump made for high temperatures. It's not going to be a standard feedwater pump or hot water pump that you use on a boiler system. These pumps can be air-cooled, water-cooled, canned pneumatic drive designs, and are sized to overcome the pressure drop of the system. However, the one caveat is specific gravity of thermal fluid starts to decrease as you heat it up in temperature.
When selecting the pump, it's important after engineering has done their review of what the actual system pressure drop is, to make sure the pump is selected in that pressure drop and a head is corrected for the specific gravity. People who are used to water systems often forget that specific gravity is part of our equation, because it's one for most applications. This is an aspect where people can get into trouble.
Flow rate through a thermal fluid heater is really important. All manufacturers I know have a given minimum flow rate that's required for their heaters, and that's critical for the vessel longevity and integrity of the system. Somewhere on their heater they have the means to prove that minimum flow. A low flow condition can cause degradation of the fluid, overheating, and with higher fill temperatures can lead to heater failure. Proof of flow is typically interlocked into the combustion circuitry, and there are many different ways manufacturers can prove flow. You could see vortex shedding meters, flow switches, pressure switches, or a differential pressure switch.
I said that liquid phase systems are very much like hot water systems. With hot water boilers we are looking at a high-temperature limit. With thermal fluid systems, we want to do the same. We want to look at a high-temperature limit. Heaters typically are going to have a high-temperature limit to make sure we don't exceed maximum bulk temperature for that fluid. What happens if we exceed it? We are going to start breaking that fluid down, it's going to carbonize, it's going to cause problems with our pumps, and could cause problems with our heater. We always want to make sure the customer doesn't exceed maximum temperature. The temperature-sensing device should be compatible with the fluid and the system operating temperature and pressure and is located at the heater outlet, and it's generally interlocked in the combustion safety circuitry as well. You will often see these include a manual reset function.
In addition to temperature limit, you might also see a high stack temperature limit. In the event of a high stack temperature condition, the heater is going to shut off. And it's the manufacturer who is going to determine what that acceptable stack temperature is for the heater, because that's going to depend on the BTUs of the heater, the design, and the heat transfer area. And a high stack temperature, if you see that, indicates that you have got either improper combustion, so maybe somebody messed with the combustion when we started to set up the heater, or you have something such as a failed coil. Both of those things are going to tell you that we have a problem and the heater should be shut down. Some places also use the high stack temperature limit as part of an inert gas smothering system, either a CO2 or steam, to smother the flame inside the heater in the event of a pressure vessel failure.
The expansion tank is another piece that is part of our system. And the fluid selection, the system volume, and the operating temperature are going to dictate our expansion tank size. All fluids don't expand equally. Some fluids over the temperature range that they are allowed to run may expand about 25 percent in volume, whereas other fluids could expand up to 60 percent in volume. It's important to know exactly how the system is intended to be operated so the expansion tank can be the appropriate size. Now, depending on the system parameters, the temperature and the fluid that we are using, that's going to dictate whether that tank is open to the atmosphere or closed. Closed tanks are going to be pressurized with an inert gas blanket, and at that point if we are pressurizing them above 15 psi, we know we need an ASME code tank.
When should a pressurized tank be used? In general there are some guidelines. If the tank isn't the highest point in the system, you are going to want to consider pressurizing it with an inert blanket. If the tank contents can be at a temperature such that exposure of the fluid to air would cause degradation of the fluid, you want to make sure that you have an inert gas blanket.
These fluids had temperatures of about 350°F or so. If they come into contact with oxygen, they are going to start to carbonize and degrade and then wreak havoc in your system. Different manufacturers have different types of expansion tank designs, and what everybody is trying to do is make sure that that fluid isn't going to come into contact with oxygen at elevated temperatures. If the fluid is operated above its atmospheric boiling point, we want to make sure we are pressurizing the tank (or if the fluid manufacturer recommends the use of an inert gas blanket). There are some fluids where the manufacturer will say we always want this fluid to have an inert gas blanket on our system.
This schematic is the same one we looked at for the liquid phase system from the process, to the pump, to the heater, out to the process with an expansion tank. The difference is the ASME code tank with a relief valve, and a method to pressurize this tank with an inert gas. Nitrogen is commonly used.
In the expansion tank, it's always important that there is a minimum level of fluid in the tank, and you are going to have that if you want to prevent the pump cavitation. A liquid level switch or similar device is typically provided on an interlock pump and burner to shut them down in the event of a low-flow condition, and generally you want to make sure that switch is satisfied before the pump can start.
There are a couple of points to cover on installation. Again, I started this explaining that whether it's vapor phase or liquid phase, it really isn't all that different from the power boilers and heating boilers we are used to seeing. From a combustion standpoint, the burner doesn't care whether we are heating water or thermal fluid. On that note, for anything with a fuel train and a burner, the ventilation requirements, combustion air requirements, those are all very common to what you are used to seeing with steam and hot water.
A few other things are a little bit different. Because it is oil and you want to be careful it won’t get down the drains, many manufacturers recommend some sort of containment curb or seal-welded drip lip on the heater skid to contain the oil if there is a drip when they are checking, cleaning the strainer, or doing something else.
The components in the system need to be rated for the temperature and pressure of the system, but you also want to look at the materials of construction. Brass, bronze, aluminum and cast iron are not recommended. Any sign of leaking in the piping is a safety concern as the fluids or its vapors can be hazardous or flammable. Some fluids I mentioned that can reach 750°F are actually regulated by the EPA and considered toxic. So that is something that needs to be looked at to ensure people are safe in their environment. If you see a leak, it needs corrected right away. We also recommend piping should be welded or flanged wherever possible, and pneumatically tested for leaks (not hydrostatic tested). You have heard the expression that oil and water don't mix. Well, that's especially true in these systems. If there is residual water in the system and somebody doesn't know what they are doing, that water will flash to steam when it hits the 500°F oil, expand in volume, and push any other thermal fluid out of its way, and that can be messy.
For installation of pressure relief devices, it's noted that the valve should be a totally-enclosed-type with no lifting lever, and the discharge piping of the pressure relief valve should be connected to a closed vented storage tank. So think about it, when we have hot water safety valves, we are going to pipe it to make sure if it lifts, nobody is going to get burned. But other than that, at least in the installations I have seen out there, people aren't overly concerned about where that water is going to go. You do want to be concerned about where your discharge piping of your hot oil is going to go. Make sure it's contained and in a safe location where nobody can get hurt and that hot oil can't splash onto anything flammable.
Insulation should be selected for the intended purpose. And where there is a potential for fluid leaks, the insulation should be nonabsorbent. You want to be careful. Generally insulation like fiberglass insulation is not recommended around parts of the piping where there is a lot of valves and flanges and everything else. In those areas, make sure it's nonabsorbent insulation. For long runs of all welded piping, some people have used fiberglass or similar insulations.
About codes and standards: in the beginning I said jurisdictions have varying requirements for thermal fluid systems, so every state treats them a little bit differently. Some ignore them, some want them Section 8, some want them Section 1. Some don't even know they are in their jurisdiction because sometimes people don't build them to code at all. Until recently there hasn't really been a lot of guidance available, but there has been some work in the different code committees. And much to everybody's chagrin, I seem to be showing up at those places to at least try to make sure what we are putting together isn't conflicting amongst the different standards. We have the National Board Inspection Code (NBIC), ASME Boiler and Pressure Vessel Code, the Controls and Safety Devices for Automatically-Fired Boilers, and National Fire Protection, NFPA 87.
Many of you who are inspectors are very familiar with the NBIC, especially Part 2 which provides some information on thermal fluid systems, but there is an active item in Part 1 right now to cover the installation requirements for these systems. Part 1 already addresses power boilers, heating boilers, and pressure vessels. There is an open item for a supplement to Part 1 to talk about the thermal fluid heater systems, which is a little bit of a combination of what's in there for power boilers and pressure vessels, with those few unique twists for the hot oil systems themselves. The combustion, the clearances, ladders, electrical – all of those things are consistent with what's already in the code. We just need to add the additional information on expansion tanks, pumps, piping, and controls.
Regarding the ASME Boiler and Pressure Vessel Code; as I said, some jurisdictions are calling out for Section 1, some are calling out for Section 8. And whichever the code, we need to make sure we are addressing the specific requirements outlined in those construction codes.
Section 1 has Part PVG that discusses organic fluid vaporizers, so this is used in conjunction with the rest of Part PG and addresses those heaters where we are vaporizing fluid. And Part PVG also has very specific rules for safety valves, gauge glasses, and drain valves. Now, liquid phase thermal fluid heaters (anyone who sits with me on the Subgroup of General Requirements are groaning as they listen to me now), because Section 1 has this little paragraph where it talks about liquid phase thermal fluid heaters meeting applicable requirements of Section 1, but it doesn't really clearly identify those requirements. There is an open item in progress to define those rules so that when there are jurisdictions that want Section 1 or customers that are requiring Section 1, we have clearly defined rules to meet those requirements.
You can also build thermal fluid heaters to Section 8, Division 1. There is Paragraph UW-2(d) for pressure vessels subject to direct firing, and there are a few caveats in there about the types of welds to use and thicknesses and whether or not postweld heat treatment might be required, and then also to make sure that the manufacturer's data report is noted with the DF for direct firing and it is included in the special service requirements. So Section 8 gave a little more definition to what was required, but didn't really again cover the other things that make some of these products unique. Safety relief valves in Section 8 are left to the user generally, but there are some basic guidelines – for example, based on API 520 for safety relief valves – that is a common practice for a lot of people. You look at the flow of fluid through the heater, the operating temperature, the properties of the fluid itself, and the set pressure to help size that safety relief valve.
Inspectors are probably all very familiar with CSD-1. That's our controls and safety devices for automatically-fired boilers. It covers power boilers and heating boilers with inputs less than 12.5 million BTUs. It covers requirements for combustion controls as well as steam and waterside controls including pressure, temperature, and water level. With the current standard, questions exist as to whether or not this covers hot oil heaters (because the combustion side all applies; the steam and hot water doesn't really apply, so what do we do?). Because you could have a small manufacturing plant that has a 4-million BTU thermal fluid heater sitting in the boiler room next to the steam boiler (or whatever else they are using for their process). So inspectors, states, and jurisdictions have called and said, “what do we do with this?” Well, there is a task group and CSD-1 is looking at this to see if there should be an appendix that at least covers the controls that are specific to hot oil heaters to give inspectors and users some additional guidance.
And then we have the National Fire Protection Agency. Large boilers are covered by NFPA 85; ovens are covered by NFPA 86, but once you got beyond the combustion controls and some of the other installation considerations for those boilers, there wasn’t a lot of information applicable to hot oil heaters. So NFPA 87 was developed. It's currently a recommended practice, eventually it may be an actual standard, but it's going to cover things consistent with what you would find in NFPA 85: things like location construction, heating systems, commissioning operations, maintenance, inspection and testing; but then it's going to get chapter specific for thermal fluid heaters and then with fire protection.
I wasn't the one who started all of this, although I think a couple of you may hold me personally responsible for pain and suffering, but what I am trying to do (because I do have experience) is go to these meetings and work on the codes and at least try to make sure there is consistency as we are putting information out there. Because one of the struggles we have in the world of Section 4 is we always have trouble with things that are conflicting between CSD-1 Section 4 and the NBIC, and I don't want to see that happen on these thermal fluid heaters. I'm trying to help Section 4 and everybody work on their issues, but in this case if we can be consistent from the start, it will be a lot less confusing to both the users and anybody trying to inspect the equipment to make sure that it's operating as intended and safely.
In conclusion, thermal fluid heaters are more common than you think, at least as far as their applications, and the key is for obtaining high temperatures with low system pressures. Some of the key safety and design considerations include the fluid selection, the flow through the heater, and temperature control. And there are a variety of codes and standards under development to provide additional guidance. Thank you very much for your time.