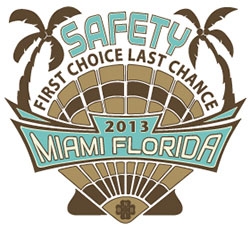
82nd General Meeting Speaker Presentation
MANUAL WELD EXAMINATION USING PHASED ARRAY ULTRASONIC TESTING (PAUT)
By Ron Kent
The following presentation was delivered at the 82nd General Meeting Monday morning session, May 13, by Ron Kent. It has been edited for content and phrasing. To follow along with Mr. Kent’s slide presentation, click here. Some sections in the following text reference the title of the corresponding slide to assist in following the slide presentation.
Introduction:
Mr. Ron Kent has more than 25 years of experience in military and civilian fields of material testing using NDT methods. He is qualified and certified as an ASNT Level III examiner in the PT, UT, MT, RT and ET examination methods. His background also includes working on a wide variety of technical projects including the U.S. Air Force Nondestructive Program. Other projects include research and development, NDT engineering, design and application of NDT tools and fixtures, weld quality, mechanical integrity testing, and product quality. Mr. Kent founded KB Inspection Services in 2008 and now serves as the company's president. KB Inspection Services operates four field service NDT offices within the USA.
His 82nd General Meeting presentation addressed a subject that concerns many in the pressure equipment industry: manual weld examination using phased array ultrasonic testing, or PAUT.
Ron Kent:
Thank you for having me. This presentation starts with the KB Inspection Services (KB) mission statement. I worked for many different firms before I started the KB Inspection Group. Our mission statement drives the behavior for why we do phased array: weld quality.
We have to provide a quality and affordable test or examination technique for many different customers trying to meet mechanical integrity criteria. And to that end, weld quality is a big part of that service. We have customers from all spectrums of business: from aircraft to industrial and of course, power plants are a big part of the business and the one that ties in the most with this group. We do a lot of work on the fossil side of the power plant business versus nuclear.
KB has implemented the phased array weld quality equipment for five plus years. The equipment, technology, and method have been around much longer than that. Affordability is the factor that is driving the recent switch from x-ray technology on welds to phased array testing. We do a lot of in-situ welds in the field (not in a shop) in the industrial plant or in the power plant, and up to a few years ago it was not affordable to take a phased array instrument to that environment.
The vendors who make the equipment have made this possible. The GEs and Olympuses of the world have created tools that now allow you to do phased array imaging on a weld where you would normally do an x-ray test. I know a lot of you have dealt with this issue for many years and you probably have a lot of experience with the ultrasonic shear wave technology that was used for the last 50 years. The difference is that now we can create imaging versus a single pip on a screen as seen with traditional UT.
Phased Array vs. X-Ray: This is a postcard we send out, but it really tells the story. We have an instrument on the left, which is a modern Olympus-made instrument that is replacing the x-ray image on the right. The weld is the same in the middle, and the field test of it has just shifted from one to the other.
Concepts of Phased Array Technology: We get compared a lot to traditional UT, and this slide was developed to compare the single-crystal approach on the left to the multiple-crystal approach on the right. Of course, the multiple-crystal approach is going to give us ability to create an image, which is something you intuitively want to see.
What is a Phased Array Transducer?: Here is another illustration of a standard one-element probe on the top creating a single pulse of waves, versus phased array being the stack of elements and when those elements fire and create the sound energy.
The Basic Approach: This is a field contact test method. We would have a person holding a probe (or a fixture or a device holding a probe) adjacent to the weld scanning along the weld axis. It all starts with a plan – in this case, it is under the guidance of ASME.
The Scan Plan Design: Here is a very elementary single V illustration (single group weld). The scan plan design that has to be developed in order to implement this technique in the field covers all the zones of concern. If you were to follow the very confusing lines, you would see there are zones for the side weld of the probe side of the bevel, there is a zone for the root, and there is a general area of the body of the weld zone. And then there are other scans that would cover the heat-affected zone for cracking or for delaminations.
But this design is the primary focus of today's illustration. Of course, it can get very complex if you change the weld fit-up geometry, but we are going to go over the simple standard weld. This is a computer-generated model of that same fit-up, and this would be what we would present to a customer to show them that we have coverage of the weld for the discontinuities they expect to see. This is a real size, showing the part thickness on the left, over half an inch.
Next is the probe placement: how far from the center line of the weld the probe is placed and the sound exits and enters the part. And then the actual beautiful part about this -- this is a very typical scan -- is we are relying on a second leg, a refraction off the ID of the pipe weld. Let's use a pipe as an example. That second leg allows an equal refraction through the material that we are interested in. Keep that in mind as we go forward, because the instrument does not know that the sound refracted.
My goal is to let you know as inspectors, when you are reviewing the NDT data or the NDE data, how to look over their shoulder and be comfortable with the screen presentation that exists today. The instruments are capable of fully recording the data, and it does get oversight by QA usually at the owner's discretion. You would also have the opportunity to view this data post the examination, which is what you are used to when you are looking at a radiograph.
Scan Plan – to – Instrument Display: There are many screen presentations, but this is the one I would like you to focus on when you review weld quality. This screen shot may be familiar to you because it's used in medical a lot. We happen to tilt it on the side where in medical they use it straight down. But you are very comfortable if you look at this view and just think of it as where it places on the weld. I overlaid it right where the sound enters the part from the probe, and then of course the instrument didn’t know that it refracted.
PAUT Applied: Here is an image of a technician actually putting the probe on a nozzle in a chemical plant. And the middle picture is a device that's made by Olympus, and look at the profile of this device. It takes the scan of this weld from both sides at one time. And you recognize that as a boiler tube in a furnace, and it's going through an opening that's a half inch in width. The tools they are making are for the applications we are up against, which are not always friendly for your probes and equipment.
PAUT Interpretation: Back to the weld scan: the screen is placed over the weld like this. So when you see the screen, you are going to see this, and you are going to see a bottom reference line because the operator knows where he places it, and then you will see a top reference line for the sound returning to the top piece. And the reason it's in this order is the sound on the screen actually is viewed like that.
Once you get used to this concept of viewing the data, you will be just as comfortable seeing the discontinuities and the flaws in this weld as when reviewing a radiograph. And that would be your goal as an inspector if you are reviewing the examination reports. You would want to be comfortable with where the center line of the weld is, which is indicated on the screen. You would want to know where the ID of the pipe is, which is illustrated on the screen, and then you would want to know where the OD of the pipe is.
Now let's place the weld into view. As you can see, it's as simple as taking this layer here and folding it up, and it would be geometrically correct. There are instruments that are coming in the next generation of this model that will do that for us, but today the operators are trained to separate that weld in legs, and that second leg is flipped, inversed. Because again the ultrasound and the detector and the probe and the circuitry do not know that the sound actually refracted off the ID. It only knows that it's traveled a certain distance at a certain angle and a certain amount of energy returned.
Advantages of Implementing PAUT: The advantages of implementing the phased array UT are obvious. The elimination of the x-ray is the biggest driver in our business, and this is for two reasons. One is the hazard itself of having radiation sources on site. That has always been a nightmare to manage. It has shut down job production and it's delayed the welding work at hand. But the thing that's changed with this offset is that regulation of radiation material is a lot different today after the 9/11 world. It takes a lot more effort and money to get a source on your site to do your work.
The second reason is that there is no trade-off on the quality. You will hear this debated in our field, and of course it needs to be, and it needs to be vetted out over many years and many studies. I think you will hear arguments that it has improved the quality detection based on all the factors. I'm sure we could get into lively debates on that if you choose. And then flaw characterization is another advantage. With an x-ray you really can't tell the depth of an item, but with a phased array side view, if you will, depth is one of its biggest strengths. It will tell you not only where the defect is front and side-to-side, but it will tell you the depth. And they are real-time results.
Imagine a foreman with fifteen crews of welders trying to get work done on a schedule. We are not offsetting them with windows for radiation hazard. We are working as the weld cools. We are real-time inspecting. Think about that from a practical standpoint. They don't have to restage equipment to do the repair work. We are right behind them in real-time. We get recordable results. This is what every QA person, every owner, and every inspector, I'm sure, would want. You would want to know that the techniques are proven and that you have an opportunity to look at the results, which is what x-ray has done for you for years. You have that now with the instruments available.
Value 2: Good Quality-Improved POD: Let’s look at the POD improvement and the probability of detection. This slide is provided by a vendor, GE. The point it's trying to make is if you are comparing phased array to traditional, you will see that defects show up at angles not fixed. In this case it showed up better at 50 degrees than it did at 45. And at 70, it didn't show up at all. If you were applying shear wave in the past, you know that you are on fixed angles, 45, 60 and 70 normally, and this is showing you that with the spectrum of 45 and every degree from there to 75, you have a probability of detection increase based on the fact that at some angle that discontinuity reflects better than others.
Improved Precision: This is the illustration of measuring the depth we have talked about. It is a quick shot, showing that you can actually measure the side profile of that side drill hole, which would be no different than measuring the side profile of a piece of porosity in your weld. So showing you the height of a piece of porosity, and then of course we can give you the length of it, because as the probe moves, it is being measured. We always have been able to do that, but the depth is the new tool that we have.
Video: Here is a quick video showing the Cobra device being put on a small tube. It's very thin, and on that tube there is an OD and ID drilled hole. The hole is the size you couldn't accept on radiograph for a random piece of porosity. I want you to look at the screen as he's talking, and you will see the OD and the ID hole as I laid it out for you.
Video narration: KB Inspection Services utilizes an ID/OD hole. Here is the OD, and an ID hole, representative of the single four porosity limits to ASME for acceptability. Also utilizes the OD/ID notch system when necessary. Represented on the screen are two channels using the Cobra system – thickness of this standard is 210– representing the ID/OD hole looking from both sides of the indication or weld in the field. (End of video.)
MR. KENT: I know that was brief and probably confusing, but the point is that standard was like two hundred thousandths thick and we were detecting holes on the ID and OD stacked on top of each other that were at a quarter T apiece. So that would put them at fifty thousandths, and we were able to separate them and see them visibly independently. That shows you the sensitivity level. And we are on a very thin piece, which is our worst case. The thicker the piece, the easier the separation. So I hope you got the intended value, which was the fact that this thing is very sensitive, very repeatable, and very reliable on small discontinuities.
Flaw Characterization Depth Determination: The rulers are right on the screen. If the probe is sitting here, there is a ruler to measure forward and depth to the indication on the screen. You could do this and review it just like a technician could. Again, another vendor provided this slide. It's obviously faster to inspect this way than to do radiographs. This is important to your group because you are probably going to have owners driving toward this test methodology and you are going to be the ones that are brought into that fold, if you haven't been already. So where traditionally they have shot with x-ray, they are probably going to ask you to switch technologies.
No Schedule Delays: And then of course, there are no scheduled delays. We are not talking about the schedule for the NDE. We are talking about the schedule for the project and reducing the reject rate. Because when you are real-time inspecting behind a production weld job, they know there is a process problem. We find it quickly because we are right behind them testing, versus if you were x-raying it could be a shift or two later when they determine a problem, because they have got to build an x-ray window in there to do the test.
And then, of course, a picture is worth a thousand words. As long as you can become comfortable as an inspector evaluating this image as if you had been doing x-ray all these years, you will be as comfortable as we are implementing this technology with your customers.
There will always be new applications as the equipment gets better. There are a lot of exceptions to the rule. We talked about a really simple fit-up of a single-bevel V weld. We obviously deal with many more complex situations in the field, and the vendors are getting very good with the instruments, training, and equipment to help us meet some of those needs.
We utilize the equipment to try to do a weld test, but it's obviously improved probability detection, faster inspection, and sizing improvements over what we have been doing before. There is good online video training to where you can become comfortable interpreting the screen shots in a few hours (or the real data as you review the recordings). I want you as inspectors to become familiar with it. We are going to see you on the job and we will help you with this issue as well.
Question and Answer
AUDIENCE MEMBER: I get the impression that when you use a single crystal probe that you would move in and out to a level, and with phased array you just set it in one position and move parallel to a weld, you don't actually approach the filled weld?
MR. KENT: That is correct. The indexing (the rastering back and forth from the weld) in the traditional sense is gone. The scan plan is done from a fixed location and linear scans going around the weld -- parallel to the weld. Obviously, as the weld gets thicker or if it gets more complex in the weld fit-up, there would be multiple scans. But they would still be done from a fixed location to cover a zone of the weld.
AUDIENCE MEMBER: Have there been improvements with regards to sizing, rounded indications, and small diameter thin wall?
MR. KENT: Right, which is the Achilles' heel of UT, because a rounded indication is a perfect reflector. It's the hardest thing to see, where with radiography it's very easy to see. There have been no improvements because you can't change the physics of that, but the improvements come from the technique improvement. In other words, you saw a video of our fellow hitting a small rounded hole in the standard versus ASME's notches. That was put in there for a reason, because we had missed porosity on a project and x-ray found it. So we learned the lesson to put a rounded indication in our standard block and adjust our sensitivity to it.
In UT terminology, it's very easy to see a corner notch, so the ASME standard curve block is very easy to see the 7 to 11 percent notch. It's very difficult to see that same size rounded indication. You have to put it in the standard in order to adjust the instrument properly. The improvements happen in the technique.
AUDIENCE MEMBER: How much thin tungsten inclusions would that show?
MR. KENT: Only if there was a void between the base metal and the inclusion. There would actually have to be a void there to have any reflection factor that you are going to see. If it's fused or there is no void nonmetal item, you probably are not going to see it. That's one of the downsides to it.
AUDIENCE MEMBER: Does the pulp and paper mill industry accept this in lieu of x-ray in recovery boilers, backup boilers?
MR. KENT: Yes, sir. They were one of the early adopters obviously for economic reasons.
AUDIENCE MEMBER: Each of the crystals, are they slightly different, the frequency at which they transmit?
MR. KENT: Yes. The frequency selection process really hasn't changed. You need to do that analysis depending on what you are expecting to find. Although, the probability of detection has increased because of the multiple angles that you are hitting at, but it really doesn't change the fact that you need to be about a half a wave length or bigger in order for it to be a reliable test method.
AUDIENCE MEMBER: Then that means each crystal is slightly different, and that gives you the ability to maybe see a shadow whereas the other one may not see a shadow?
MR. KENT: Right. That was the standard traditional way of determining wave length, and now you have a probe with an array of elements and you have the ability to only use the ones you want. So if you wanted a smaller starting point, you would use less of the elements in that technique. But to your point, the elements are very small to start off with. So we usually do not have a frequency problem or a wave length problem with phased array for weld qualities.
AUDIENCE MEMBER: How about the productivity like weld-to-weld and the equipment availability? Say if you were doing an outage and you had 20 to 30 welds that you came for.
MR. KENT: That's a two-stage question. One is an x-ray environment; you are limited to a window, usually a four-hour window, so you obviously are not going to get a lot of production. But in UT you have the full shift to work. In a direct comparison within those four hours, it's a 50 percent type of increase in inspection numbers per hour.
MR. BERGER: My name is Dave Berger and I work for a generation company who has used different permutations of phased array examination for different things. One thing that is not well communicated is that what you are talking about today is primarily phased array -- linear phased array ultrasonics. There are other permutations where you use a matrix or you use an annular phased array, and those are aimed at different purposes than what you are doing.
MR. KENT: Yes, sir.
MR. BERGER: You are talking about general weld inspection. One of the reasons we embrace that very clearly is that you don't have the radiographic exclusion zone to contend with that shuts down work in the cases where you would need cobalt for quite some distance.
MR. KENT: The biggest driver.
MR. BERGER: So that is a big driver. But the point that we like about it is that the phased array ultrasonics, linear phased array in many cases, is capable of detecting the flaws that are more of interest.
MR. KENT: Absolutely.
MR. BERGER: Because from a fitness for service point of view, the ones that come up and bite you tend to be the plantar flaws that ultrasonics is particularly good at detecting. The volumetric flaws aren't such a big deal in most cases unless it's gross slugging or really poor conditions.
MR. KENT: It's seen a lot of volume, right.
MR. BERGER: A couple pores don't cause weld failures. Things that are plantar flaws that escape radiographic detection, those are the ones that are going to hurt you.
MR. KENT: Yes. It's unfortunate that x-ray examination didn't get the same scrutiny that phased array does, because you are correct, phased array would outperform radiographic technique in probably 80, 90 percent of the time, and the rounded indication is the Achilles' heel of the UT.
MR. BERGER: They both meet codes and standards –
MR. KENT: Yes.
MR. BERGER: -- but one method won't disclose exactly the same results as the other.
MR. KENT: Right.
MR. BERGER: The point is that they are both very effective and –
MR. KENT: Reliable.
MR. BERGER: -- in any given flaw, one may outperform the other.
MR. KENT: And there are cases for both. We do x-ray as well. We are not trying to offset the x-ray business. We are here to speak about the shifting trends of the business. We notice it because it becomes a manpower equipment issue on our side, so it's been hard to keep up the shift from a provider of the service. And of course, on most of our jobs, we are dealing with an AI ultimately when they are in on a review for the owner, so we get to do these education one-on-ones with inspectors in the field to get them comfortable with evaluating data from phased array UT versus a piece of film.