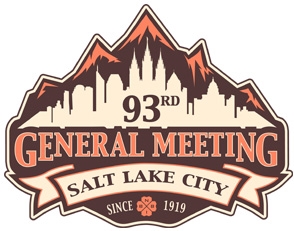
93rd General Meeting Presentation
Boiler Inspections - An Evolving Responsibility
Rodger Adams and Tom Clark
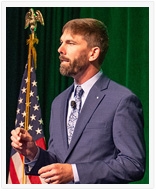
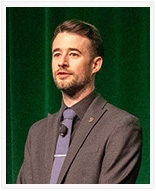
The following remarks were delivered at the General Session of the 93rd General Meeting on May 12, 2025. It has been edited for content and phrasing.
INTRODUCTION: Rodger Adams is the South Region Manager of Machinery Breakdown Risk Engineering with Zurich Insurance. He is also an NBIC Subgroup Installation member.
Tom Clark is the chief boiler inspector for the state of Oregon and is a member at large on the NBBI Board of Trustees, chair of NBBI’s Committee on Qualifications for Inspection, and a member of NBIC Subgroup and Subcommittee Installation.
Their slide presentation can be found here.
MR. ADAMS: Welcome back. Who's ready to recite some code? According to National Board Inspection Code (NBIC) Part 2, Inspection, Section I, 1.1 Scope, "The safety of the public and the inspector is the most important aspect of any inspection activity."
What do we do when the safety of the public or an inspector is jeopardized? Whose responsibility is it to ensure that an owner understands the hazards of their pressure equipment or an operator understands how to operate their equipment safely and effectively? What do we do as an industry when faced with a lack of skilled labor? Our responsibility extends, as the code might say, beyond the boiler property.
MR. CLARK: One of the great strengths of our industry is its amazing diversity of backgrounds, skills, and levels of education. However, as you'll see in this presentation, this strength can also be a weakness at times.
That diversity applies to the two of us here as well. Rodger Adams was a Special Forces Operator, and I, of course, was an MMA fighter. No, just kidding. That was our keynote (Tim Kennedy).
Rodger came from the world of academia, and my background is in the U.S. Navy's nuclear power program. But despite those two very different starting points, our paths converged as inspector supervisors, trainers, and presenters here today. I know you've just come from lunch, so before the food coma sets in, we're going to do something to help you wake up. We're going to do a live poll.
We will have you stand up if you represent a member jurisdiction, an AIA, a manufacturer, or a repair organization. Should be most of you, right?
MR. ADAMS: Now, listen closely. Please sit down if you can retire within 10 years. Not if you will, but if you can retire in the next 10 years. Look around the room. All of us in this room have a responsibility to transfer our knowledge to those left standing to maintain the mission of promoting greater safety for life and property. You can be seated now.
MR. CLARK: OK, but don't get comfortable, because we're going to do this one more time. Now, I would like you to please rise if your job or job title is that of a boiler operator.
MR. ADAMS: Maybe we should rephrase the question. Please stand up if you have a boiler operator or a stationary engineer license. Again, take a look around the room. Make a mental note of these observations. We'll come back to them later in our presentation. You can be seated.
MR. CLARK: Well, if the exercise didn't wake you up, maybe the photos on the screen will. I took these during an accident investigation in August of 2022. And while I could spend the rest of the afternoon discussing this incident, I'll try to keep it brief.
What happened here is the result of an accident that started months before when a rental thermal fluid heater was installed indoors at a food processing facility. And throughout the installation and the brief period of operation of this piece of equipment, everything that could go wrong did go wrong. It was primarily due to a lack of knowledge and understanding of the system on the part of those who installed it and those who operated it.
A few examples of this would be the fact that the temporary piping that was installed to connect this rental unit to the existing kettles was hydrostatically tested instead of pneumatically tested, despite thermal fluid incompatibility with water and even though there were no low-point drains or high-point vents to allow them to get the water back out of the system.
The system was operated over pressure multiple times. They exceeded the maximum allowable working pressure of the expansion tank by something like 50%. They forgot to install bypass valves around the kettle, so they deadheaded the pump against the kettle. After they made that mistake, they went back in and installed a bypass valve. However, during the investigation, we discovered that the bypass valve had been installed backward.
All these factors, unfortunately, led to part of that temporary piping failing. A vapor cloud of thermal fluid was released and found an ignition source. And as one witness described: It went up like napalm. Instantly, a facility was destroyed. Fortunately, there were no fatalities, but there could have been. Seven were injured, and 300 people were out of a job.
If the people who installed and subsequently operated this equipment had understood the complexity of what they were working with and the risks they were dealing with, would this have happened?
There's another incident I'd like to discuss, although I don't have as dramatic and flashy photos for it. Another rental unit – we're seeing a trend here – this time, a power steam boiler was installed at another food processing facility to provide coverage while the existing boiler was down for routine inspections.
However, the operators at that food processing plant weren't given very good training on the equipment they were renting, so they were not prepared when they experienced, and I'm not joking, 100 low-water cutoff alarms. One hundred! That, of course, led them to think there might be issues with the feed tank, and they got distracted by that, which prevented them from realizing that they had another problem. Sludge was building up in the boiler, and building up fast. So when that 101st alarm was supposed to go off, it didn't. The boiler ran dry. The Morrison tube melted, and the boiler was a total loss.
Fortunately, the operators weren't present with the boiler, despite the fact that the law requires them to attend the boiler at all times, so they weren’t killed. But if they had been trained on how to operate boiler systems properly, would they have realized that the boiler should not have experienced that many alarms while in operation? Perhaps we could have saved thatequipment.
These two incidents may seem like extreme one-offs, but as Rodger is about to show you, incidents driven by operator error are all too common.
MR. ADAMS: Tragically, 127 people lost their lives as a result of boiler and pressure vessel accidents between 1992 and 2002. I would encourage you to reference the eye-opening feature in the summer 2002 edition of the National Board’s BULLETIN titled “10 Years of Incident Reports Underscore Human Error As the Primary Cause of Accidents.”
Of 23,338 accidents reported during that referenced 10-year period, 83% were a direct result of human oversight or a lack of knowledge. This includes low-water conditions, improper installation, improper repair, operator error, or poor maintenance. Of those 23,338 accidents, human oversight and a lack of knowledge were responsible for 69% of the injuries and 60% of the recorded deaths.
When we look at equipment categories, unfired pressure vessels proved to be the deadliest by far, with 64 persons killed by unfired pressure vessels during that 10-year period. This was followed by power boilers, water-heating boilers, and steam-heating boilers. Yet in a peculiar twist, this order is reversed when it comes to the number of accidents reported during that 10-year period, with steam-heating boilers leading the way with over 9,500 accidents, followed by water-heating boilers, power boilers, and unfired pressure vessels.
Former National Board Executive Director Don Tanner wrote an article in the summer 2002 BULLETIN titled “The Big Picture.” This article contains information compiled by National Board Jurisdiction Authorities and Authorized Inspection Agencies, including the 2001 incident report.
The 2001 incident report showed that 80% of the accidents were directly related to low-water conditions and operator error. With 90% of the deaths recorded in 2001 attributed to operator error, our objective should be increasingly clear: to embrace training as the most important and effective means of reducing accidents, injuries, and deaths.
We must do more to inform the general public so that those working on or around boilers have the essential knowledge necessary to protect themselves as well as those around them, Tom.
MR. CLARK: That's right, Rodger. Although that data is somewhat dated, our findings in the state of Oregon tell a similar story. In the last 10 years, Oregon has documented 28 accidents, and 12 of them were directly driven by operator error alone.
Obviously, in an ideal world, we would have no incidents due to operator error. In a world where we have an adequate number of suitably trained operators, we would have very few operator error incidents, but based on the statistics we just shared, I don't think we live in that world. That leads to the question: Do we have the adequate number of skilled operators that we need?
MR. ADAMS: According to a study by Deloitte and the Manufacturing Institute, the manufacturing skills gap in the U.S. could result in 2.1 million unfilled jobs by 2030. The skilled welder who can handle multiple welding methods has suddenly become a scarce commodity. The demand for skilled welders outpaces the supply, and this trend is expected to continue unabated.
Can anyone guess the primary reason for these labor shortages? Over half of all skilled trades workers are age 45 or older. We witnessed something similar at the beginning of our presentation when the majority of you sat down, indicating that you can retire within the next 10 years.
Similar to the welding industry, one of the biggest challenges in the electrical industry is a lack of labor. In today's rapidly evolving industrial landscape, the role of maintenance technicians is more critical than ever. Yet the retirement of experienced Baby Boomers has left a void that the incoming workforce struggles to fill. As technology advances, the skills required of maintenance technicians have evolved, leading to a growing skills gap.
Now, the boiler industry continues to expand with the market, seeing steady growth in recent years. According to Market Research 365, the commercial boiler market will grow 6.8% from its current estimated value of $11.8 billion to $29.3 billion by 2035. This rapid growth is partially attributable to decarbonization initiatives in the U.S. Accompanying these initiatives is the development of high-efficiency gas and electric boiler technology. According to the U.S. Department of Labor Bureau of Statistics, most large buildings and facilities possess large heating, ventilation and air-conditioning equipment. And as many of us are familiar, industrial plants typically possess facilities to generate power, steam, and other services.
MR. CLARK: And in order to operate that equipment, of course, we need boiler operators. We need power engineers. We need stationary engineers. You know what a stationary engineer is, right, Rodger?
MR. ADAMS: Yeah, they sit at their desk, right?
MR. CLARK: No, that's all engineers. No, just kidding. Stationary engineers, of course, are another type of boiler operator often regulated and licensed by a jurisdiction, but as we'll see, sometimes not. Boiler operators are expected to see an employment growth of about 4% by 2033, but when compared to the industry growth of 6.8% that Rodger just shared, a clear gap is evident.
One jurisdiction that we examined while preparing for this presentation has 450 locations that, by law, require a stationary engineer to operate, but unfortunately, only 30% of those locations actually have them.
We're seeing a shortage of operators, but their jobs are becoming even more complex. We're now seeing building management systems, remote operations, and more complex boilers. How many of you have inspected or installed a boiler with a touch screen? How many of you thought that made it easier to inspect or operate? We continue to face growing challenges, so in that case, what are we doing about it?
One thing we have been doing as an industry is training inspectors to train operators. I think as an organization, the National Board has done an awesome job of doing that. There are so many resources available to inspectors. On the website, there are inspectors' guides and topics of interest that inspectors can read about specific types of equipment.
Recently, the training team of the National Board released the instructor-led virtual Boiler and Pressure Vessel Fundamentals Seminar, which has been a huge hit. On the business center website (nbbi.org), the installers series of self-guided training courses is available. And near and dear to my heart, of course, for our new generation of inspectors who may not have the same background that we all do, we have the NB-380 Inservice Inspector Training Program, which provides them with the strong start they need.
But, it doesn't stop there. We also have, of course, the NBIC. And while we have traditionally focused on installation, inspection, repair, and alteration, we have started to consider some items that are more typically considered operational. Rodger and I serve on NBIC Part 1, Installation. We are currently reviewing an item related to a boil-out for new boilers. The committee debated this back and forth, saying, “Well, that's more traditionally an operational item.”
The manufacturer should drive it, but one of our committee members shared the thought that since we are running low on skilled operators and knowledgeable inspectors, we need to add things like this to the code for those who don't know.
MR. ADAMS: What are we doing with respect to Authorized Inspection Agencies? After conducting interviews with several AIAs, it was determined that we're providing a variety of informal and situational training to new inspector candidates. In fact, one AIA is revising the scope of their training program to fully integrate NB-380. But what are our AIAs doing for their external customers? How are our AIAs educating operators?
Most of our AIAs take a similar approach to training operators and provide instruction and guidance on site during the course of the annual external operating inspection. This might include demonstrating how to test a low-water cutout, how to blow down a water column or flame sensor or test the low-gas pressure switch.
When deficiencies are noted, our AIAs will write loss prevention recommendations for the insured or customer to obtain operator training. Many of our AIAs offer operator training. Some even do it at their customers' facilities or in their classrooms. One AIA took it a step further by providing on-site training in their customers’ boiler rooms.
Another AIA offers on-demand operator training, which is available to all policyholders. Many of our AIAs also distribute boiler log tags, similar to what you see on the screen, which note the scope and frequency of recommended tests, as well as a brief description of how to perform these tests. Yet the resounding response we receive from the AIAs is that, ultimately, it's the owner’s or operator's responsibility for the safe operation of their equipment, yet we mentor when and where we deem appropriate.
Now, these are the types of collaborative inspections that all commissioned inspectors should provide across all kinds of equipment; however, I think we could all agree that these were largely limited to high-pressure boilers. What about the steam-heating boilers, which we learned were the leading cause of accidents, with over 9,000 reported incidents between 1992 and 2002?
Many manufacturers, service organizations, and independent training organizations also offer online and in-person training, typically for a fee. They also distribute boiler logs and other literature similar to our AIAs documenting the scope and frequency of certain tests.
You may not be aware of some of the outstanding collaborations within our industry. The Wisconsin Boiler Inspector's Association (WBIA) is a nonprofit organization dedicated to promoting boiler and pressure vessel safety in all sectors of the population. And they've been doing so for over 34 years. Their membership consists of boiler inspectors from the state of Wisconsin, the city of Milwaukee, and insurance companies, as well as boiler manufacturers, boiler repair companies, safety valve manufacturers and manufacturers' representatives, owners and operators, and others concerned about the safe and efficient operation of boilers and pressure vessels.
The WBIA hosts an annual meeting in April called Industry Days, which provides a variety of continuing education credits, technical training, and presentations on boiler safety and other code-related items. Can we replicate the success elsewhere?
Several jurisdictions have posted in-person meetings providing similar training. And they've even invited boiler, burner and controls manufacturers, water treatment representatives, and local boiler repair and service organizations, but are these meetings as frequent as they should be?
While the COVID-19 pandemic changed the way we work and budgets impact the ability to host in-person meetings, can we be doing more? Tom, I understand you hosted a meeting recently. What did you do?
MR. CLARK: I did. I worked with my neighbor, Mike Carlson, the chief from the state of Washington, to hold back-to-back meetings not just for our own inspectors, but also for our insurance industry partners. We had training provided, thank you very much, by the National Board, as well as some of our own staff and our industry partners, to help keep our inspectors up to date and aware of code changes. And while that was great, we didn't involve the rest of the industry. We didn't get owners and operators. Hopefully, one day we can do more. So that leads us to the question: What should we be doing about this lack of knowledge in our operators?
According to NBIC Part 2, Inspection, during any inspections or tests of pressure-retaining items, the actual operating and maintenance practices should be noted by the inspector and a determination made as to their acceptability. Is it up to the inspector to determine if it's acceptable? What do they base that on? It should be up to the jurisdiction, but as we have discovered, jurisdictions are incredibly inconsistent when it comes to requirements for boiler operators.
Out of these 73 jurisdictions we were able to find information on, 35 required some form of boiler operator licensing. That could be as simple as a standard operating license that has a single category for operators, up to jurisdictions that require five different levels of licensing, ranging from the basic operator to the chief engineer. Some of our members hold that chief engineer credential, and they're very proud of it, as they should be.
Some jurisdictions simply require boiler operators to be suitably trained. Some jurisdictions, like mine, require them to be trained soon, but unfortunately, don't provide any further clarity than that. Some have more detailed requirements, and some have no requirements at all. And some of that may be because we don't have a lot of code documents to point to when it comes to operation.
Sure, we have ASME Section VI and VII, as you can on the screen, “Recommended Rules For the Care and Operation of Heating Boilers” and the “Recommended Guidelines For the Care of Power Boilers.” I don’t know why one is “rules” and one is “guidelines.” You'll have to ask our friends at ASME, but these are two great documents.
I have personally pointed customers to the maintenance logs and testing logs located in Section VI. However, the problem is that in my jurisdiction and many others, Section VI and Section VII are not adopted and are not mandatory, so they're not enforceable.
Without code guidance, without consistency across our jurisdictions, we have to ask, is our current non-mandatory guidelines enough?
MR. ADAMS: It's a great question, Tom. So I'll ask: Should guidelines be developed for operators, or should we as an industry look to develop guidance for the inspector? Do our inspectors effectively understand the basics of boiler operations?
At the beginning of our presentation, we witnessed a handful of folks in the room who stood up that had boiler operator or stationary engineer licenses, but do we have an opportunity to better educate our inspectors on basic operations? Maybe we need to provide training on effective communication. Can our inspectors effectively articulate verbal and written deficiencies?
We all understand that the owner and operator is responsible for the safe operation of their equipment, but do we have the duty as an inspection organization, as member jurisdictions, and Authorized Inspection Agencies, to better educate owners and operators through consultative inspections?
Can we work collaboratively with our industry partners and independent training organizations to develop optional modules on operations that a commissioned inspector can take as part of the National Board's annual continuing education requirements, or do we aim for the stars and look to prove operator competency in a manner similar to NB-380?
MR. CLARK: You know, clearly we're doing a lot, but there is more to do. And if we boil down, pun intended, the situation to its root, it really is that owners and operators just don't know what it is that they don't know. And I have an analogy that I love to use for this. Before you is the Ferrari 812 GTS. Its 6.5-liter V12 engine generates 788 horsepower and accelerates the car from zero to 60 in just 2.8 seconds. Most of us will never see this vehicle because of its eye-watering price tag of $430,000, but you know what we will encounter that costs about $430,000? A 400 horsepower packaged power boiler. Rodger, do you know the difference between the two?
MR. ADAMS: 388 horsepower.
MR. CLARK: Yes. But what I was thinking of is that when an executive goes to buy this Ferrari, they know exactly what they're getting into. They know that they need oil changes. They know they need tire rotations.
They know they need to buy leather driving gloves. But when they go to buy that power boiler, they have no idea of the training their staff needs, the maintenance the equipment will need, the inspections, and it leads them to ask ridiculous questions like, “Can I buy a different type of steam boiler that I don't have to blow down?”
We don't claim to have all the answers. I think we asked more questions today than we provided answers, but we're here to start the conversation. Great things are happening, but more is needed. Clearly, owners are not properly motivated to train their operators. We spoke with one training provider as we were preparing for this, and they shared the opinion that no one is holding boiler operators' feet to the fire. These companies only reach out to training organizations after they have a near miss, but if we, as an industry, can help better educate those owners and operators to teach them what they don't know, then maybe we can help them from becoming another statistic.
MR. ADAMS: The late Don Tanner stated in that summer 2002 BULLETIN article: “If you're like me, we share a certain sense of pride in what we're able to contribute to this very important industry, our industry. When all is said and done, none of us wants to be measured in terms of numbers or statistics or even incident reports. We want to be evaluated on how each of us, as individuals, has dedicated ourselves to protecting an unsuspecting public. Numbers reveal only what was. It is up to you to determine what will be. That, my friends, is not just the big picture. It's a window of opportunity.”
We leave you today with two questions. Are we doing enough?
MR. CLARK: And are you doing enough? Thank you.