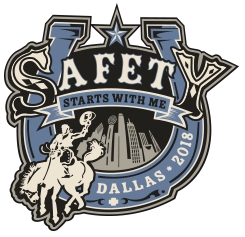
The 87th General Meeting Speaker Presentation
"Pressure Test Safety Awareness"
Anne Ehrmann
The following presentation was delivered at the 87th General Meeting Monday General Session, May 7, 2018. It has been edited for content and phrasing.
INTRODUCTION: Anne Ehrmann is the Director of Global Safety for the Hartford Steam Boiler Inspection and Insurance Company. Ms. Ehrmann has twenty years of experience as an industrial safety professional. Highlights of Anne's career include a global safety program that addressed hazards associated with boiler and pressure vessel inspection activities at manufacturing, construction, and repair facilities. She has also implemented safety awareness programs on pressure testing, radiography, and fatigue risk management.
Ms. Ehrmann's slide presentation can be accessed here.
MS. EHRMANN: Good afternoon, everyone. I am here to present on pressure test safety and awareness, not a curious topic we will be talking about this afternoon.
I work for Hartford Steam Boiler Inspection and Insurance Company, Global Inspection Agency, and as I said, we witness hydrostatic and pneumatic pressure tests every day as part of our job.
As you can see from the chart that I have presented here, pressure test near-misses is a global concern that we cannot ignore as a global entity for our organization. How can we as authorized inspection agencies protect our inspectors when we don't control the location where the tests are taking place?
How do we address the risk?
The first thing that we did was we empowered our inspectors to stop work and step away if they ever feel that their safety is in danger or their well-being is in danger.
The second thing we did was we listened to our inspectors. My team and I travelled to all of our company inspectors’ meetings around the world, and we talked to our inspection staff directly about the issues that they were facing, and they told us the hazards and matters of concern.
Then, of course, we also did our research. We reviewed the regulatory requirements, industry guidance documents, a lot of incidents history, and a lot of technical analysis as well.
We put all that information together, and we created a pressure testing program for our organization, and we augmented our training so that we can increase awareness of our inspectors and prevent injuries or, worse, death.
Something that we also put together in regard to our research was failure to maintain test fittings. What we found was that many of our clients use test fittings over and over again, which is fine, but there was no preventive maintenance plan in place to take them out of service. Unfortunately, they used them until they went bad.
Another thing we found was the failure to use the correct number and size of temporary closures and fittings. And with that, in some cases in a test, they don't have to use the full number and the proper size, but that can be a great mistake.
Another issue was failure to stand back and away from the equipment while the pressure was being increased. If something is going to happen, it's most likely going to happen at this time. Failure of installed safety restraints to contain fittings and equipment can become projectiles. So nobody is looking at these restraints. The restraints need to be strong to hold to that test pressure as well. There was one case wherein a pneumatic test failed and went right through the test lid and landed thirty feet away. And when we looked at the situation, the test was actually chicken wire. So how was that supposed to hold at test pressure?
Improper thread engagement—all threads of a bolt have to be engaged with the nut. If it's worn down, then there is a really good chance it's going to fail.
Failure to maintain the pressure test rig or the setup—a lot of times when they are doing a pressure test, they are looking at the equipment that's being tested, but they are not actually looking at the rig being used over and over again. That rig needs to be checked to make sure that it's adequate for the pressure test.
Failure to verify the test pressure is accurate for the current test.
Failure to follow the applicable code regarding the test temperatures and water temperature.
Failure to stop the test and reduce the pressure prior to approaching the vessel to determine where the leak is.
We also put together a pressure test best practice document, and we started off with just some general requirements. The first is to review the test procedure. If there is no test procedure, one needs to be created immediately. If they've used the same test procedure for the last fifteen years, then you need to give them some time to write down a new test. And that test procedure should include the roles of all the test personnel involved.
It should also include any deviation, what happens if a deviation occurs. For instance, what if you disconnect a part during the test? Maybe most of us know that's very dangerous, but maybe not the 18-year-old operator who was just hired.
You should also review the piping and instrument diagrams and the valve open/close procedures, because you don't want to leave something that's broken or stuck because it could lead to failure.
Remember the purpose of the test. You are checking for gross defects in design, materials or fabrication, and you are verifying that there is no leakage in the welds or permanent mechanical joints, right? You are looking for failure.
If you are looking for failure, you need to be aware of the hazards. You cannot become complacent. You need to watch for ruptures, for release of permanent or temporary closures, fluid jets or other hazards.
Conduct a risk assessment. Do the "what if" technique. Say what if this valve failed? What if this restriction doesn't hold? You are looking at the whole setup when you are conducting a pressure test.
Include methods of protection from overpressurization, such as use of a pressure relief valve or pressure regulating valve. And if you do use a pressure relief valve, make sure the discharge is less than it can carry because we don't want that to injure the person who uses it.
Implement a change management program. Change management is really important. You want to review each step of your procedure if you start changing things. What if you change the test pressure, the test temperature, the test medium, the fittings that you are using, the size of the temporary fitting, the size of the closures, the valves, the vessels? All of these, you need to take each step and look what could happen if you change this, what's the effect going to be.
And then you need to train everybody involved in the test, you need to train them on the procedure, on the awareness of the hazards associated with the test, and what that danger zone is that surrounds the test.
In putting the pressure test best practices together, we continue with the general requirements. We need to verify that the test location is safe enough and remote enough to conduct the test so that the risk to you is mitigated. So you want to utilize an adequate test bay wherever possible, and you want to verify safe egress is available in the event of an emergency. Whenever possible, pressure needs to be controlled from a safe distance.
Recognizing that pneumatic tests present significantly higher risks due to the stored energy, it should only be conducted if a hydrostatic test cannot be done. And you need to understand that it's going to require additional physical safeguards and procedures because it's more difficult to identify the leak.
Pressure test failures can result in all these things. They can result in ruptures and the release of permanent and temporary closures and the ejection of shrapnel. It can produce projectiles and fluid jets. Fluid jets are fine streams of liquid that can be injected into your skin. It only takes a 100 psi/7 bar for that water, that fluid to get injected into your skin. Any of these things can result in death or serious injury.
So before the test, you want to verify that the pressure test calculations are accurate.
Secondly, you make sure those calculations are adequately accurate for the test about to be performed.
You want to verify that all valves, fittings and flanges are properly rated for the test pressure.
You want to ensure that there is a preventative maintenance plan in place for any issues in test fittings, your hoses, your bolts, your bolting. You want to include a recording of each time you use it and a replacement schedule. You want to also have the test criteria that you looked at, it needs to be inspected before use, and there has to be specified criteria that would take it out of service. You don't want to wait for it to fail if the threads are worn or there is cracking evident.
Check that all connections and piping in nearby equipment are secure and restrained from possible movement. You want to verify all temporary closures are fully threaded, flanged, and fully bolted or attached with a full penetration weld, and the correct type, size and number of nut bolts and fasteners have been used. If not, you need your client to provide calculations proving that it is safe using anything less.
Also before the test you want to check the pressure gauge to ensure that it's within calibration and properly rated. You want to verify that the pressure test setup is adequate for the test pressures. Look at the manufacturer data sheets for each component of that pressure test setup so you can verify that all those components within it are acceptable for the test pressure.
Ensure that there is a provision for venting the object properly. If this is not done correctly, this could have a catastrophic result. Basically you can turn a hydrostatic test into a pneumatic test.
Keep all nonessential personnel away from the testing area by use of information, warnings and barriers.
Any hoses that are used should be inspected prior to use and contain whip checks to prevent injury should they fail.
Conduct a pre-job briefing so that all personnel involved in the test are on the same page. Everybody should know what the hazards of this test are, where the danger zone is, and what their role is.
The test should be conducted with water not less than ambient temperature but never less than 70 degrees Fahrenheit to prevent brittle fracture.
Now we are moving on to during the test. Stand at a safe distance or behind suitable shielding. Never stand in the line of fire. If visual cannot be done from a safe distance, then remote visual options should be considered.
The pressure is to be increased incrementally. That way you can make sure that the pressure gauge is working appropriately and that the object has stabilized.
You should hold the test object at that pressure for at least ten minutes or the code-required minimum, and then it gets reduced. And only after that reduction should the inspection be made.
You are still not safe. After the test you need to follow lock-out, tag-out procedures for the safe dissipation of energy. Test plugs and temporary closures should only be removed when the pressure is at zero to prevent injury. Verify that your emptying rate is not too high to create a vacuum. Utilize drain valves as appropriate in appropriate places, and make sure they are draining properly.
Here are some common pressure test issues that we face and some safe practices that we recommend.
If the pressure gauge is not working, the correct answer is to not keep pressure, right? It isn't, oh, I can't read the pressure gauge, it's not reading, keep adding pressure. Stop. You need to stop adding the pressure. Release the pressure to zero, then move up on the object and determine where the leak is or where the problem is.
Never send somebody in to tighten up a fitting or something while the object is under pressure. You could be signing their death warrant. You are basically putting them in the danger zone, and what's going to happen if you start torqueing that down, and it shatters? You are either seriously injuring somebody or killing them. Reduce the pressure to zero before sending somebody in. Then figure out where the problem is and tighten it up. Or utilize close visual cameras that can zoom in and figure out where the leak or problem is.
Another issue that we have encountered is this test setup I've mentioned already. We have clients who use this test setup over and over again, but they are always looking at the object and the connections from the test setup beyond. They don't look at this actual setup. So we really recommend that they have a manufacturer's data sheet on each component of that test setup so that it can be verified for each test pressure and make sure that it's adequate.
Those responsible for the test should state how the item under test can be safely energized, monitored, vented, or test medium discharged without placing any people in that danger zone. Those involved in the test should maintain respect for the full potential of that hazard. Stored energy many times is equated to TNT, right?
So what is the solution? It is a professional and ethical responsibility for us to keep those involved in the tests safe while this test is being conducted. Allow your personnel to speak up and raise their concerns that affect them. If you are the person, you speak up. You may save your life or that of someone else.
Share your incident history so that we can learn from the lessons learned of each person. I know that people do not want to have to share incidents involving a fatality or a serious injury, but we are never going to learn if you don't share that information. We need to know what is happening, and we need to know what the solution is. If we can share that information, we can save people's lives moving forward.
What is being done about it? I know that they have developed an ANSI Standards Committee. I know that IMechE has hosted a conference associated with pressure testing that I attended in December of last year, and I know that they are planning to host more. And I think it's such a serious topic that you are going to see pressure testing conferences and forums in the future.
I want to end by saying pressure testing can be done safely by following controlled procedures. Do not be complacent. Do not do it ad hoc. If you can put a procedure and a program around it for each and every test, this can be done safely, and we can prevent people from being hurt or killed.
MS. EHRMANN: Any questions?
PARTICIPANT: Would the entire procedure you put together for best practices be available electronically?
MS. EHRMANN: I am trying to get that approved by legal, but as soon as it's available, I will make it available to you.
PARTICIPANT: I appreciate it.
MS. EHRMANN: Yes.
PARTICIPANT: What does IMechE stand for?
MS. EHRMANN: It's the Institution of Mechanical Engineers—it's in England.