Polymer Use for Boilers and Pressure Vessels
Print Date: 8/20/2025 1:19:09 AM
Dr. Robert Grimm
Edison Welding Institute (EWI)
Category: Operations
Summary: The following article is a part of the National Board Technical Series. This article was originally published in the Summer 2001 National Board BULLETIN.(4 printed pages)
Normally when we think of very hot or even boiling liquids and pressure vessels, we think of metallic containers. The use of plastics for these applications is not the first thing that comes to mind. However, plastic pressure vessels surround us and are so common we may not notice them. Some of them operate at elevated pressures and temperatures. A few examples include:
Automotive radiators and hoses. These operate for extended periods of time at temperatures above 100°C (212°F) and at least 20 psi pressure. Usually the hoses are of a rubber or elastomer composition (composite) with reinforcing fibers of glass or highly heat-resistant polymers. Headers in radiators can be molded from glass-reinforced nylon.
Plastic plumbing in houses. While domestic plumbing is mostly polyvinyl chloride (PVC) and is seldom operated at temperatures above boiling, it does operate with hot water (60°C, 140°F) and pressure ratings around 570 kPa (85 psi). Chlorinated PVC (CPVC) has even better heat resistance than PVC (almost 90°C, 190°F at 330 kPa or 50 psi) and is another common plumbing material.
Plastic beverage bottles. While this application is not at high temperature, the pressure load on the wall is substantial when it has freshly carbonated beverage in it. This is all the more substantial when one realizes that the walls are very thin and the contents of this pressure vessel are clearly visible.
Composite pressure tanks. These are built to hold natural gas for transportation applications. These withstand high pressures, corrosive environments, and are resistant to impact.
Rocket motors. While they are not everyday applications, rocket motors, such as the ones that push the shuttle into orbit, are made from polymers and continuous reinforcing fibers wound into vessels that must withstand very high pressures.
Polymers (plastics) have advantages over metals in the construction of vessels. They can often be made easily by taking a gob of molten plastic and blowing it up like a balloon into a molded cavity. Beverage bottles are made this way, spewing out of the bottle-making machines in what almost appears to be a continuous stream. Polymeric structures are usually lighter in weight than metal ones. When blow-molded, the atomic chains of the polymer become biaxially oriented and much stronger than the parent polymer. Very importantly, they do not corrode as readily as metals.
For the application to boilers, there are some properties of polymers that make them different and, perhaps, less desirable than metals. Polymers are not as strong under tensile loads and they do not resist high temperatures as well as metals do. Moreover, polymers do not conduct heat well, and most do not conduct electricity at all. The lack of thermal conduction can be overcome by adding thermally conductive materials to the polymer formulation.
While further descriptions of polymer behavior follow, it is useful to understand at least on a basic level why polymers and metals are different and how these differences affect properties. Polymers are made from chains of atoms instead of atoms. In understanding the chain nature of polymers, it is important to note that if a carbon atom was about 40 cm in diameter (12 inches) instead of 10 -8 cm, a polyethylene chain, stretched straight, would be about 3 km (2 miles) in length. For something like ultrahigh molecular weight polyethylene, the length could be 30 km (20 miles). That is why molten polymers form a viscous gum while molten metals are runny liquids.
There are two broad classifications of polymers as shown in Figure 1.
FIGURE 1
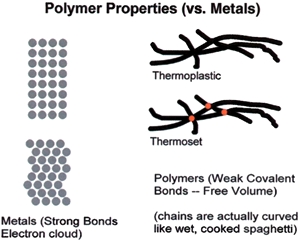
Thermoset
In thermosetting polymers, the individual chains are often short, but they are all interconnected through strong chemical bonds. Conceptually, they can be considered as three-dimensional fishnets. These thermosetting polymers are formed in heated molds and, once formed, they will not melt again. When heated excessively, they can become “cheesy” and then undergo a slow, smoky decomposition. Some examples (and long-term heat-resistance temperatures) include: epoxy (90° to 180°C, or about 190° to 350°F),2 phenolic (150° to 260°C, or 300° to 500°F),3 and rubber (100°C, or 212°F and higher). As the number of interlinks increases and/or the distance between them decreases, the bulk polymer increases in thermal resistance but becomes more brittle.
When the number of links is low or the distance between them is large, they can be heated and stretched as they cool. On reheating, they shrink back to the unstretched state (shrink-wrap).
Thermoplastic
Thermoplastic polymers constitute the second class. These can be likened to a mass of spaghetti noodles since the chains are not irreversibly connected to other chains. Heat is normally used to reverse chain interactions. Thermoplastics form glasses at lower temperatures in which the chains are not able to move very much. Above a temperature called the glass transition temperature (Tg), segments of chains can start to move in sort of a “crankshaft” motion.4 If thermoplastic polymers do not have crystalline regions, increasing temperatures will increase this motion until the mass becomes fluid enough to mold and shape. On cooling, viscosity increases until the Tg, when it again forms a glass. Typical polymers in this category (amorphous thermoplastic) include polystyrene, acrylic, polycarbonate and many others. They are often transparent.
Some thermoplastic polymers form regions where the chains fold into highly ordered crystals. These thermoplastics are called semicrystalline because the level of crystallinity varies widely, depending on the polymer and how it is processed (it commonly varies even within the thickness of a molded part, depending on the cooling rate). Crystals behave as thermally reversible crosslinks, and they have definite melting points. Semicrystalline thermoplastics tend to retain some physical properties until the melting point where the mass becomes, at once, fluid enough to mold and shape. Examples of semicrystalline thermoplastics include: polyethylene, nylon, polypropylene and many others. Figure 2 shows different forms of polystyrene and how the tensile modulus varies with temperature.
FIGURE 2
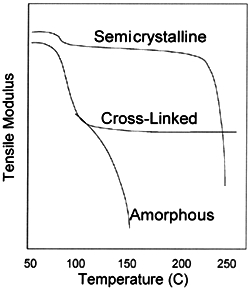
Polymers exhibit typical stress strain curves. An exception is for elastomers which exhibit reversible stress strain curves much like a spring. In general, physical properties of polymers can be modeled (Voight-Kelvin) as a combination of a spring and a dashpot. As the chains flow under stress, as Figure 3 shows, they behave like the dashpot and exhibit irreversible changes.
FIGURE 3
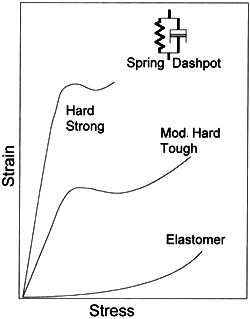
Under a constant stress, thermoplastic polymers can undergo creep. The behavior shown in Figure 4 illustrates creep behavior for one polymer as a function of the applied stress. Creep behavior is not only a function of applied stress, it is also a function of temperature. At elevated temperatures, strain occurs more rapidly. Edison Welding Institute and The Ohio State University explored this behavior several years ago in several reports on creep crack growth and developed quantitative relationships for polyethylene.5 The expected lifetime of a pressure vessel as a function of temperature, pressure, and wall thickness (which may have been reduced due to damage) were interrelated.
FIGURE 4
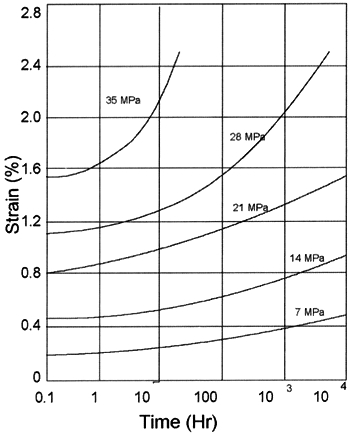
Glass reinforcing fibers are incorporated into polymers at various levels to increase tensile properties and reduce the tendency to creep as well. Levels up to 30% glass fiber (approximately 1 mm long) are common.
As with thermosetting polymers, thermoplastics have a wide range of physical properties just because of differences in molecular structure. Polyethylene (PE) comes in a wide range of grades including LDPE (low density), LLDPE (linear low density), MDPE (medium density), HDPE (high density), and UHMWPE (ultrahigh molecular weight). A few grades of polyethylene have been standardized and one, PE3408, is used for natural gas pipelines. According to ASTM 2837, it has a melting point of 124°C (250°F), and at 24°C (76°F), it must withstand a hydrostatic load of 10.7 Mpa (1.53 ksi) after 100,000 hours.6 Its design stress is 5.6 Mpa (800 psi).
Polyethylene is one of the lower-melting thermoplastics. The table lists a few thermoplastics and some of their thermal properties.
Polymer Name |
Melting Point |
HDPE Polyethylene |
124°C (250°F) |
Nylon-6,6 |
240°C (464°F) |
Polysulfone |
Glass transition temperature 220°C (428°F).
At 148°C (300°F) maximum working stress of 13 Mpa (1900 psi). |
Polyphenylene Sulfide |
300°C (575°F) |
Liquid crystal polymers |
400°C (750°F) |
While polymers have many attractive features, they also show some sensitivity. While metals can rust, polymers can undergo oxidation (they can be stabilized depending on the formulation) and embrittlement. Sunlight and other forms of radiation can also cause cross-linking and embrittlement. To counter this challenge, many polymers that are exposed to sunlight are colored black. The black absorbs the radiation at the surface and the underlying material is protected. Over long periods of time, microbes can attack some polymers and, like metals, they can be damaged by exposure to corrosive chemicals and environmental agents.7
Another feature of polymers is that they are permeable to gases. As Figure 5 shows, there are gaps where the chains overlap and small molecules such as water, oxygen, and carbon dioxide can travel through them. This is why plastic beverage bottles are not good for long storage of carbonated beverages since the carbon dioxide permeates through the sidewalls and the beverage becomes flat.
FIGURE 5
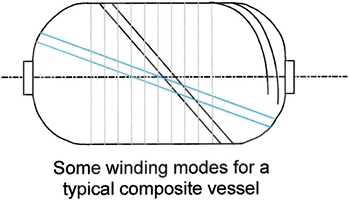
Polymers can also absorb moisture at various levels, depending on the polymer. Polyethylene and polyvinyl chloride hardly absorb any moisture at all while nylons, polyesters, and others can absorb more than 1% (w/w). The contained moisture usually has little effect on polymer properties, although it may make nylon tougher.
The use of nonmetallic materials for pressure vessels normally involves the winding of very strong, continuous filaments over an internal bladder. The internal bladder can be made from polymer or metal. Glass, carbon fiber, or several polymeric filaments are very strong in tension, and containers made this way can withstand very high pressures. Many of the design criteria of these vessels have been worked out by groups like NASA and are available to the public.8 An important feature of filament-wound vessels is that openings must not be cut into the vessel wall since this will cut the fibers and greatly weaken the vessel.
Design guides and standards for polymeric vessels can be found in several references, including:
- J.J. Koppert and A. Beukers, “Full Composite Isotensoid Pressure Vessels or How Composites Can Compete with Steel,” SAMPE Journal, Vol. 36, No. 6 (Nov.–Dec. 2000): 8–15; and
- R.J. Rashilla Jr., “All-Composite Pressure Vessels for Natural Gas Vehicle (NGV) Fuel Tanks,” Proceedings of the Conference for Advanced Composites Technologies, Dearborn, MI (Nov. 1993): 8–11.
If it is necessary to create a pressure vessel by welding end caps onto a cylinder, care should be taken to load the joints in shear and to maximize the joint area. Welding of flat disks to the end of a plastic pipe is a relatively poor way to create the vessel because the joints are subject to peel loads. In theory, better approaches involve overlap welding of cup-shaped caps onto the ends, and the best approach would be to weld shear-loaded caps that are hemispherical (or approximately so) or that have ribs on them to help reduce the stress at the center of the end cap.
In short, polymers can have a bright future in pressure vessels because of improved performance properties, low cost, and light weight. The field of polymeric vessels is still developing.
Notes
1 John DeGaspari, “Epoxy Mold,” Mechanical Engineering (January 2001): 27–28.
2 J.S. Puglisi and M.A. Chaudhari, “Epoxies (EP),” in Engineering Plastics: Engineered Materials Handbook, Vol. 2, ASM International [formerly American Society for Metals] (1988): 240–241.
3 H.J. Harrington, “Phenolics,” in Engineering Plastics: 242–245.
4 F.W. Billmeyer, Textbook of Polymer Science, 3rd Edition, John Wiley and Sons Inc. (1984): 321–323.
5 S. Popelar, C. Popelar and V. Kenner, “Creep Crack Growth in Joints of a Thermoplastic,” Edison Welding Institute Research Report MR9009 (August 1990). Also, C.H. Popelar, V.H. Kenner, S.F. Popelar and M.C. Pfeil, “Fracture Mechanics Evaluation for the Life Expectancy of Polyethylene Butt-Fusion Joints,” EWI Research Report MR9203 (April 1992). Also, M.C. Pfeil, C.H. Popelar and V.H. Kenner, “Determination of Critical J for Polyethylene Butt-Fusion Joints,” EWI Research Report MR9209 (December 1992).
6 American Society of Testing Materials Standard ASTM 2837.
7 R.B. Seymour, “Influence of Long-Term Environmental Factors on Properties,” in Engineering Plastics: 423–432 and references therein.
8 Editors of Advanced Composites Magazine, Design Guide for Advanced Composites Applications, Design Study 5, Pressure Vessels, Advanced Composites Magazine [ceased publication 1994] (1993): 44–48.
Editor's note: Some ASME Boiler and Pressure Vessel Code requirements may have changed because of advances in material technology and/or actual experience. The reader is cautioned to refer to the latest edition of the ASME Boiler and Pressure Vessel Code for current requirements.